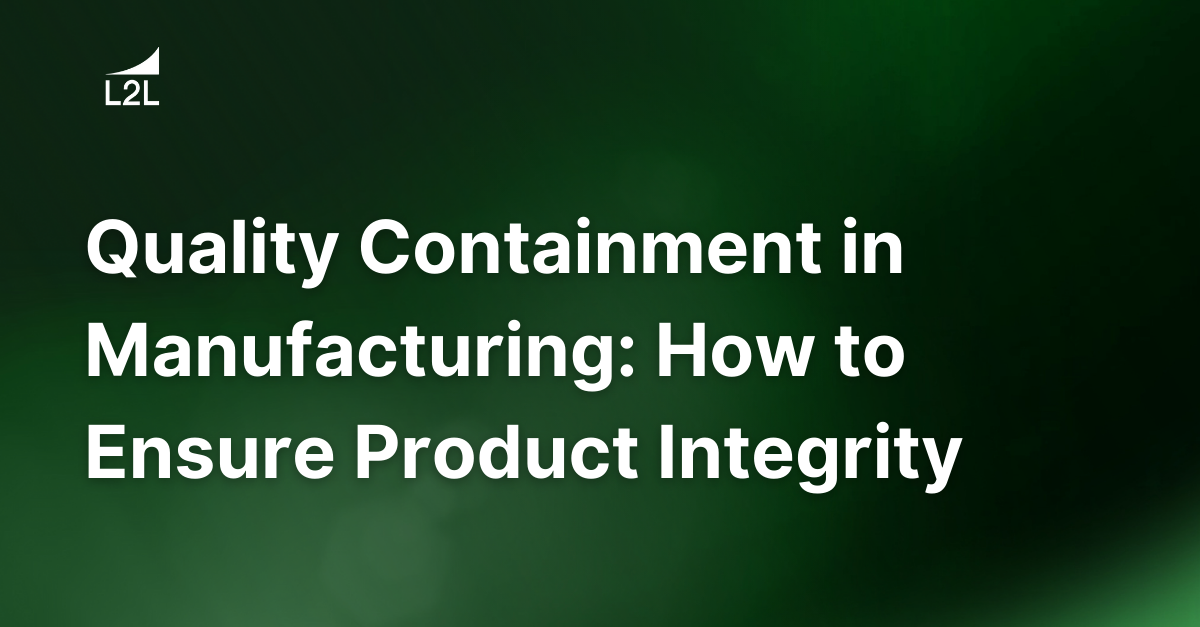
Quality containment is not just a checkpoint in the manufacturing process — it’s a series of measures designed to identify, manage, and mitigate defects before products leave the factory floor.
Effective quality containment measures are crucial for maintaining product integrity and, ultimately, customer satisfaction.
In this article, we will explore the key components of a quality containment system, effective implementation strategies, and application examples across various industries. To wrap things up, we’ll show you how manufacturers use connected workforce platforms like L2L to maintain the highest standards of quality.
The fundamentals of quality containment
Quality containment operates at various stages of the manufacturing cycle, from the procurement of raw materials to the final stages of production. By integrating quality checkpoints throughout the production process, manufacturers can isolate and address potential issues without disrupting the overall workflow.
An effective quality containment system is built on several key components:
-
Standardization: Implementing standardized processes and quality checks that every product must undergo before advancing to the next stage of production.
-
Documentation: Maintaining detailed records of quality checks, issues identified, and resolution steps taken. This not only helps in pinpointing recurring problems but also aids in regulatory compliance.
-
Employee training: Ensuring that all personnel are trained in quality assurance practices. This includes how to detect defects and what to do once a defect is detected.
-
Technology integration: Utilizing automated inspection systems and AI-powered defect detection tools to enhance the accuracy and efficiency of quality checks.
-
Feedback loops: Establishing mechanisms for feedback on the manufacturing process, allowing for continuous improvement based on real-time data and analytics.
This process not only protects consumers but also safeguards manufacturers against costly recalls and reputational damage.
Strategies for implementing quality containment
Quality containment can operate at three different levels. We explore each below.
Preventive measures
Preventive measures in quality containment focus on reducing the likelihood of defects in the first place. This happens right from the design and planning stages:
-
Design optimization: The design phase holds the key to preempting many quality issues. Utilizing advanced simulation tools and CAD software, designers can predict potential problems and modify designs to enhance manufacturability (minimizing part count, designing for efficient joining, etc.).
-
Material quality: Selecting high-quality materials is crucial for product integrity. Materials should be sourced from reliable suppliers and tested for compliance with industry standards. This ensures that the manufacturing process starts with a foundation capable of achieving the desired quality outcomes.
-
Standard operating procedures (SOPs): Be it product designers, supply chain managers, maintenance technicians, or line workers, all employees should follow best practices (a.k.a. standard work) to avoid actions that can lead to product defects.
Detection systems
Effective detection systems allow manufacturers to identify and address defects before products reach the final quality assurance stage. These systems encompass a range of inspection, testing, and monitoring techniques, often supported by cutting-edge technologies.
Examples include:
-
Automated Inspection Systems: These systems use tools like cameras and sensors to conduct real-time inspections of products on the assembly line. Automated inspection helps detect physical defects, dimensional inaccuracies, and functional discrepancies that might not be visible to the naked eye.
-
Statistical Process Control (SPC): SPC employs statistical methods to monitor and control a process. This helps ensure the process operates at its full potential and produces more conforming products with fewer defects.
-
Regular audits and checkpoints: Setting up regular checkpoints throughout the production process allows for early detection of non-conformity. Implementing a simple visual alert system like Andon can do the trick, especially if you’re relying on line workers to spot and report production issues.
-
Intelligent technology integration: AI in manufacturing is gaining widespread use. One of the reasons why is that machine learning algorithms can now predict potential failure points and irregularities by analyzing data collected from the manufacturing process. These predictive analytics tools are becoming increasingly crucial in preemptive defect detection.
Reactive measures
Even with comprehensive preventive measures in place, some non-conformities are bound to happen. Manufacturers need to have a clear set of steps to immediately contain and rectify the issue once defects are detected.
Here are the typical quality containment action steps:
-
Immediate isolation: The first step is to isolate the affected product or batch to prevent further processing or mixing with unaffected products. This helps minimize the scope of the problem.
-
Root Cause Analysis (RCA): Once the defective items are contained, it's crucial to conduct a thorough investigation to determine the root cause of the defect. The analysis often involves cross-functional teams and may utilize tools like the Five Whys or fishbone diagrams to pinpoint the underlying issues.
-
Corrective actions: Based on the findings from the root cause analysis, appropriate corrective actions are implemented to fix the defect. This might involve adjustments in the manufacturing process, updates to equipment, or changes in material usage.
-
Preventive actions: To prevent recurrence, the lessons learned from the incident are used to refine existing processes. This might include retraining employees, updating SOPs, or enhancing quality control measures.
-
Documentation and follow-up: All steps taken in response to the defect, from detection to corrective actions, should be thoroughly documented. This is crucial for regulatory compliance and continuous improvement efforts. Regular follow-ups ensure that the corrective measures are effective and that no further issues have arisen.
Quality containment examples from various industries
While the principles of quality containment are broadly applicable across all manufacturing sectors, the exact prevention and detection measures employed will vary depending on the specific demands and standards of each industry.
Automotive manufacturing
The automotive industry employs a multi-faceted approach to quality containment that integrates advanced technologies and rigorous testing protocols:
-
Robust design and testing: Using computer-aided design CAD software to simulate vehicle performance under various conditions and employing crash testing to ensure safety standards are met.
-
Supplier quality management: Manufacturers require suppliers to adhere to strict quality standards, and they often conduct audits and require certification processes to ensure these standards are maintained.
-
Assembly line monitoring systems: On the assembly line, real-time monitoring systems are used to check the fit and function of parts as vehicles are assembled. These systems use sensors and cameras to immediately detect deviations from set specifications.
-
End-of-line testing: Once a vehicle is assembled, it undergoes end-of-line testing, which includes a series of automated and manual checks. These tests cover everything from engine performance to electronic systems functionality.
-
Traceability and data analysis: Automotive manufacturers utilize sophisticated traceability systems to track components back to their origin. This is crucial for quickly addressing any defects that may appear and for conducting thorough recalls if necessary.
Furniture manufacturing
Quality containment in furniture manufacturing often combines traditional craftsmanship with modern manufacturing processes:
-
Material quality checks: Quality containment begins with the rigorous inspection of raw materials. Wood, metals, fabrics, and other materials are tested for defects and durability to prevent issues such as warping, rusting, or wear over time.
-
Precision in production: Automated cutting and assembly machines are calibrated regularly to maintain accuracy, while skilled craftsmen are employed for finer details and finishes.
-
Fit and finish standards: Furniture manufacturers use strict checks for alignment, stability, and finish quality to ensure that each piece meets the aesthetic and functional standards expected by customers.
-
Environmental and stress testing: Furniture can be subjected to environmental and stress testing to simulate long-term use and exposure to various climates. This helps identify potential failures in joints, materials, or finishes before products are shipped to consumers.
-
Continuous improvement feedback loop: Customer feedback and return data are analyzed to identify common defects or areas for improvement. This information is fed back into the design and production processes to enhance future product quality.
Pharmaceutical manufacturing
Pharma manufacturers must adhere to rigorous regulatory standards and employ advanced quality containment measures to ensure the integrity of every product released to the market:
-
Strict regulatory compliance: Organizations like the FDA and EMA (European Medicines Agency) have regulations that govern every aspect of pharmaceutical production, from raw material sourcing to final product testing.
-
Good manufacturing practices (GMP): GMP guidelines are followed to ensure products are produced and controlled according to quality standards. This includes detailed documentation for every step of the manufacturing process to ensure traceability and accountability.
-
Advanced testing: Pharmaceutical products must undergo extensive testing to ensure purity, potency, and absence of contaminants. Techniques such as gas chromatography and mass spectrometry are commonly used.
-
Environmental monitoring: The manufacturing environment is strictly monitored for parameters such as air quality, temperature, and humidity. This helps prevent contamination and ensures the stability of products throughout the manufacturing process.
-
Risk management and quality audits: Risk management strategies are implemented to assess and mitigate potential quality risks throughout the production cycle. Regular quality audits are conducted to ensure continuous compliance with both internal and external quality standards.
Because of the nature of pharma products, quality containment is effectively prescribed through regulatory requirements.
How L2L facilitates early quality containment
Catching non-conformances as early as possible in the production process is essential for maintaining a competitive edge and improving your bottom line.
The L2L Connected Workforce Platform is designed to integrate seamlessly with existing manufacturing operations. It offers a range of tools and functionalities that support, among many other things, early and effective quality containment.
L2L provides real-time monitoring capabilities, allowing quality managers to detect and address issues promptly. The platform's advanced data analytics enable predictive maintenance and proactive quality control, while its collaboration features ensure swift problem resolution between floor workers and managers. Additionally, L2L’s customizable alerts keep users informed of quality deviations, and its detailed reporting features support regulatory compliance and continuous process improvement.
Here's what some of those features look like in action:
If you're ready to leverage this functionality on your plant floor, schedule a quick product demo or reach out to sales@l2l.com with any questions you might have.
Revisions
Original version: 18 July 2024
Written by: Evelyn DuJack
Reviewed by: Daan Assen
Please read our editorial process for more information
Subscribe to Our Blog
We won't spam you, we promise. Only informative stuff about manufacturing, that's all.