Mueller shifts to proactive maintenance with L2L
Mueller Industries is a global manufacturer of copper and copper alloy products.
With L2L, the Mueller team has:
-> Shifted to proactive, data-driven maintenance
-> Simplified the spare parts request process significantly
-> Improved plant-wide maintenance communication and visibility
Reactive to proactive maintenance
Mueller shifted into preventive maintenance by implementing L2L, which let the plant digitize processes, centralize data, and gain visibility into machine performance for better product quality.
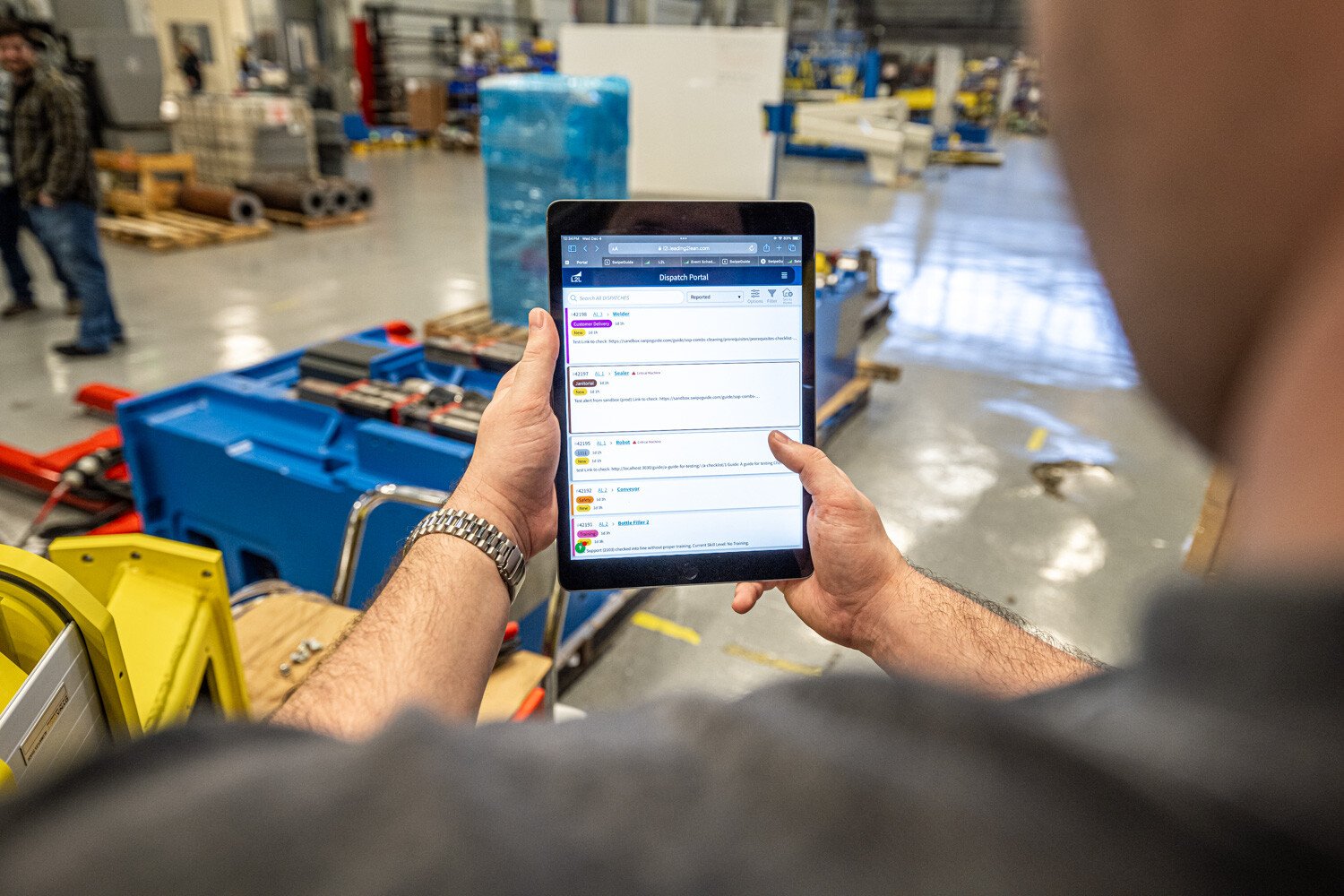
Before

Mueller's reactive maintenance process was an ongoing issue at the company's Great Lakes Copper plant. Maintenance teams were laden with static preventive maintenance (PM) scheduled and manual methods of data management. They also lacked visibility into machine performance.
Now
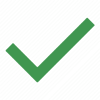
With L2L, Mueller created standardized work procedures and preventive maintenance processes while centralizing and digitizing work order data in L2L. Now, Maintenance can track planned jobs and progress target work orders in a single system. Maintenance supervisors have an easier time tracking operational efficiency—something they didn't have the tools to do before launching L2L.

We had a static PM schedule and reactive breakdowns. We were using either Microsoft Excel, Access, or human memory to manage maintenance.
Streamlining and simplifying workflows
Inefficient, paper-based spare parts process led to delays and frustration. L2L streamlined the requisition process, reducing it to a single step and enabling mobile access for technicians across the plant.
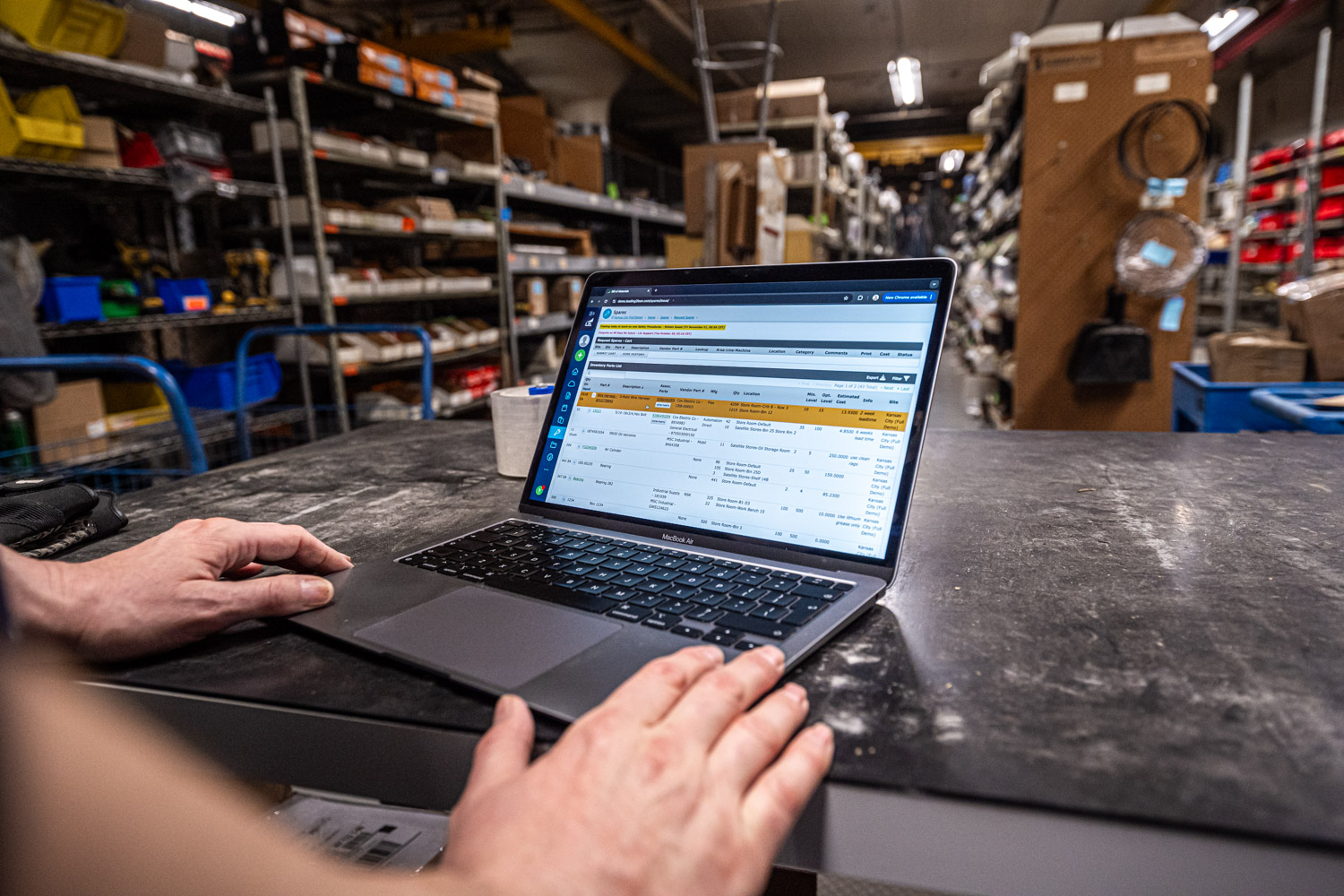
Before

A cumbersome, paper-based spare parts process involving manual MROs, ERP entry, and physical searches caused delays and inventory shortages, frustrating maintenance technicians.
Now
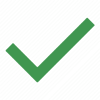
Mueller simplified the parts requisition process from five steps to one with L2L Studio. Technicians now request spares from anywhere in the plant using phones, tablets, or computers.
Improved communication and visibility
Before L2L, Mueller’s Great Lakes Copper plant suffered from siloed information and communication, leading to delays and inefficiencies in maintenance and production. L2L's centralized platform improved communication across the plant.
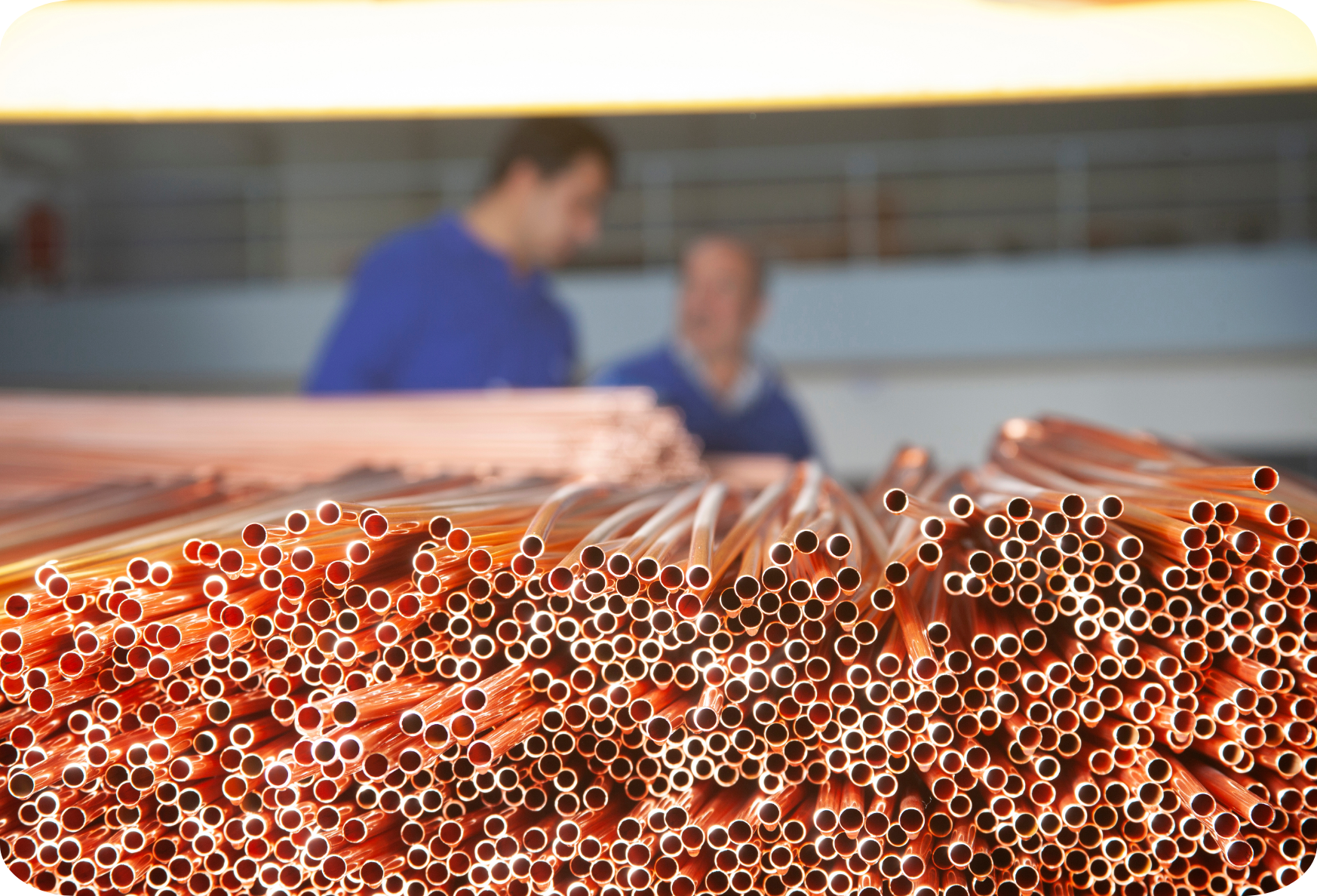
Before

Disconnected information sharing across departments led to delays and miscommunications due to siloed work and scattered data. The lack of a centralized system hindered collaboration, particularly during critical maintenance and production needs.
Now
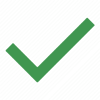
L2L's real-time digital list provides plant-wide visibility of maintenance activities, improving coordination and response times. Centralizing communication reduces confusion and supports interdepartmental collaboration.
Metrics tracking and performance analysis
Mueller previously lacked operational efficiency tracking and machine visibility, leading to reactive maintenance and poor decision-making. L2L Studio now provides real-time, data-driven insights for proactive maintenance and performance improvements.
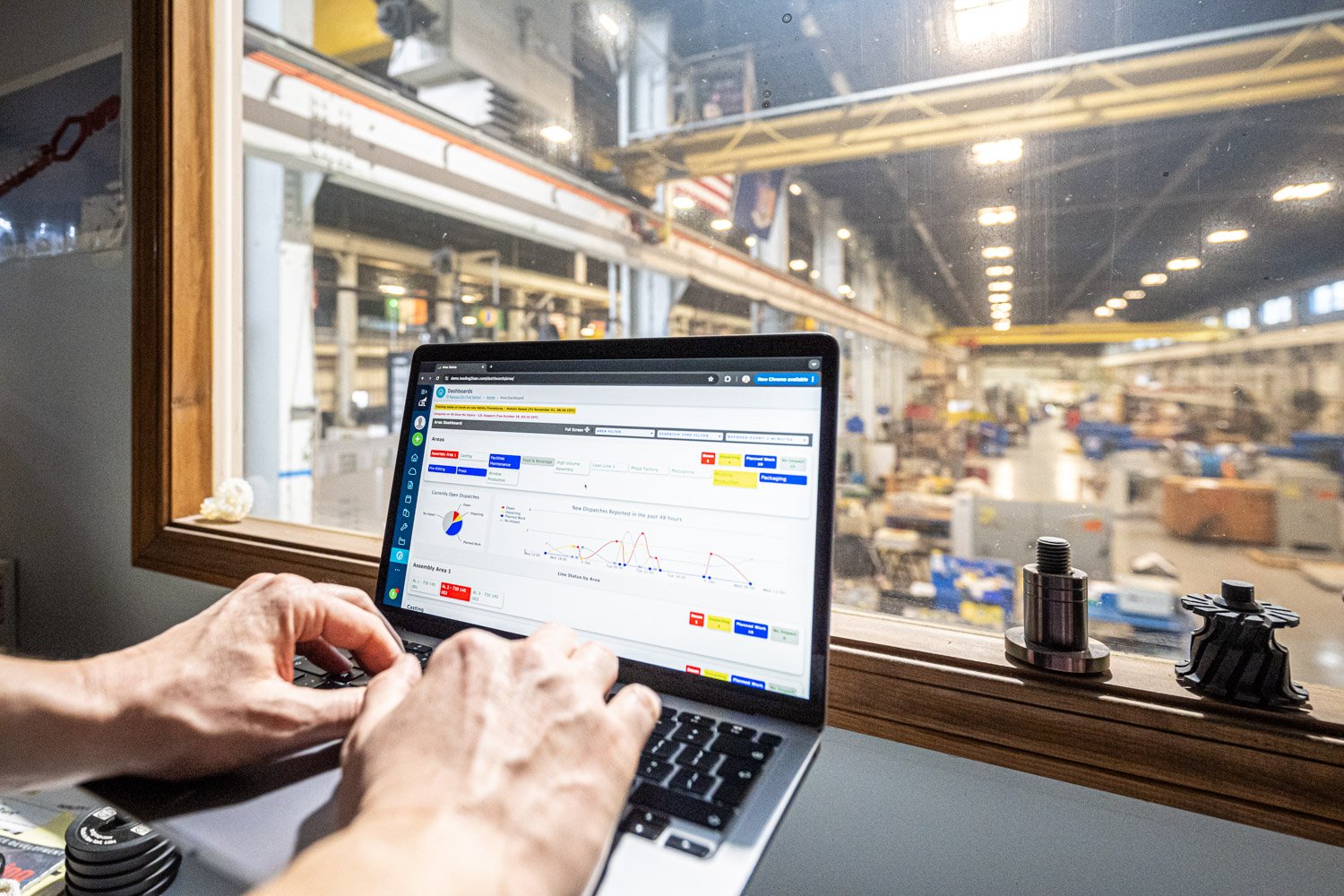
Before

Mueller's lack of operational efficiency tracking and machine visibility led to frequent breakdowns and reactive maintenance. Without data-driven insights, management couldn't optimize maintenance or measure its impact on plant performance.
Now
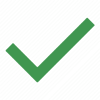
L2L Studio provides Mueller with real-time performance metrics, enabling data-driven maintenance and proactive problem-solving, replacing reactive repairs with informed decisions.
The return on investment
Streamlined process
Process efficiency improvement for spare parts management
Repair Time ↓
Reduction in repair time metrics
Cost savings ↑
Tangible cost savings from reduced downtime
High adoption
The solution that shows your manufacturing problems—and fixes them too
Drive continuous improvement in availability, performance, quality, and workforce enablement.
Quickly identify problems and take action faster with L2L. Empower your teams to achieve daily wins and drive success every day.
Trusted by leading sites around the globe.