Worthington reduces downtime costs by $1M
Worthington is a value-added steel processor, producer of laser-welded products, and leading global supplier of pressure cylinders and accessories.
Worthington Industries uses L2L to increase visibility and efficiency across plant operations to:
-> Use real-time data to identify actionable insights for continuous improvement
-> Decrease downtime
-> Improve production floor visibility
Worthington x L2L achievements
The role of IT
"Being in IT, one of the hardest parts of unveiling software is getting that adoption up front. What we kept seeing with L2L was how user-friendly it was."
- Justin Skaggs, IT Delivery Manager
Real-time production metrics and orchestration
Worthington Industries transitioned from inefficient, manual production tracking to L2L's real-time metric system, significantly improving visibility, reducing downtime, and driving continuous improvement across multiple locations. This shift enabled faster responses to production issues and enhanced overall operational efficiency.

Before

Worthington Industries relied on ad-hoc, manual tracking of production metrics. Information was scattered across whiteboards and spreadsheets and teams struggled to identify bottlenecks or respond quickly to downtime issues.
Now
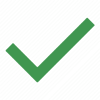
Seven locations now use L2L to view real-time metrics and orchestrate their teams. L2L collects data in real time, making it easy to tell if a line is running or experiencing downtime. Teams are more productive, react faster to downtime, can identify bottlenecks more quickly, and are improving in every area of production.

Everything our plants could do to improve efficiency, reduce unplanned downtime, drive waste out of the process, and react faster to change became even more critical to keep up with the changing market conditions.
Smart factory initiative implementation
Worthington Industries replaced fragmented, manual data tracking with L2L's Plant Digitization Platform, integrating machine data and deploying mobile tools to achieve real-time visibility and improve operational efficiency. This strategic shift, driven by a cross-functional team, aimed to reduce costs and enhance competitiveness through improved data-driven decision-making.
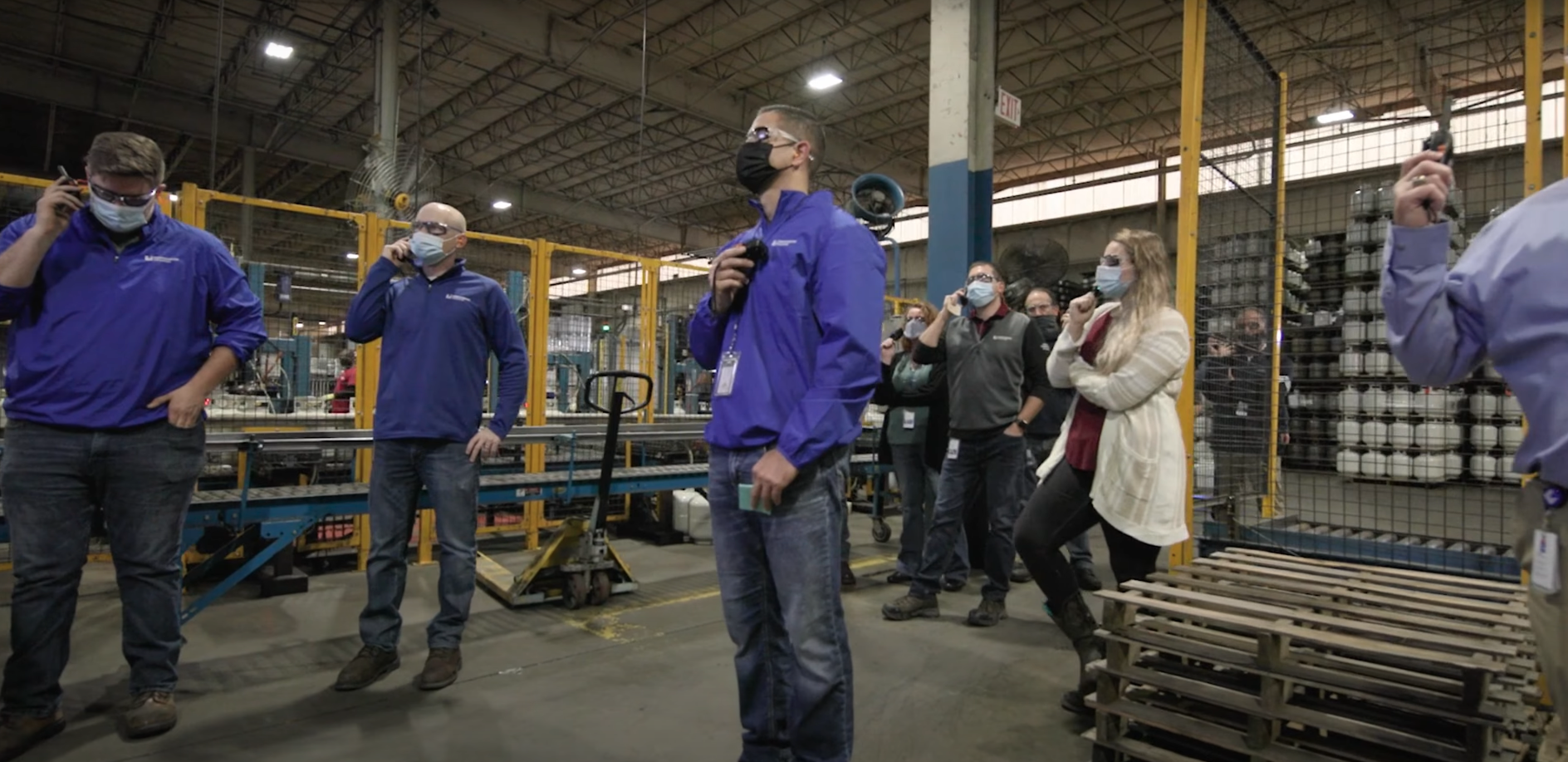
Before

Production data was tracked on whiteboards and spreadsheets, creating information silos and delayed responses to production issues.
Now
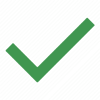
Worthington Industries implemented L2L and integrated it with machine sensors and existing systems to create a unified view of production metrics. They deployed mobile devices and wearables onto the shop floor for better team coordination.

Prior to L2L, tracking production metrics was ad-hoc, manual, and most of the time lost forever when the whiteboard was erased each day. L2L has changed that paradigm by collecting and displaying plant metrics in real time from both operators and machines. The system makes it easy to tell if each line is winning or losing throughout the day. Now we’re more productive, reacting faster to downtime, figuring out where our bottlenecks are more quickly, and we’ve been able to improve in every area of production.
The return on investment
Unplanned downtime ↓
350+ hours reduction in unplanned downtime
Cost savings ↑
$1,000,000+ cost avoidance of machine downtime
Visibility ↑
Real-time visibility across operations
Response time ↑
Collaboration ↑
The solution that shows your manufacturing problems—and fixes them too
Drive continuous improvement in availability, performance, quality, and workforce enablement.
Quickly identify problems and take action faster with L2L. Empower your teams to achieve daily wins and drive success every day.
Trusted by leading sites around the globe.