Oetiker improves OEE
+11% in 6 months
Oetiker is a global leader in high-end connecting solutions for the vehicle industry and for high-value applications in industrial segments.
With L2L, the Oetiker team has improved:
-> Standardized data drove global efficiency gains
-> Real-time visibility enabled continuous improvement
-> Streamlined collaboration ensured consistent quality

Oetiker x L2L achievements
Fast time to value
With L2L's digital manufacturing solutions, Oetiker achieved significant improvements across multiple facilities, including an 11% increase in Overall Equipment Effectiveness (OEE) in just six months at its Alliston, Ontario plant. The success led to company-wide implementation across all 10 manufacturing facilities.
.png)
Production data standardization
Facing inconsistencies across its global manufacturing plants, Oetiker implemented L2L to standardize operations and drive continuous improvement. This enabled real-time data analysis, global process alignment, and significant productivity gains, as evidenced by increased Parts Produced per Man Hour (PPMH) and reduced downtime.
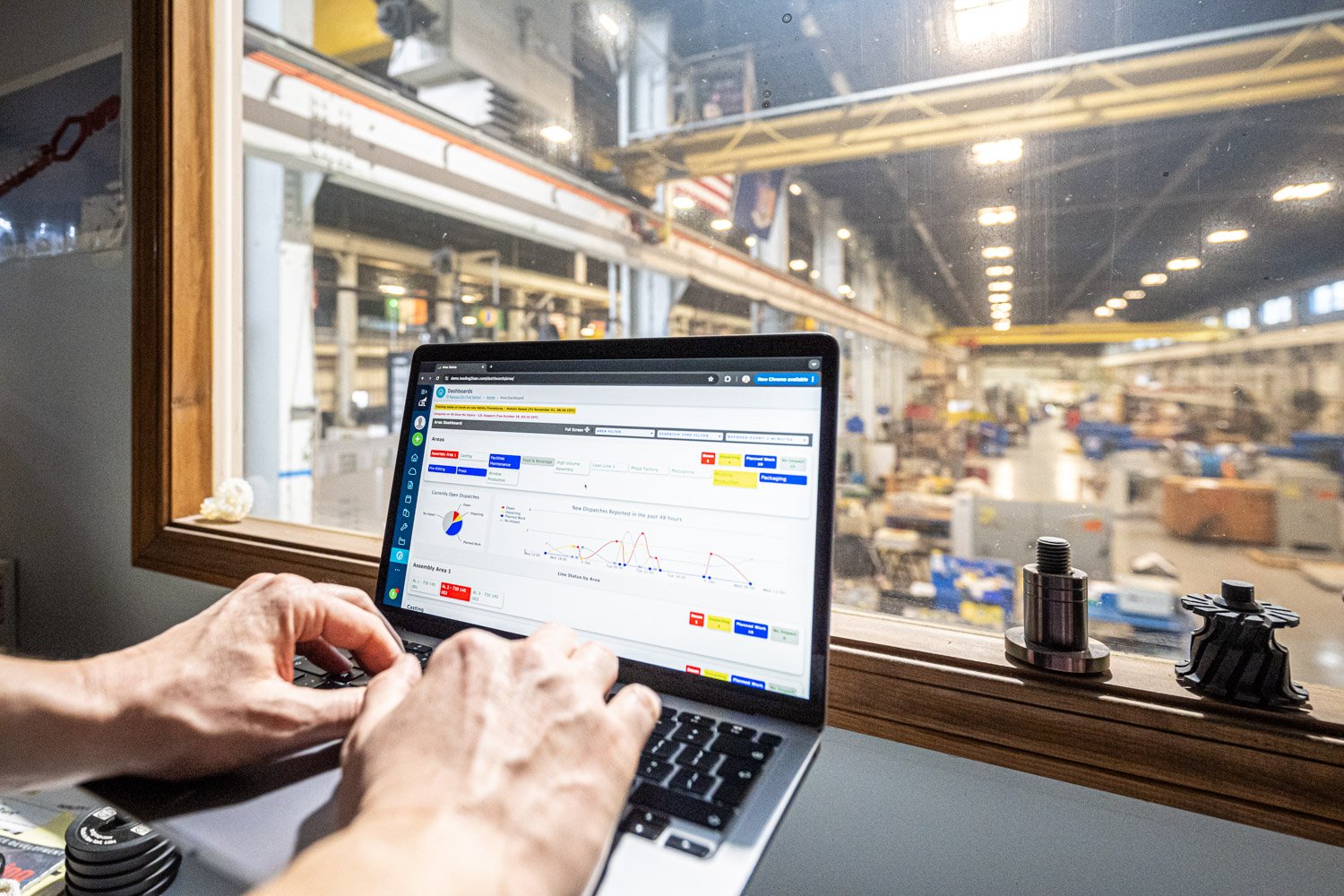
Before

While Oetiker's plants were collectively producing over 2 billion connecting solutions annually, there were inconsistencies between plants. Even though many plants had the same level of assets and personnel, there was a variance in actual production.
Now
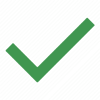
Using L2L's Production module, Oetiker started analyzing production data on a worldwide scale. The company was able to identify systemic problems and develop solutions and standards that could be implemented across the globe.

L2L makes production run more effectively. It's not just focused on individual aspects, departments, or roles. L2L focuses on the value stream as a whole. It really got the lean concepts nailed down.
Production visibility and OEE improvement
Oetiker lacked real-time visibility across its global plants. Following significant performance improvements at its Ontario plant, Oetiker expanded L2L to all ten facilities, establishing a corporate platform for continuous improvement and industrial transformation.
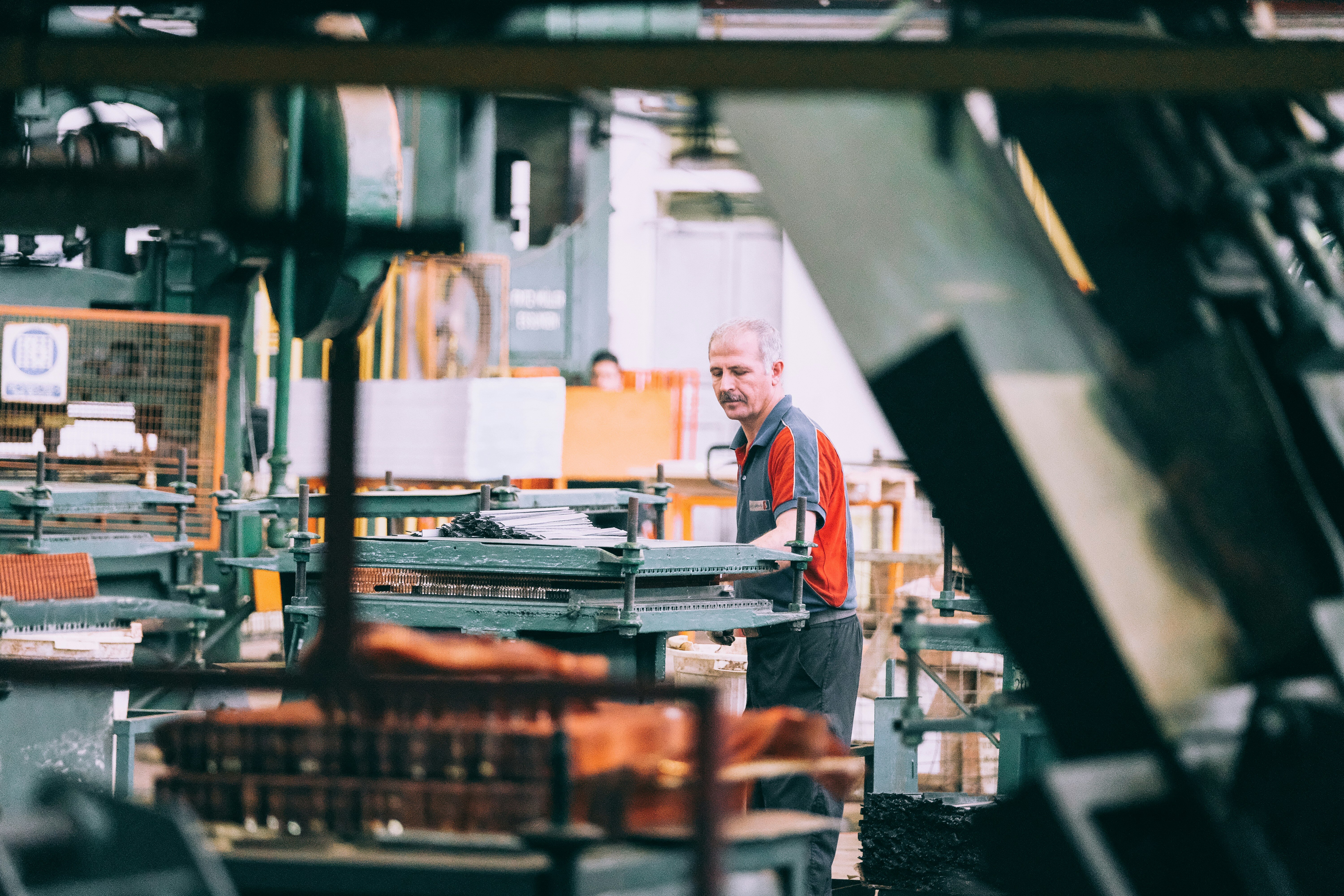
Before

There was a lack of real-time visibility into production practices at all 10 Oetiker plants around the world. This created challenges in understanding actual performance and identifying areas for improvement.
Now
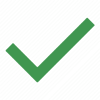
Oetiker's successful L2L pilot in Ontario, marked by significant OEE and productivity gains, led to its global deployment across all ten plants. This now provides Oetiker with a standardized platform for continuous improvement and smart manufacturing.

Prior to L2L, everybody had their own isolated packets of information. Now with L2L, we have a single point of truth that all of us can use to problem solve.
Quality management and standardization
To maintain its rigorous parts-per-billion quality standard globally, Oetiker needed consistent processes. L2L enabled this through standardized collaboration, ensuring uniform quality across all plants.
.png)
Before

In manufacturing, product quality is always a top priority, Oetiker’s goal of parts per billion requires uniform, high product quality for every plant.
Now
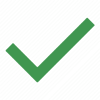
Shift changes and tier meetings are essential for aligning the entire team on production issues. L2L TeamBoard helps standardize these processes while enabling continuous improvement across all facilities.

These meetings ensure that small issues can be addressed before becoming larger problems. Team members can discuss core safety, quality, delivery and cost (SQDC) issues.
Meeting efficiency with TeamBoard
Oetiker's team meetings were previously hampered by inefficient data searches, disrupting discussions and wasting time. The adoption of L2L TeamBoard streamlined meetings by providing instant data access, enhancing team engagement, and also aiding in employee recruitment by appealing to digitally-native workers.
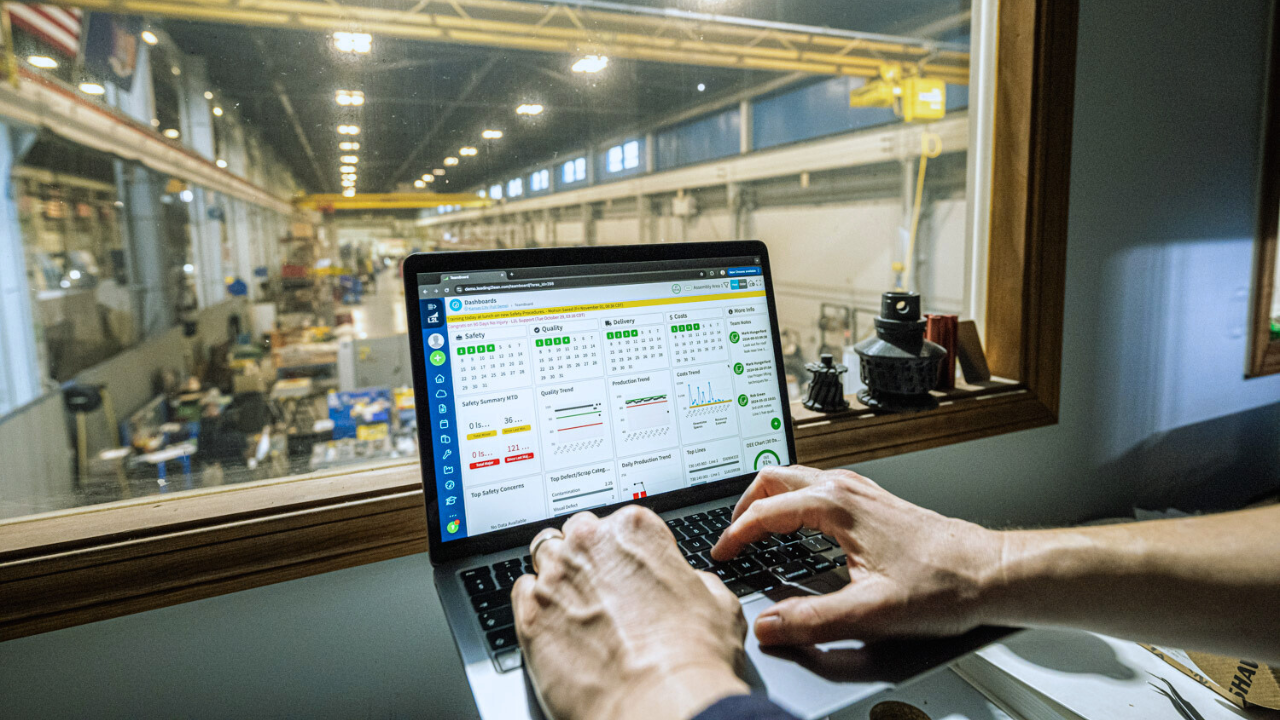
Before

Team meetings were inefficient and disjointed due to constant data searches, diverting attention from critical discussions.
Now
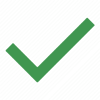
Oetiker implemented L2L TeamBoard to streamline meetings by eliminating data searches, enhancing team engagement, and accommodating digital-native employees with real-time data displays.

Before TeamBoard, finding the right data was distracting for the team. With TeamBoard, the team can stay engaged. The presenter can focus on the team, and everyone can focus less on the data and more on the issues.
The return on investment
OEE ↑
11% increase in Overall Equipment Effectiveness (OEE) in just six months at the Alliston plant
Machine Availability ↑
5% improvement in machine availability allowing for more productive time
Performance ↑
PPMH ↑
MTTR ↓
The solution that shows your manufacturing problems—and fixes them too
Drive continuous improvement in availability, performance, quality, and workforce enablement.
Quickly identify problems and take action faster with L2L. Empower your teams to achieve daily wins and drive success every day.
Trusted by leading sites around the globe.