Signode streamlines maintenance and production operations
Signode makes a broad spectrum of transit packaging consumables, tools, software, and equipment.
With L2L, the Signode team has:
-> Eliminated paper processes
-> Centralized maintenance and production data
-> Boosted employee engagement and accountability
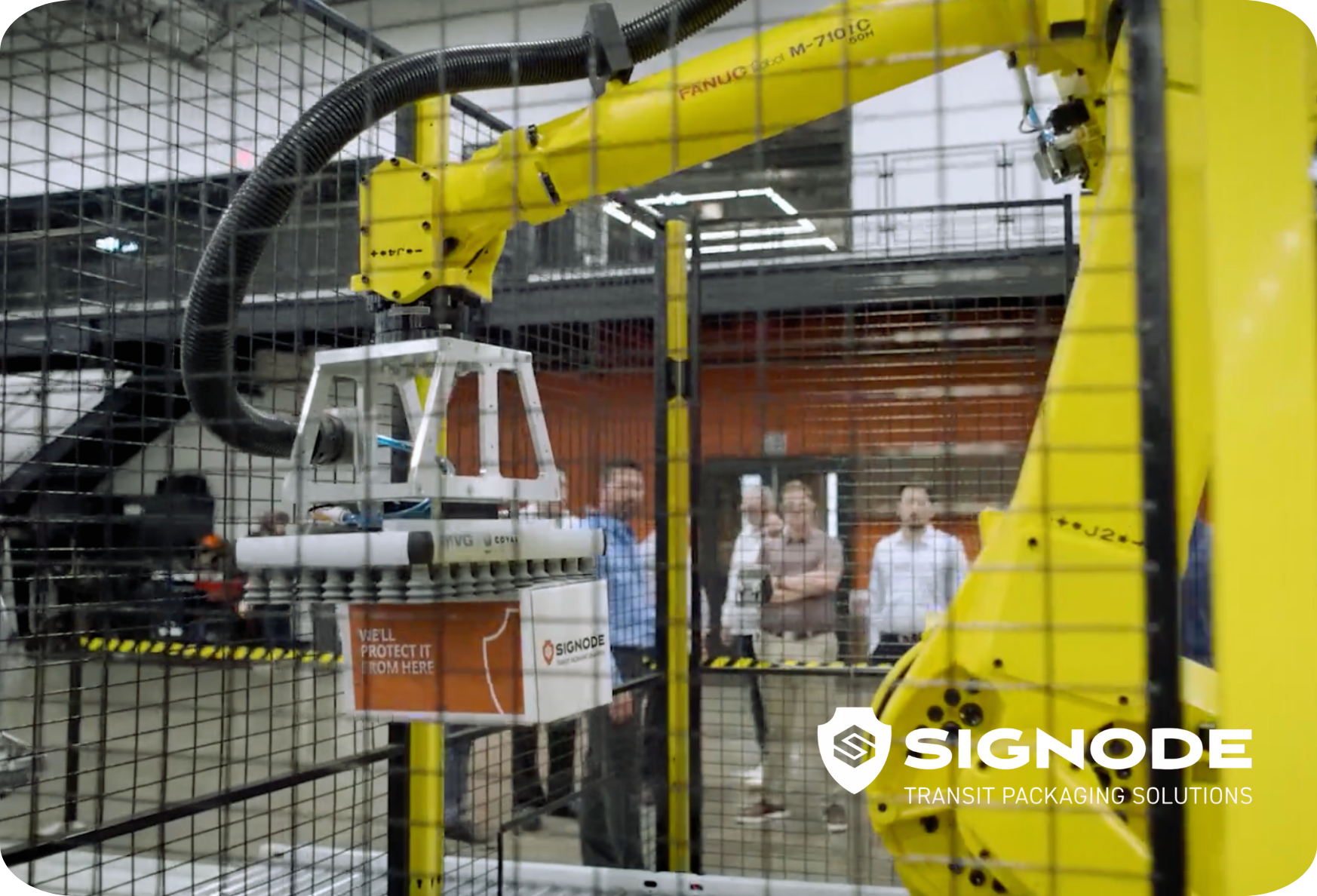
Improved communication & visibility
Old, legacy paper processes meant notes and reminders were lost and overlooked. However, L2L provided Signode with an easy-to-use platform for real-time updates, changeovers, and standardized processes.
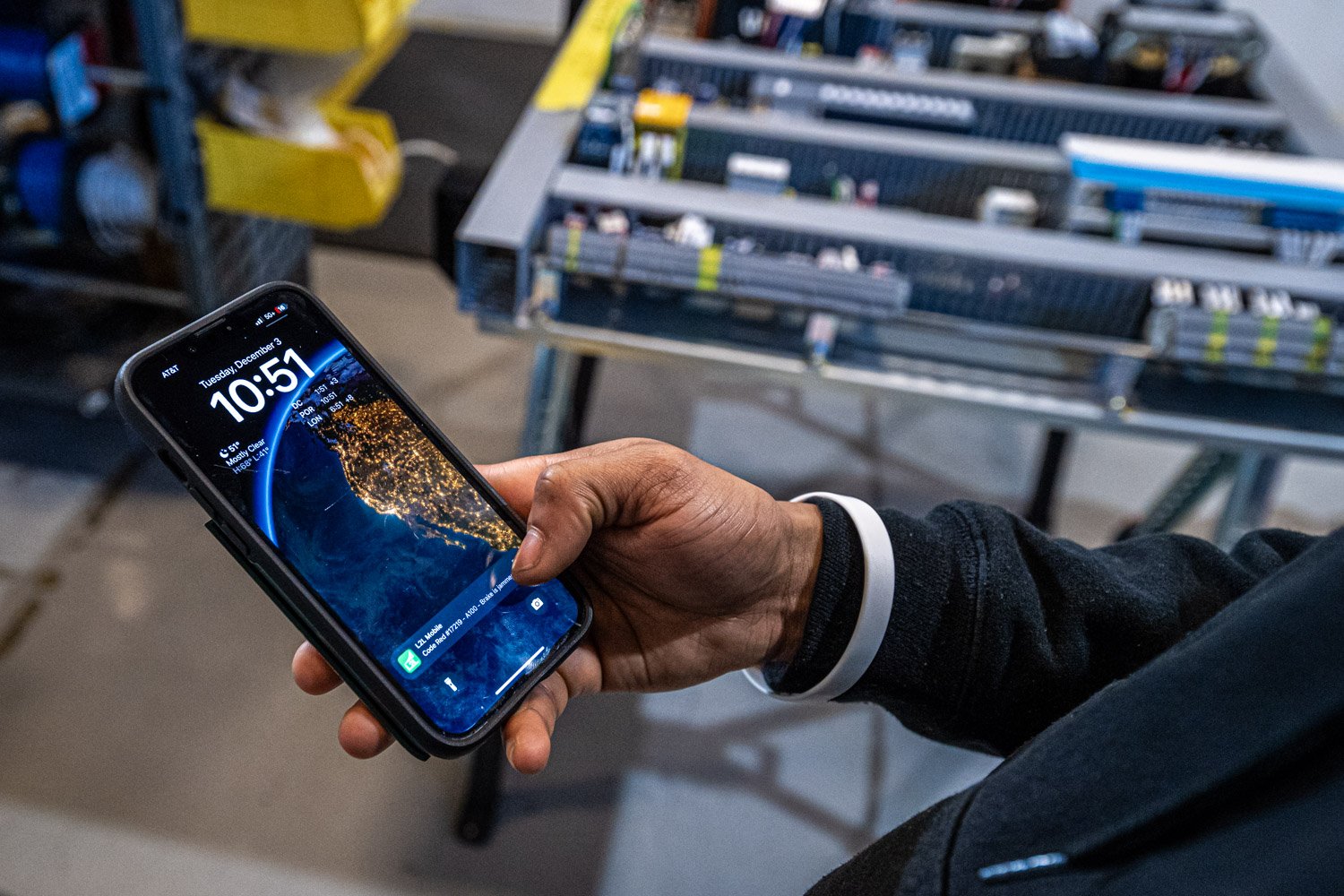
Before

Signode’s existing maintenance system was cumbersome and difficult to use and relied on paper processes. This resulted in many communication gaps and delays.
Now
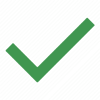
L2L provided real-time visibility into production data and maintenance schedules, bridging communication gaps in a bilingual facility to increase downtime response time.

I connect with the employees, with their problems. Because at the end of the day, they're why I'm here. I want to make their jobs easier.
One-stop shop
L2L became the centralized tool connecting all maintenance, production, and spare part data, leading to decreased costs and improved visibility across the organization.
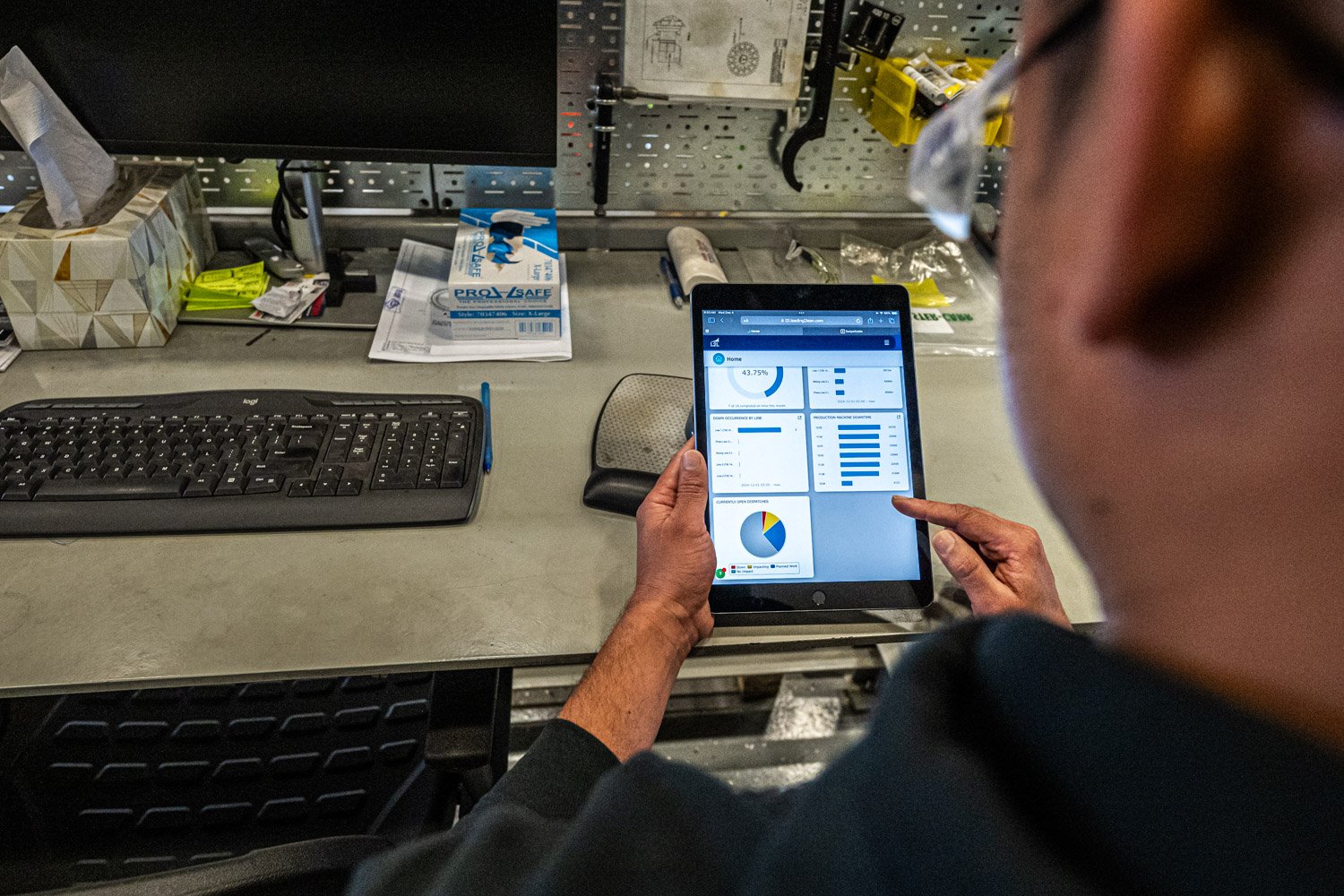
Before

Signode's disconnected systems made it difficult to get an accurate picture of spare part inventory, maintenance schedules, and production data.
Now
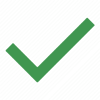
L2Lʼs platform integrated maintenance, production, spare parts, and Dispatch
functionalities in a single solution for plant and corporate employees, saving time and money.

L2L is a one-stop shop. It reports your production, safety, maintenance, and quality. Everything we need from a day-to-day plant perspective as far as data and information, it's available in L2L.
Improved accountability and productivity
Signode’s employees felt empowered and engaged as L2L’s easy-to-use system increased shop floor transparency and accountability. L2L was quickly adopted by employees, driving a more transparent and communicative work environment.
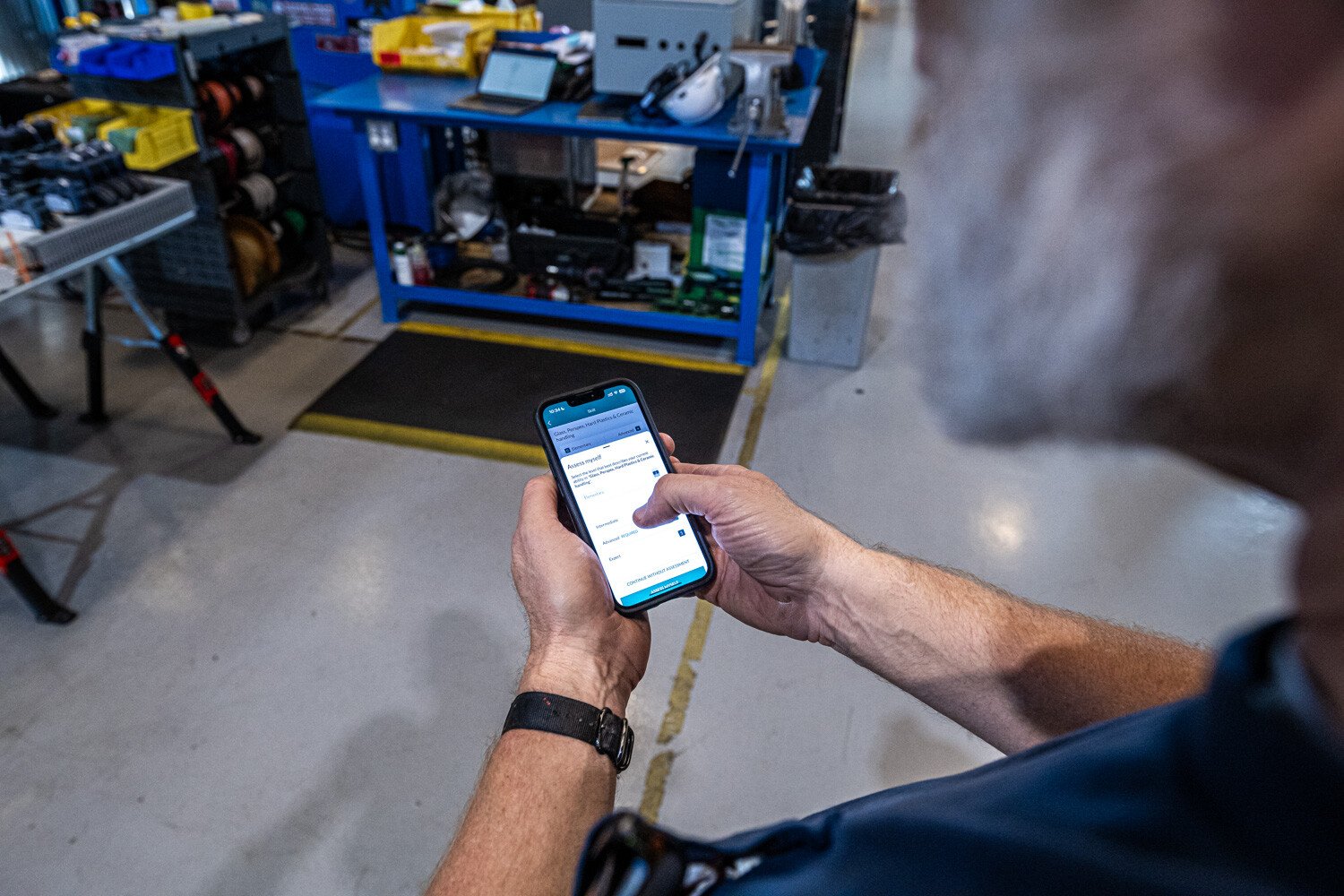
Before

Manual processes and disconnected systems created inefficiencies, delays in addressing shop floor issues, and low employee ownership over their areas.
Now
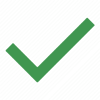
Accountability has increased as operators can see production data on their devices, fostering ownership. Also, employees can quickly identify root causes, creating a more transparent work environment.
The return on investment
Response time ↑
Faster response to downtime and production floor issues
Data visibility ↑
Enhanced data visibility across all plant operations
Engagement ↑
Positive cultural change with increased employee engagement
Accountability ↑
Lead time ↓
Reduced lead time for obtaining spare parts
Spending ↓
The solution that shows your manufacturing problems—and fixes them too
Drive continuous improvement in availability, performance, quality, and workforce enablement.
Quickly identify problems and take action faster with L2L. Empower your teams to achieve daily wins and drive success every day.
Trusted by leading sites around the globe.