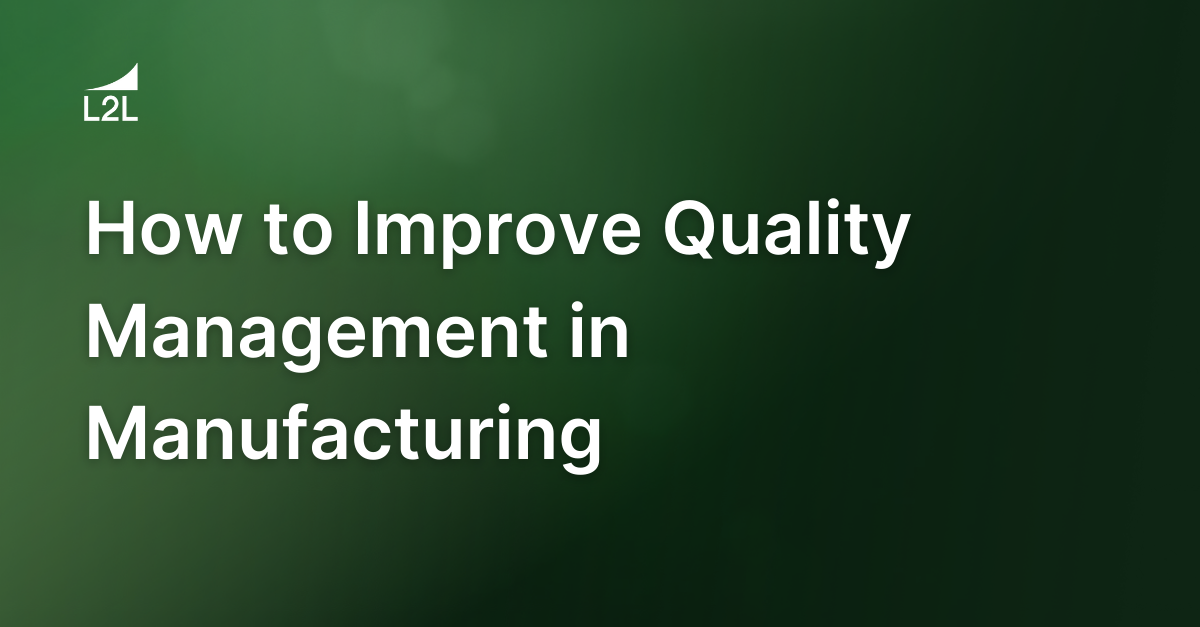
Achieving consistent quality is a cornerstone of any successful manufacturing business. However, in today's fast-paced environment, maintaining high-quality standards can be challenging.
This is where connected workforce solutions like L2L come in. These powerful platforms are designed to empower your workforce and streamline your quality management processes. By surfacing the right data at the right times, this technology helps workers identify and address quality issues faster and more effectively.
Let’s take a look at the components of quality management and how connected technology can transform quality processes in your plant.
The four pillars of manufacturing quality management
Before we dive into the quality-boosting benefits of connected worker platforms, let’s briefly define what constitutes manufacturing quality management. Simply put, quality management is built on four pillars:
1. Quality control planning
This is the blueprint for ensuring consistent quality. It involves defining what quality means for your specific products, outlining the standards and specifications they must meet, and establishing clear standard procedures for inspection and testing.
Here are some key elements of quality control planning:
-
Identifying critical quality characteristics (CTQs), the essential features of your product that directly impact performance and safety
-
Establishing clear and measurable quality control protocols, including inspection methods and acceptance criteria
-
Developing a robust documentation system to record inspections, test results, and any non-conformances
2. Quality control
Quality control is the hands-on execution of the quality control plan. It's the active process of checking products against established standards and specifications to identify any defects or deviations.
Common quality control practices include:
-
In-line inspections: Throughout the manufacturing process, quality control teams perform in-line inspections to ensure that products or components are defect-free at various stages of the production line.
-
Final product inspections: These inspections happen right before a product is shipped. They ensure that all products meet quality standards and specifications before they’re sent to customers.
-
Statistical process control (SPC): This preventive quality control method uses statistical techniques to monitor and control a production process, ensuring that it produces conforming products with minimal variation and defects.
3. Quality assurance
Quality assurance takes a preventative approach. It focuses on establishing processes and systems that ensure quality is built into the product from the very beginning. This pillar emphasizes proactive measures to minimize defects and prevent quality issues throughout the entire production lifecycle.
Key elements of quality assurance include:
-
Supplier quality management: Ensuring your raw materials and components meet your standards
-
Process improvement initiatives: Continually refining production processes to optimize efficiency and quality
-
Training and development programs: Equipping your workforce with the skills and knowledge to produce high-quality products
4. Quality improvement
Quality is not a static state; it's a continuous journey. The final pillar of manufacturing quality management, quality improvement is an iterative process that supports the ongoing pursuit of excellence. It involves analyzing quality data, identifying areas for improvement, and implementing corrective and preventative actions (CAPA) to address issues and prevent them from recurring.
Effective quality improvement involves:
-
Regularly reviewing and analyzing quality control data
-
Identifying trends and root causes of defects
-
Implementing corrective actions to address identified problems
-
Implementing preventative actions to minimize the risk of future issues
Quality management as a team effort
Every manufacturer performs quality checks to ensure products meet customer expectations. This is especially crucial in highly regulated industries like aerospace, food and beverage, and pharmaceuticals.
Traditionally, quality control has often relied on manual quality inspections or post-production checks. However, connected workforce platforms like L2L place the power of quality management directly in the hands of frontline workers, enabling effective in-process inspections that mitigate defects before they reach your customers.
Here's how to streamline and improve your quality containment processes with connected technology:
-
Establish clear, consistent checks: Develop step-by-step digital work instructions with embedded images and videos for each quality check. This ensures everyone follows the same process and reduces confusion.
-
Simplify existing procedures: Convert your existing written Standard Operating Procedures (SOPs) into digital checklists within the L2L Platform.
-
Make critical information accessible: Equip frontline workers with job-critical information, like digital quality checklists, available on the factory floor during production.
-
Unlock data-driven insights: Transforming paper-based processes into digital workflows enables you to utilize powerful tools like control charts for SPC, monitor your processes, and identify potential issues before they impact quality.
-
Automate the right actions: L2L's dispatch functionality, for instance, sends automated notifications when deviations occur. This allows for the automatic escalation of workflows and corrective actions, ensuring a timely response to quality concerns.
-
Improve data accessibility: Workers can access quality dispatch, checklists, and procedures on mobile devices, allowing them to perform checks right at production, catching defects early, and preventing rework. Alternatively, using dedicated kiosks allows operators to access and share data in a centralized place.
Data-driven quality management with the L2L Platform
L2L goes beyond simply collecting data; it empowers you to make informed decisions based on real-time insights. With our platform, you'll be able to engage your employees on the floor who often see the problems before anyone else. They're able to raise the alarm before those issues become major problems that prohibit you from delivering quality products on time.
L2L lets QA teams conduct quick, easy quality checks using an intuitive digital interface.
Here are some of the ways that L2L can help you make quality data-driven decisions:
-
Digital checklists: Checklists within L2L help users capture real-time product quality and process performance data. With up-to-date quality data, you can see which processes are in and out of control, enabling you to allocate your resources effectively and establish proper corrective actions.
-
Abnormality management: L2L makes it easy to identify quality issues and flag the right people to address them. Not only does L2L let you collect quality and process data, but it also uses that information to automatically assign corrective actions to specific teams or workers.
-
Digital SQDC: L2L’s TeamBoard keeps everyone informed about production status and daily, weekly, and monthly quality metrics, fostering a sense of ownership and accountability. This digital SQDC board also enables immediate corrective actions for identified quality issues of the day.
By leveraging L2L's innovative capabilities, you can create a culture of quality that permeates every aspect of your organization. In turn, this leads to improved product quality, reduced waste, and ultimately, increased customer satisfaction.
If you're ready to empower your workforce and achieve operational excellence, reach out to sales@l2l.com or schedule a demo with one of our representatives today!
Revisions
Original version: 20 August 2024
Written by: Evelyn DuJack
Reviewed by: Daan Assen
Please read our editorial process for more information
Subscribe to Our Blog
We won't spam you, we promise. Only informative stuff about manufacturing, that's all.