Sonoco saved $50,000
in 9 months
Sonoco is a packaging solutions company for food and household products.
With L2L, the Sonoco team has improved:
-> Reduced unplanned downtime events
-> Reduced maintenance costs
-> Improved reliability on source line and downstream production lines
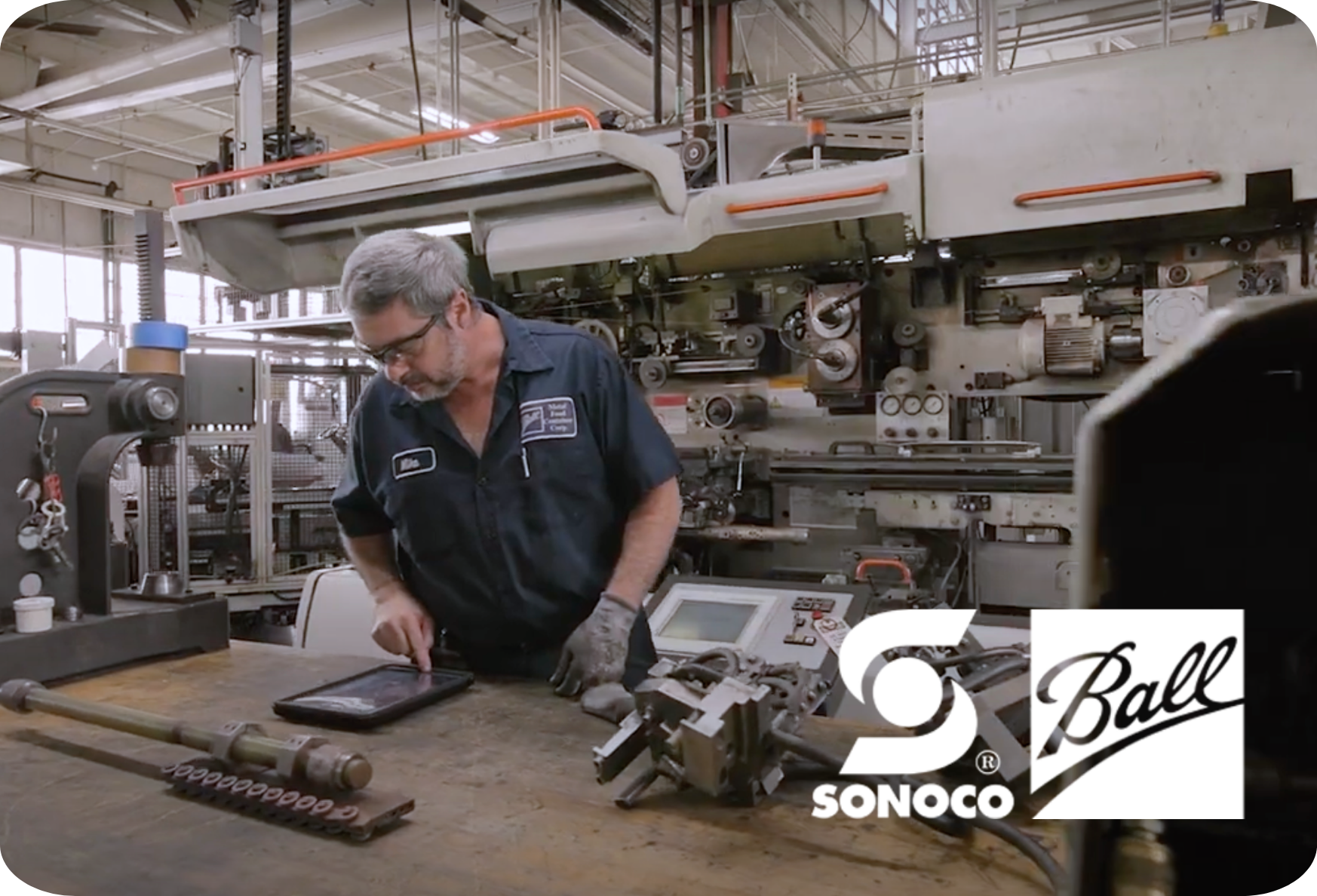
Sonoco x L2L achievements
Fast time to value
"Per plant, I would say really to get everyone up and running, once our data is loaded and things like that, we were within two weeks of up and running and actually kind of using all levels of it."
- Jason Bryan, Senior Manager of Plant Operations
Proactive maintenance with real-time insights
Sonoco implemented L2L’s platform with real-time sensors to monitor equipment health and automatically trigger maintenance before failures occurred.
Before

Sonoco's industrial KBA curing unit fans failed at unpredictable times, causing significant disruptions and often requiring specialized personnel, equipment, and extended line downtime.
Now
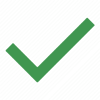

By responding to real-time data, we have avoided costly unplanned catastrophic failures. So far, we're happy with the results.
Production line impact management
Equipment failures of Sonoco’s industrial KBA curing unit fans had cascading impacts on production. By identifying issues earlier, the team was able to eliminate production delays.
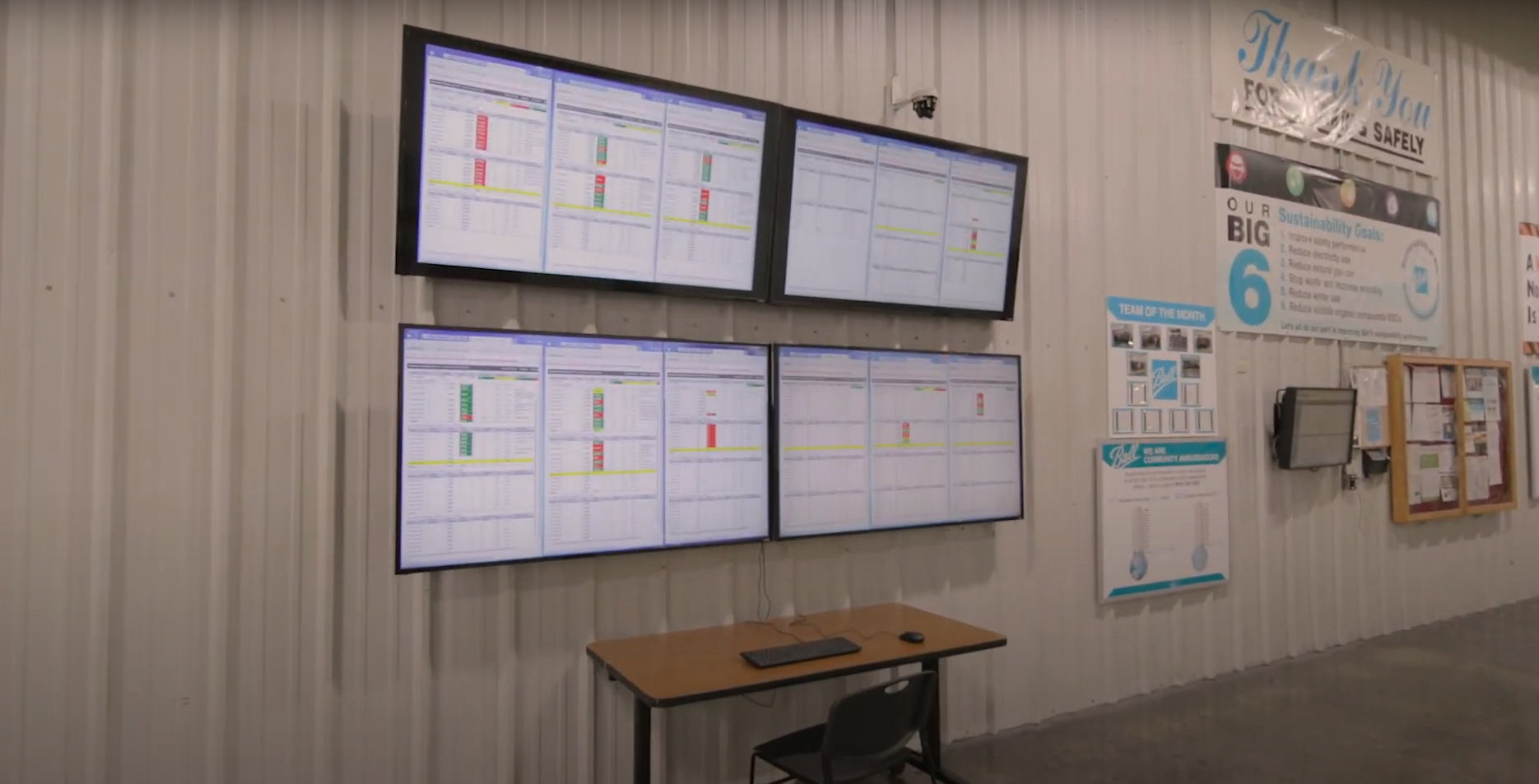
Before

A single fan failure could impact up to 5 production lines inside the plant and 6 to 7 additional lines outside the plant, creating cascading production delays and losses.
Now
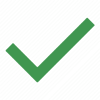
With improved issue detection, maintenance can service fans quickly to avoid failure, improving the reliability of equipment and minimizing the ripple effect of equipment issues.

These ovens support one of the primary processes where we're applying coatings to raw sheets of steel. When one of the fans fails, not only do you lose that coating line, but that line might be supplying 5 lines inside the plant and 6 or 7 lines outside the plant. You might impact 10 or 12 downstream lines as well. That bubble just pushes out, and it's enormous when you're a supply plant like us.
Maintenance resource optimization
Sonoco used L2L in conjunction with real-time sensors to monitor equipment health and automatically trigger maintenance before failures occurred.
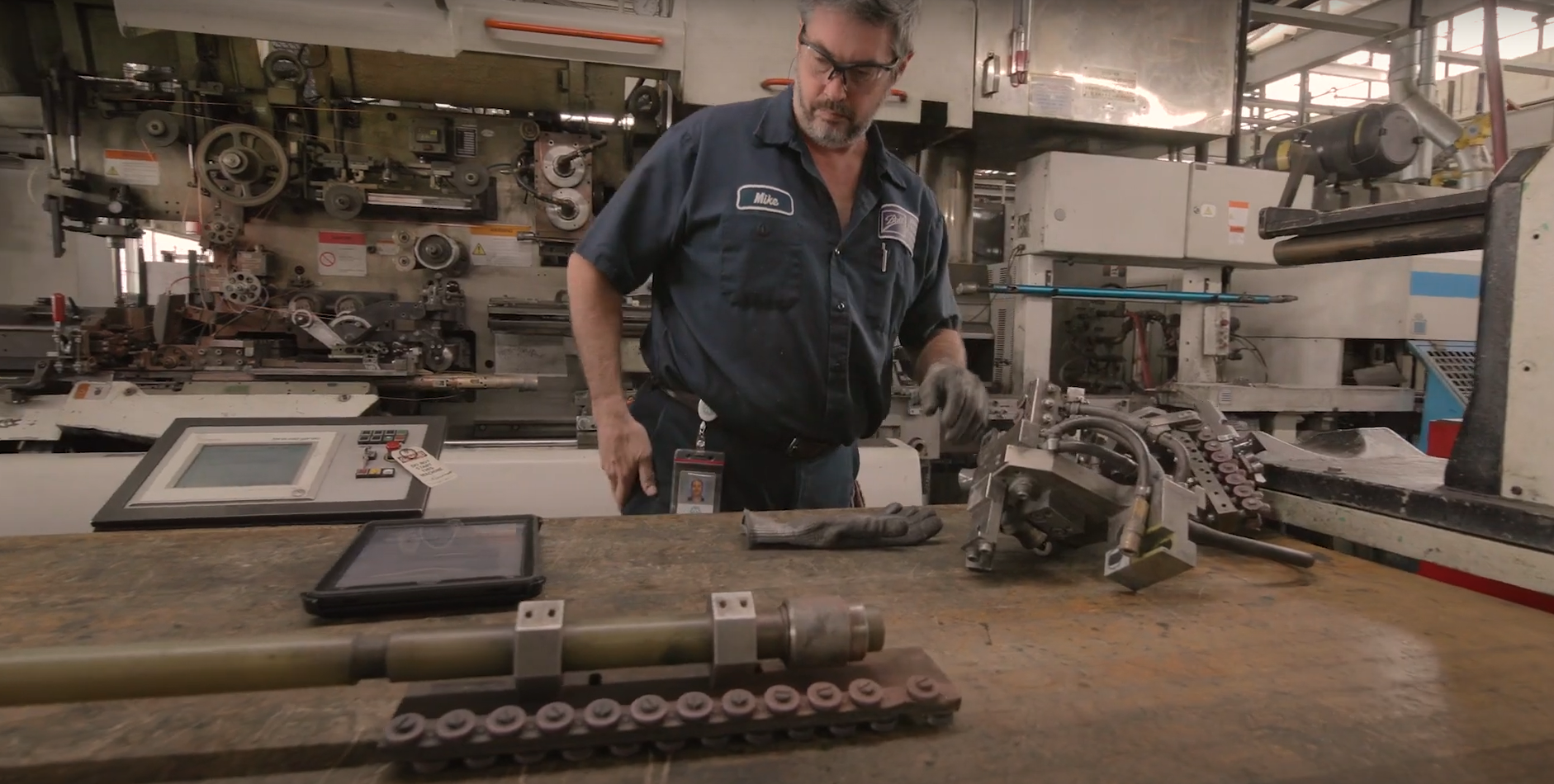
Before

Expensive quarterly scans of the fans with specialized vibration equipment were not able to predict failure and did not reduce the fan failure rate, leaving maintenance teams stuck in a reactive model.
Now
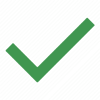
Now, fans can be serviced when needed, and maintenance activities are planned and scheduled during appropriate windows, eliminating emergency overtime and allowing for optimal resource allocation. Overall, Sonoco has seen a reduction in fan replacement costs and has been able to avoid expensive line disruptions.
Daily operations management
Sonoco increased transparency on the shop floor with L2L to engage employees and streamline daily operations management.
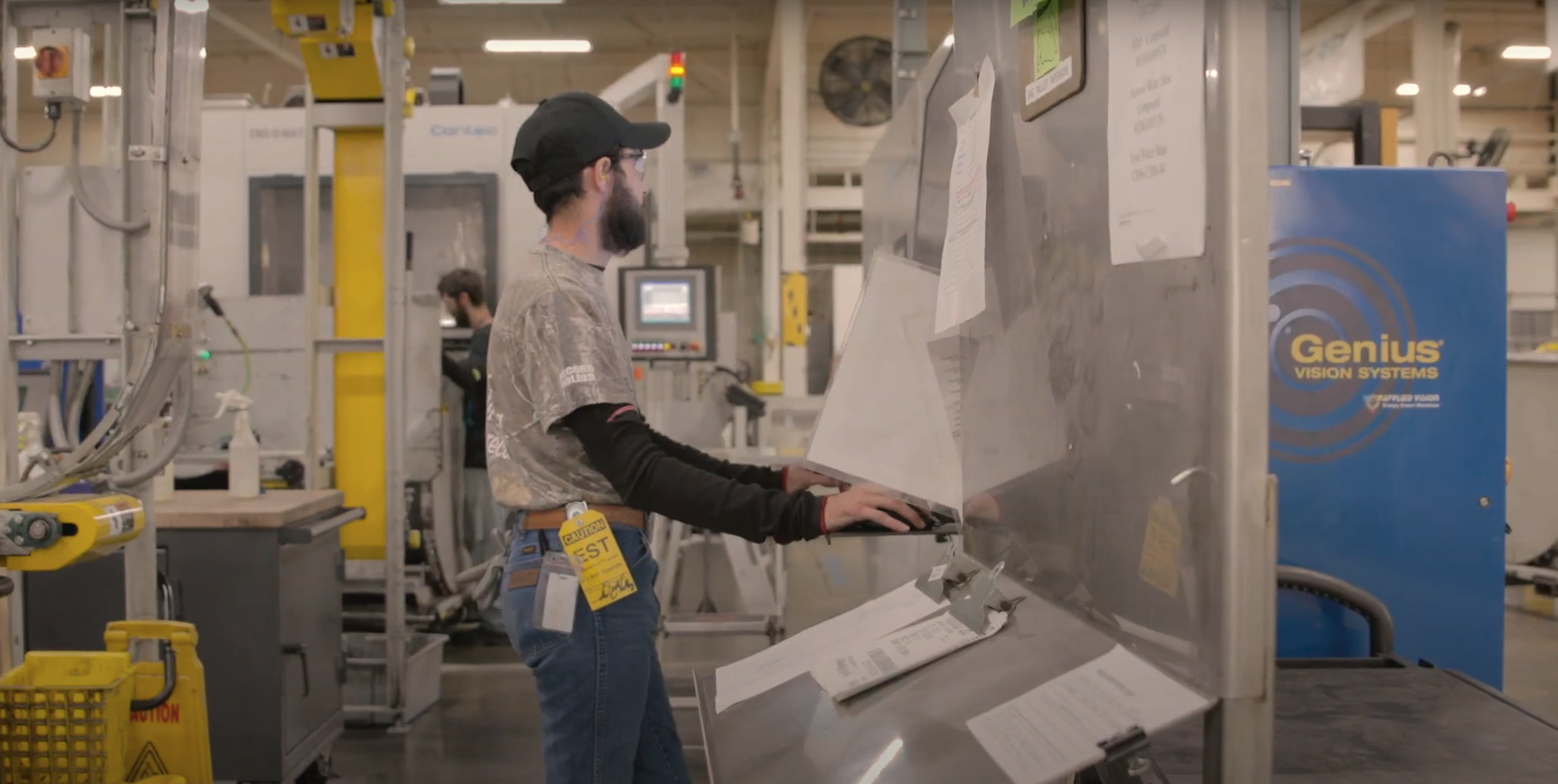
Before

Identifying daily priorities was challenging and often reactive, and paper-based manual processes meant information was lost and communication was spotty.
Now
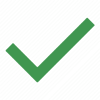
Operators can easily submit Dispatches when issues arise, and maintenance technicians can quickly solve issues, all while having the necessary information to quickly resolve downtime events.

L2L probably saves 10-15 minutes an hour, maybe, with just not having to go through and do all your checks over and over again.
Data management
Data on historical and current processes allows employees to quickly identify trends and areas of improvement and see the impact of changes made.
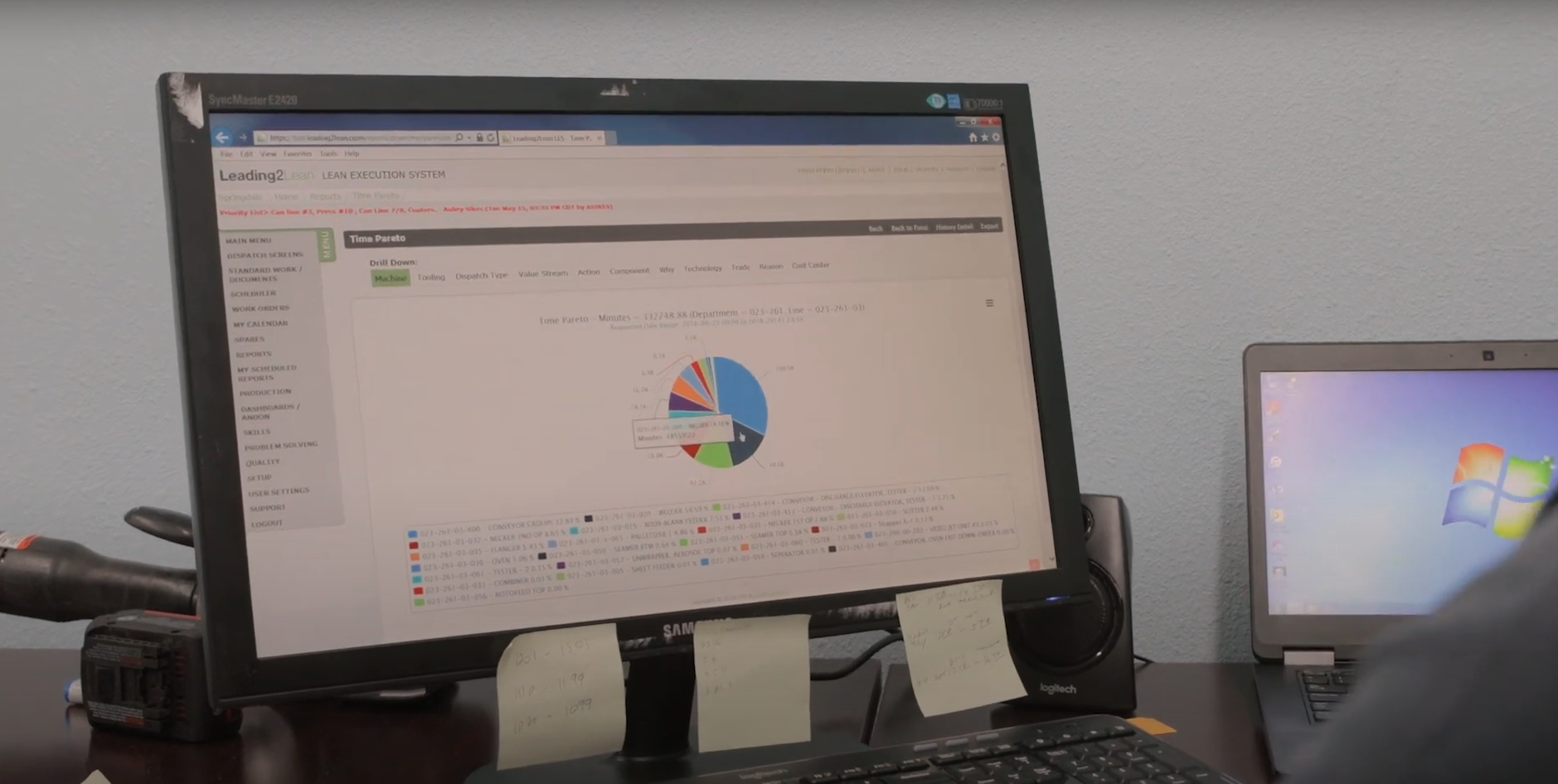
Before

Shift managers had limited visibility into previous shift performance without manual communication.
Now
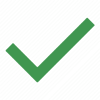
By starting their day in L2L, supervisors can see what recently occurred, better identify issues, and better prioritize areas of improvement.

I start my day by looking at L2L, and I can look at the whole day, what happened on night shift, what happened on the mid shifts as far as how much time has been lost on any particular item.
The return on investment
Big 6 Variance costs ↓
55% decrease in Big 6 Variance costs over one year, driven by 85% improvement in labor costs and 83% improvement in supply costs
Maintenance Costs ↓
$50,000 in cost savings from just two lines using condition-based maintenance and L2L
Annual Savings ↑
The solution that shows your manufacturing problems—and fixes them too
Drive continuous improvement in availability, performance, quality, and workforce enablement.
Quickly identify problems and take action faster with L2L. Empower your teams to achieve daily wins and drive success every day.
Trusted by leading sites around the globe.