How JELD-WEN improved productivity by 53%
JELD-WEN is a leading designer, manufacturer, and distributor of high-performance interior and exterior doors, windows, and building products.
With L2L, the JELD-WEN team has improved:
-> Productivity gains through digital transformation
-> Centralized operations management
-> Real-time visibility for data-driven decisions
JELD-WEN x L2L achievements
Propelling operations
"L2L helped us expedite the transformation. With employee teamwork, improved processes, and L2L providing the data we needed, we’ve accomplished a tremendous amount in just a short period of time."
- Keith Holliman, Maintenance and Reliability Manager
Going paperless
JELD-WEN reduced its paper trail and saved time by digitizing reporting processes.
Before

JELD-WEN was using manual processes, like Excel and print-out papers, to manage work.
Now
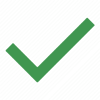

We were underperforming, understaffed, and it was spreadsheet on top of spreadsheet. Simply keeping track of what was happening was a nightmare, and the team was spending hours gathering data. We knew we had to change.
Beyond just maintenance
JELD-WEN needed a comprehensive system to handle more than just work orders and maintenance.
Before

JELD-WEN leaders realized they needed capabilities beyond that of a CMMS.
Now
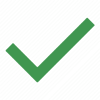
JELD-WEN uses L2L to manage comprehensive maintenance, training, onboarding, checklists, and reporting, making teams more productive and improving safety on the floor.
Real-time visibility and data
JELD-WEN was spending too much time on manual processes and needed a way of working that freed teams to focus on more strategic initiatives.
Before

JELD-WEN relied on paperwork to identify critical insights, which was tedious and time-consuming for employees.
Now
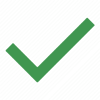
JELD-WEN now has real-time insights into what is happening on the production floor accessible via mobile devices.

It’s a big thing to be digital. It gives me real-time data, I can see what they’re running on the shift currently and I can see what they ran in the last hour without having to dig through mounds of paperwork to find that information.
The return on investment
Performance ↑
53% overall performance improvement
Less Paperwork ↓
90% reduction in administrative paperwork
Increased Output ↑
Time Saved ↑
The solution that shows your manufacturing problems—and fixes them too
Drive continuous improvement in availability, performance, quality, and workforce enablement.
Quickly identify problems and take action faster with L2L. Empower your teams to achieve daily wins and drive success every day.
Trusted by leading sites around the globe.