Platform support to keep you moving
Need help? Our Support and Services team has you covered. Our Customer Support Center is your hub for troubleshooting, training, and platform feedback.
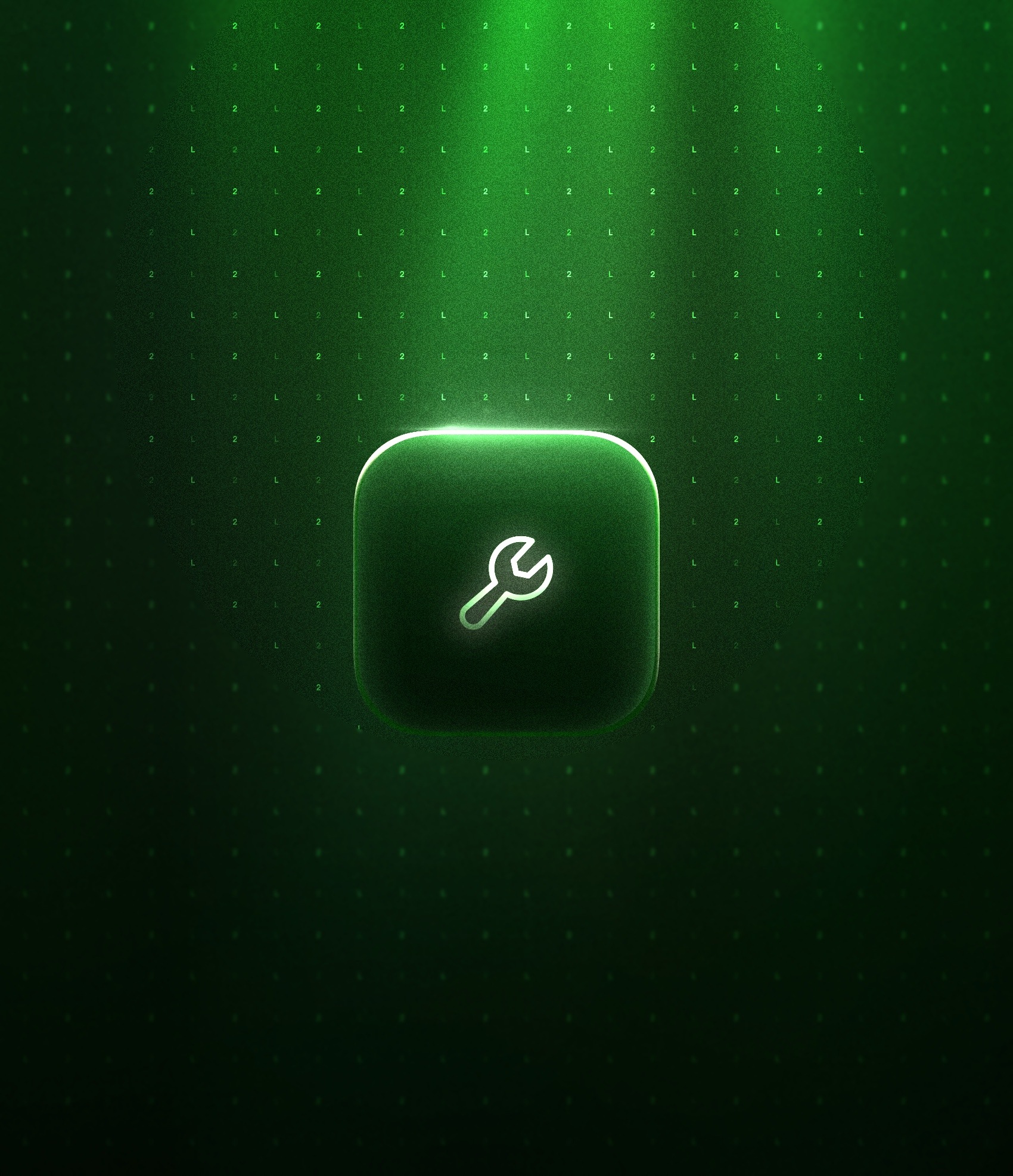
Connect with L2L customer support
Three ways to get in touch
Submit a ticket
Having trouble resolving an issue? Drop us a ticket, and we’ll get back to you in approximately 1 business day.
Chat with us
Send us a quick note with questions, concerns, or feedback on our platform and services.
Join our community
Learn from peers and dive into all topics L2L in our community.
Visit our help center
Explore our help center for more information on common issues and their solutions—and don’t forget to check out our training videos.
Before, during, and after every shift
L2L is the only platform that unifies asset management, production performance, quality control, and team collaboration into one seamless solution.

“Eliminating paper maintenance work orders has been a huge win. We have increased productivity, visibility, and prioritization. The software is easily adapted to our needs.”
Principal Owner

“L2L makes it simple to drill down through categorical data and various collected metrics and plant production information. I most often use this to synthesize scrap Paretos and report on our continuous improvement progress. L2L is an all-inclusive interface that I utilize multiple times per week with ease to pull data for our production performance.”
Project Engineer

“Pure GOLD. The strategic direction of the company is spot on. Interaction with L2L customers and L2L resources that share the same passion for continuous improvement. Very well run and coordinated. The forward-thinking vision with AI, BI, and rules-based automation is exactly where we all need to focus, and L2L has done a great job in moving quickly in these game changers.”
Vice President of Information Technology

“Great tool for managing manufacturing challenges. L2L continues to evolve and has made many improvements in the past few years. They understand the bigger picture, the manufacturing challenges, and data.”
IT Projects Engineer

“L2L has helped us locate problem areas in shipping, production, facilities, and in our own shop. An immediate and up-to-date report of what's happening and what has happened, depending on use of the program.”

“L2L is THE tool for transformation. It has everything... automated dispatches, standard work tools, data accuracy, historical data, dashboards...it's such a powerful tool!”
Plant General Manager

“L2L smart manufacturing usage in daily life. I'm able to see all production indicators to understand the status and anticipate what the result vs target defines. It gives real data to attack problems before they are creating big unexpected results.”
Become an L2L pro
This online L2L Administrator Training course guides you through the process and best practices of setting up and administering L2L software.