Move fast and fix things
L2L connects operators and technicians with the critical information and guided workflows they need to find, fix, and prevent issues.
Clarity on who, what, when & where
Make machine maintenance easier and more effective. World-class maintenance depends on a shared view of your processes.
-
Unskilled peoplePeople without the right skills cause downtime.
-
No collaborationDisconnected actions between teams.
-
Ah hoc sparesQuit searching, start working.
-
Lacking standardizationLimited access to how-to information.
-
Unclear root causesReactive maintenance keeps you putting out fires all day.
A disengaged workforce lacking skills and knowledge because of inefficient training decreases productivity.
No connection between teams on the tasks that need to be done or actions that need to happen. No alerts and no digitized work.
L2L’s Spares Management system reduces delays caused by locating the right spare parts. Teams quickly access the parts they need with detailed inventory management, machine history, and repair data.
Without standards, continuous improvement is impossible. Profitability naturally takes a hit if you consistently miss production targets because of delays.
Frequent stops, inefficient changeovers, and scheduling conflicts - usually caused by a lack of root cause identification and ineffective preventive maintenance.
-
Unskilled peoplePeople without the right skills cause downtime.
A disengaged workforce lacking skills and knowledge because of inefficient training decreases productivity.
-
No collaborationDisconnected actions between teams.
No connection between teams on the tasks that need to be done or actions that need to happen. No alerts and no digitized work.
-
Ah hoc sparesQuit searching, start working.
L2L’s Spares Management system reduces delays caused by locating the right spare parts. Teams quickly access the parts they need with detailed inventory management, machine history, and repair data.
-
Lacking standardizationLimited access to how-to information.
Without standards, continuous improvement is impossible. Profitability naturally takes a hit if you consistently miss production targets because of delays.
-
Unclear root causesReactive maintenance keeps you putting out fires all day.
Frequent stops, inefficient changeovers, and scheduling conflicts - usually caused by a lack of root cause identification and ineffective preventive maintenance.
Keep your assets running smoothly
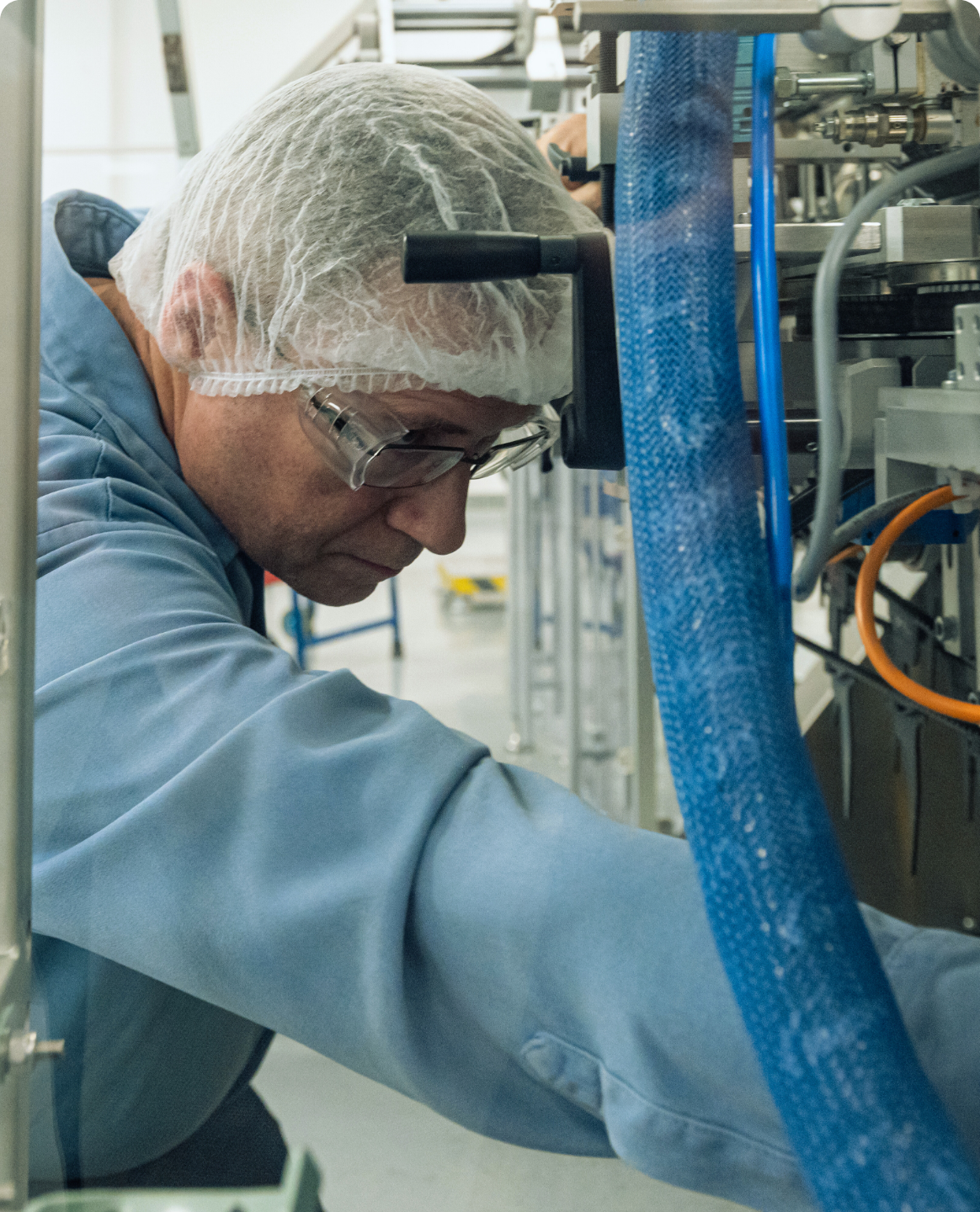
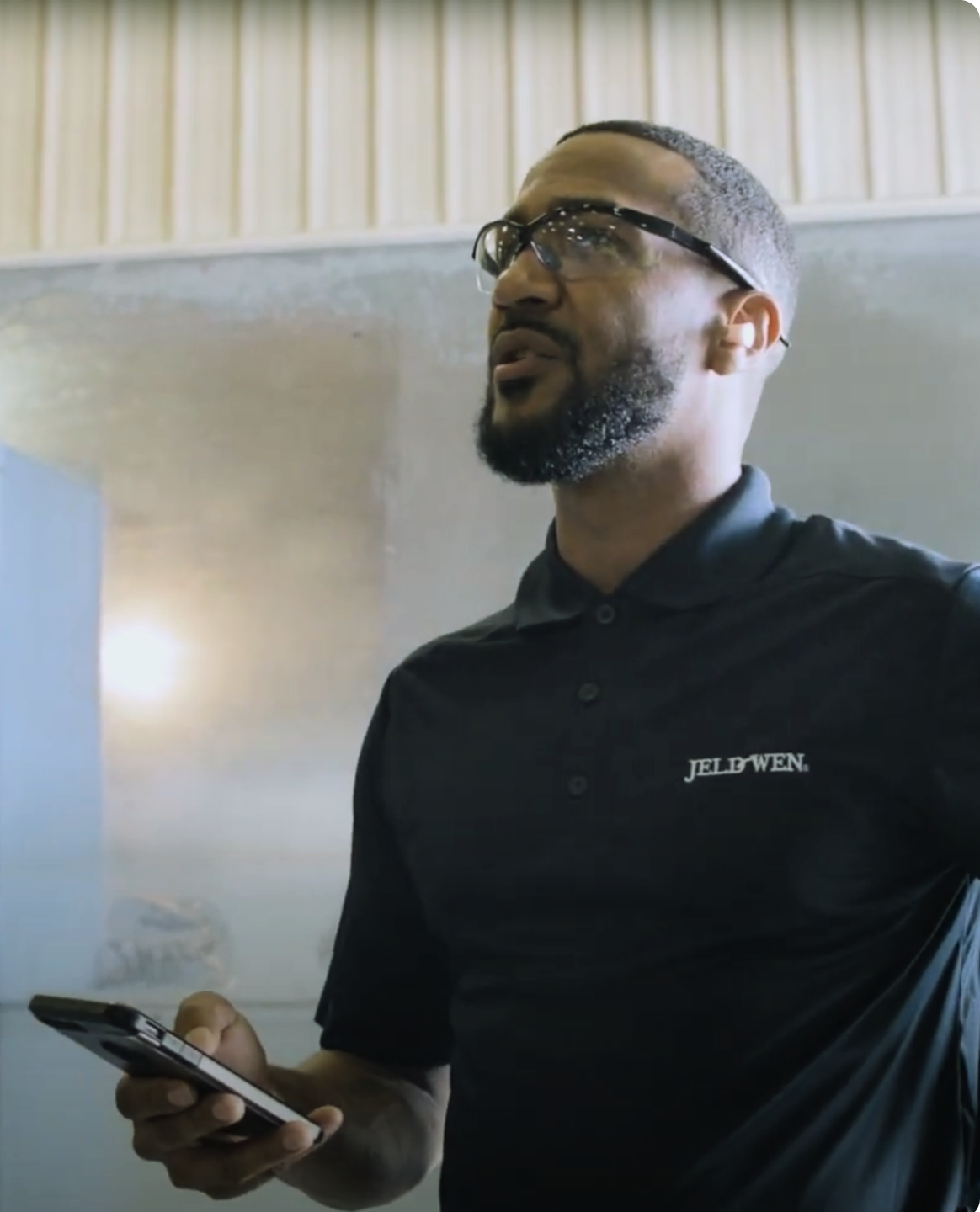
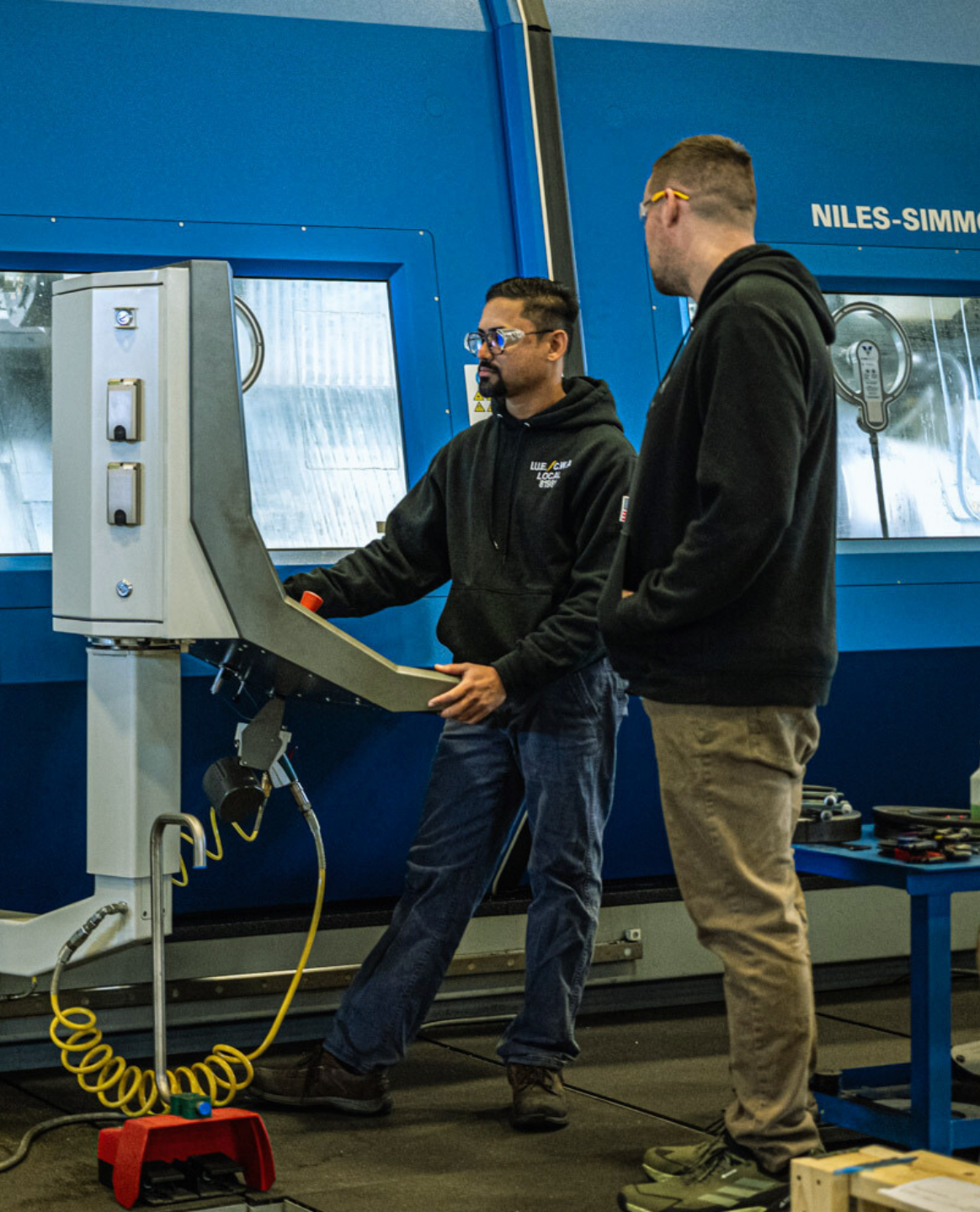
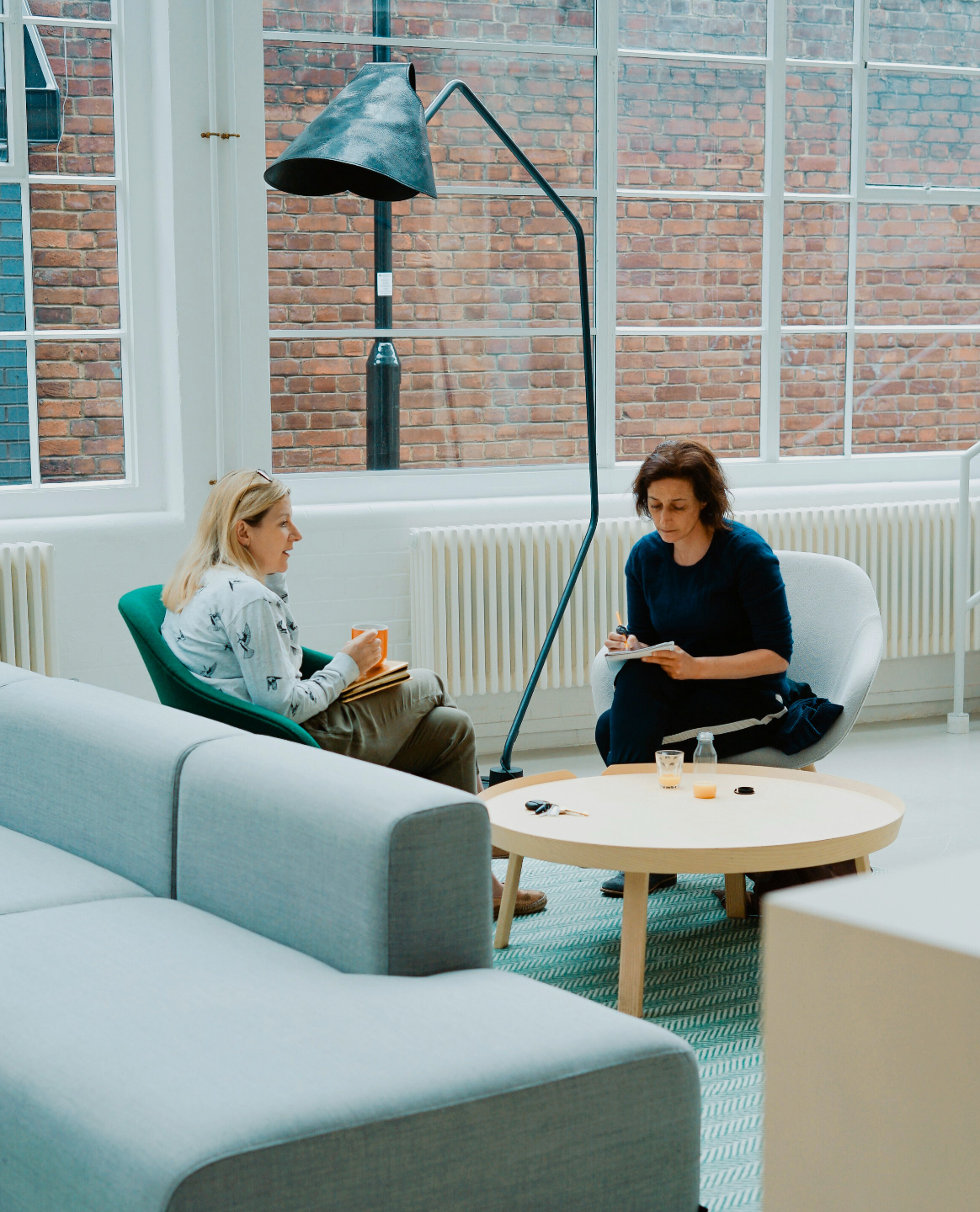
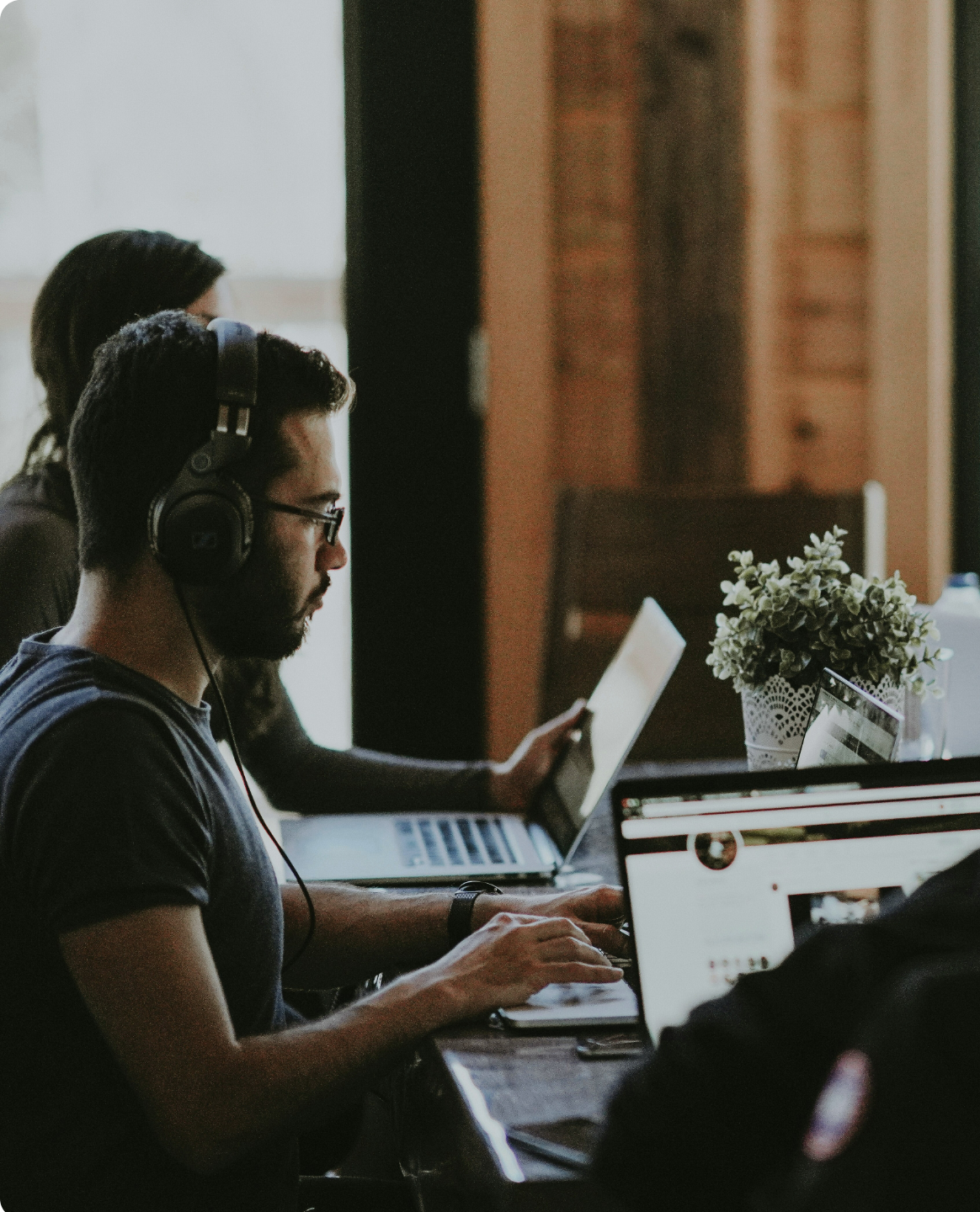
L2L Dispatch connects technicians with operators in real time to solve machine abnormalities before they become serious. Technicians take charge of preventive maintenance scheduling and task tracking with L2L to ensure machine availability and reduce unplanned downtime.
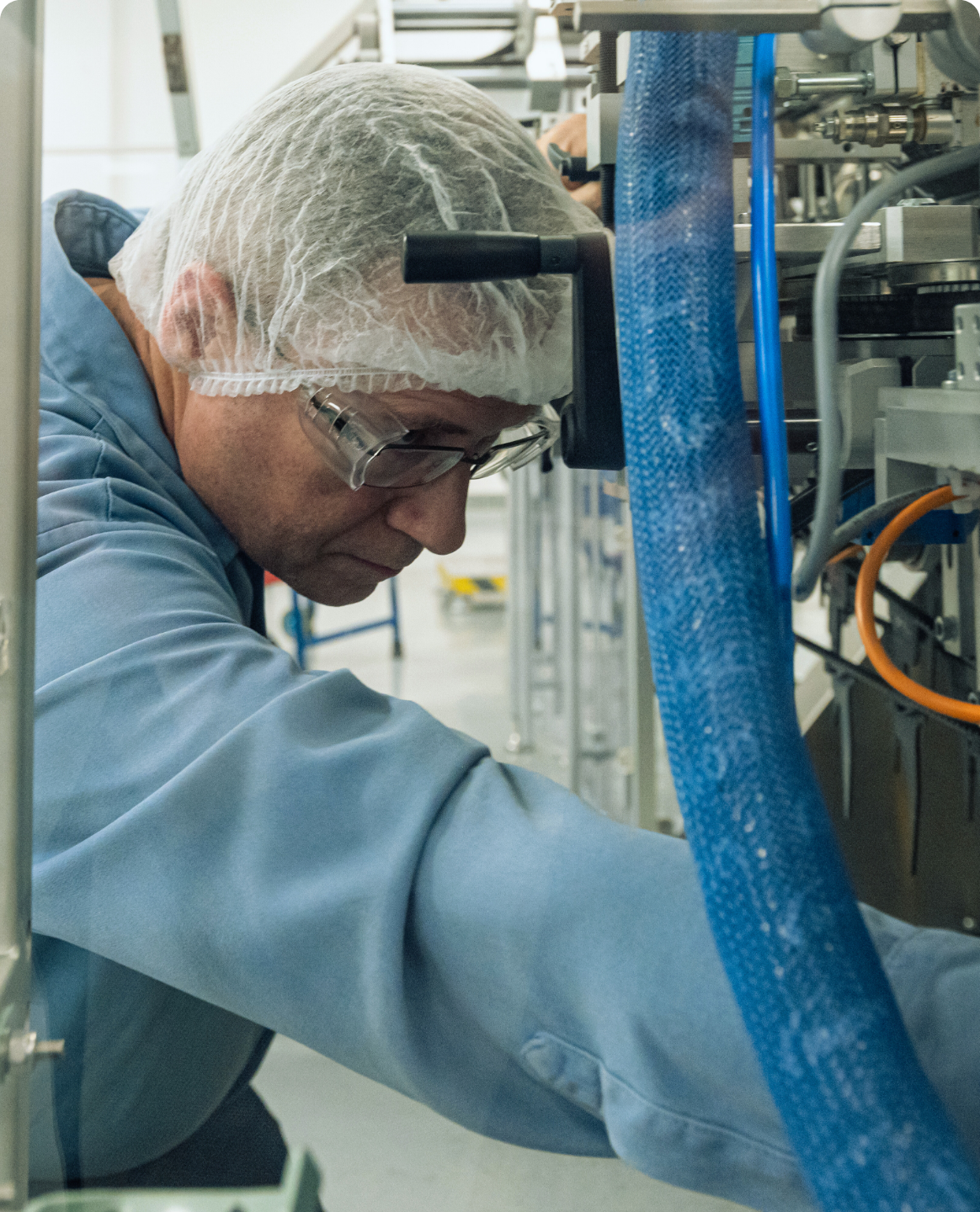
Plant leaders keep their finger on the pulse of the entire factory floor. Improve equipment availability with real-time data about machine and line health, spare parts inventory, and work orders.
Connect data with actions and tackle resource issues by identifying bottlenecks, measuring performance, and driving continuous improvement across the plant. We help you focus on the problems that matter most.
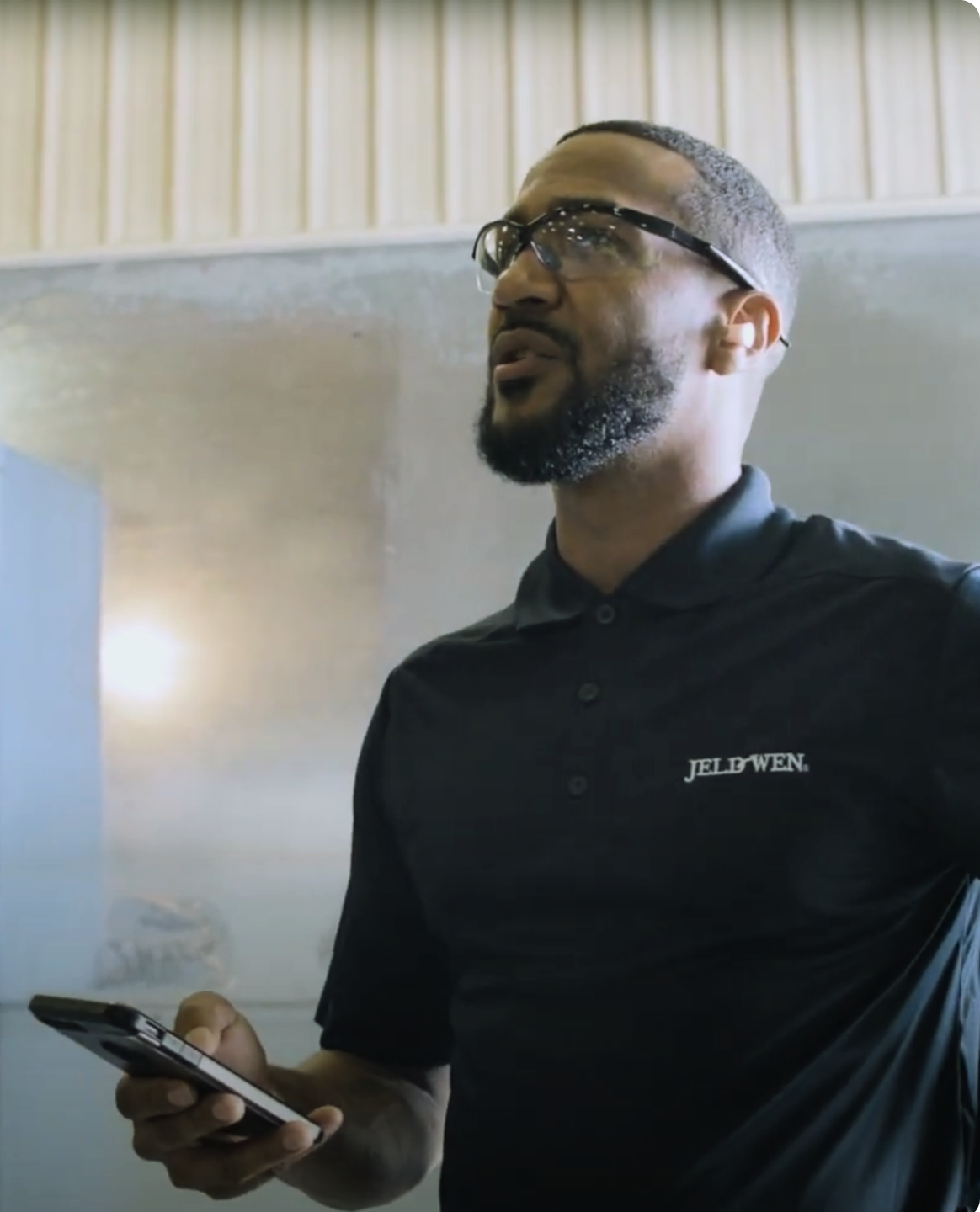
Keep productivity high across maintenance and production operations. Schedule resources, manage assets, launch work orders, order spares, and perform inspections.
Ensure that technicians and operators collaborate smoothly and always according to standard. L2L helps your newest worker perform like your most tenured team member.
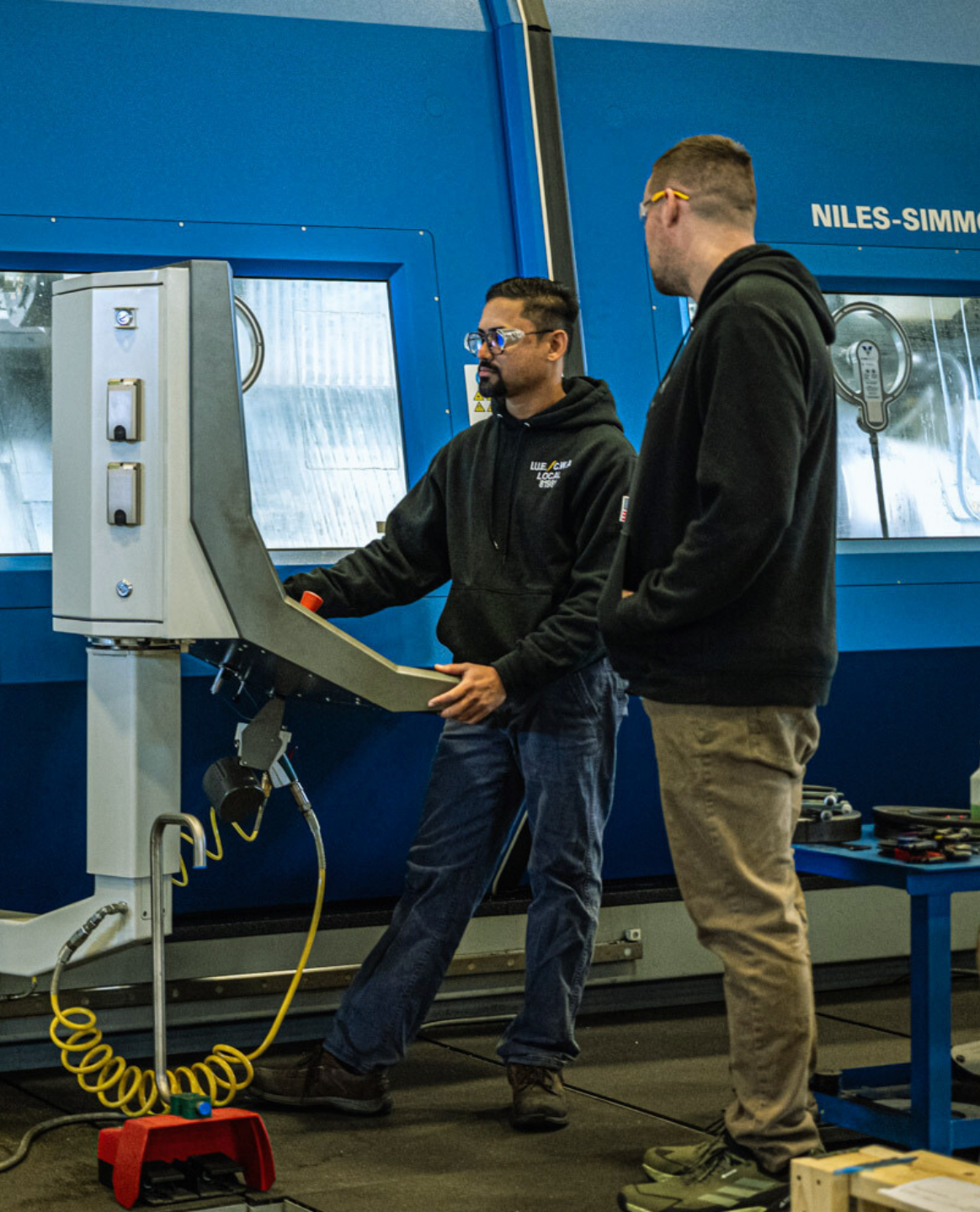
Understand and compare plant performance at a glance with L2L Business Intelligence to improve your bottom line. L2L gives leadership real-time data to make faster, better decisions, meet demand, and ensure uptime and productivity across sites.
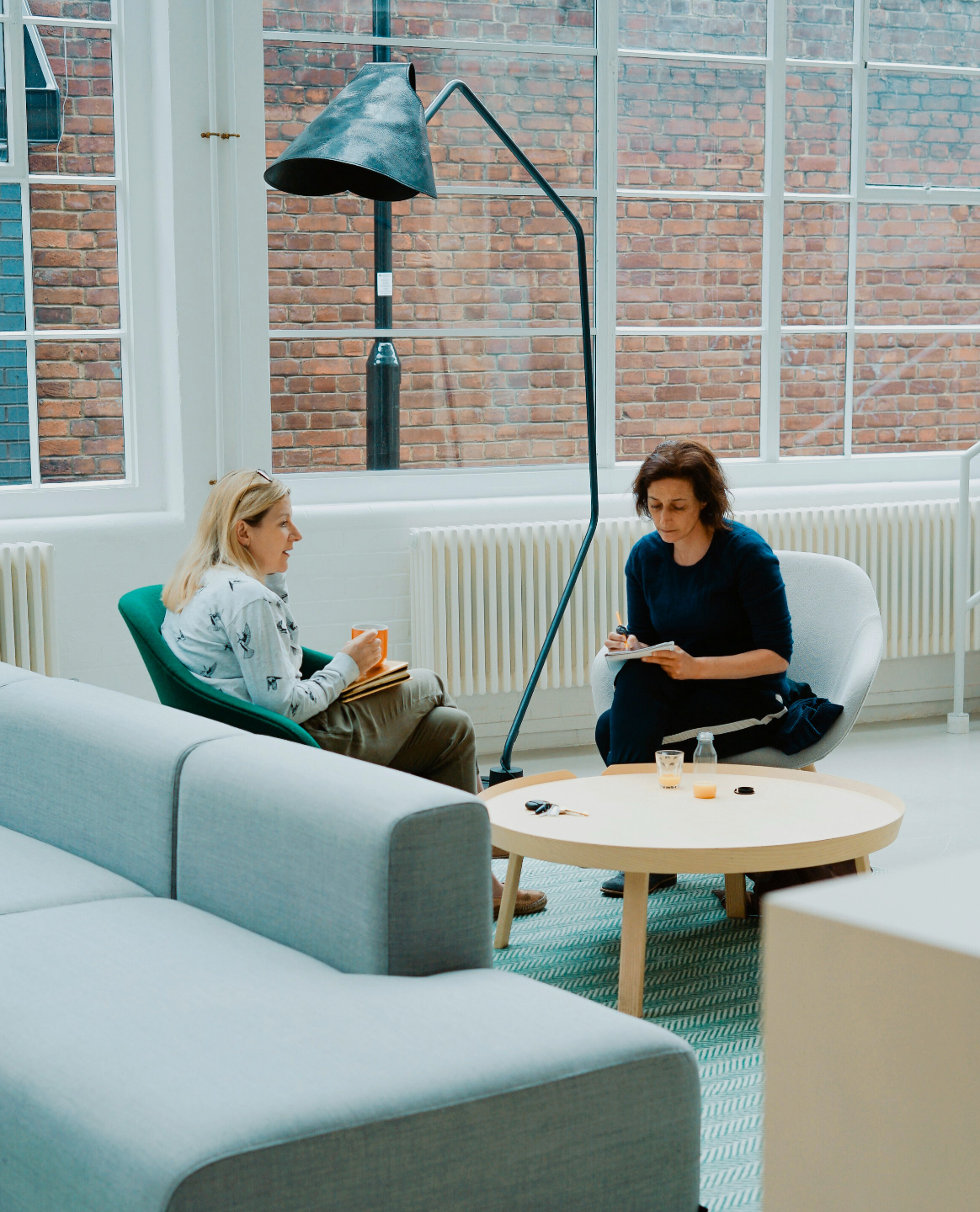
Our promise: Clear ROI in 2 weeks
You’ll see reduced downtime, increased productivity, better quality, and more engaged team members.
Visualize, prioritize, execute.
L2L delivers a shared view of machine health to drive operational availability while creating machine uptime.
Preventive maintenance
Frontline employees carry out preventive maintenance as planned with robust planning and scheduling capabilities, automated alerts, and detailed work instructions.
Condition-based and predictive maintenance
L2L Dispatch automatically alerts teams when pre-determined machine parameters are reached (heat, vibration, thermography) so technicians can perform corrective maintenance in time.
Spare parts and inventory
No more searching for the right part. No more wondering about a machine’s maintenance history. L2L provides a robust spare parts inventory system for simple use by frontline technicians and MRO crib attendants.
Asset management and warranty
Improve asset tracking and traceability with our EAM capabilities. Monitor past and current asset performance and cost, including details about location, condition, maintenance history, and warranty.
Work orders and task management
Coordinate all work orders from L2L’s Work Order module to ensure proper routing, cost accounting, and task execution. The entire team has clarity on what needs to be done, when, where, how, and by whom.
Inspections and SOPs
Our digital checklists and mobile work instructions deliver a clearer, more efficient way for frontline teams to perform inspections, changeovers, and CILT procedures. Control safety, quality, and settings checks on every shift.

“The system has given our employees the tools to see the highest impact opportunities for improvement and a way to visually see the impact of actions taken to address them,”
VP of Engineering and Manufacturing
“We had a static PM schedule and reactive breakdowns. We were using either Microsoft Excel, Access, or human memory to manage maintenance. The maintenance teams really like L2L. Everybody’s been quite excited about it. We feel like we’re getting value for our investment.”
Process Improvement Technician

“L2L helps our maintenance teams maintain a world-class standard. Everyone has real-time visibility into what’s happening at our plant. If we have a problem, we can quickly get to the root cause of it. L2L has not only saved us money, but it has also improved our processes and made us more productive with the resources we have.”
Corporate Maintenance Manager
Frequently asked questions
Find out how L2L enhances equipment availability, streamlines maintenance tasks, and reduces downtime for better operational performance.
How does L2L improve equipment availability?
L2L connects maintenance teams and operators with real-time data to coordinate proactive maintenance, reduce downtime, and prioritize tasks efficiently. Features like predictive maintenance and spares management ensure maximum machine uptime.
Which maintenance tasks can L2L help automate?
L2L streamlines tasks such as preventive maintenance scheduling, condition-based maintenance alerts, and inventory tracking for spare parts. Our platform helps reduce manual effort and improve overall maintenance effectiveness.
Can L2L reduce dependency on skilled technicians?
Yes, L2L democratizes maintenance tasks by providing clear work instructions, skills management tools, and accessible digital records, enabling frontline employees to perform basic maintenance while freeing technicians for more complex tasks.
Related content
Video | Dart Container Slashes Downtime and Boosts Productivity with L2L
How Purple Reduced Equipment Downtime by 54% with L2L
How ADAC Automotive Gained Real-Time Visibility Into Machine Downtime and Production Performance
eBook: Minimizing Downtime
Ready to drive equipment availability?
Discover how L2L connects your teams with real-time data and tools to reduce downtime through optimized maintenance operations.