Hitachi Astemo is achieving operational excellence
The Rock Spring Astemo facility manufactures suspension and brake components for major global automotive original equipment manufacturers (OEMs).
With L2L, the Hitachi team has improved:
-> Eliminate manual paperwork
-> Boost operational visibility & machine reliability
-> Empower frontline workers
Digital innovation
"With L2L, we were instantly able to take them into the future and give them something that will allow them to digitally make a difference very quickly."
- Maurice Henson, Senior Director of IT Operations
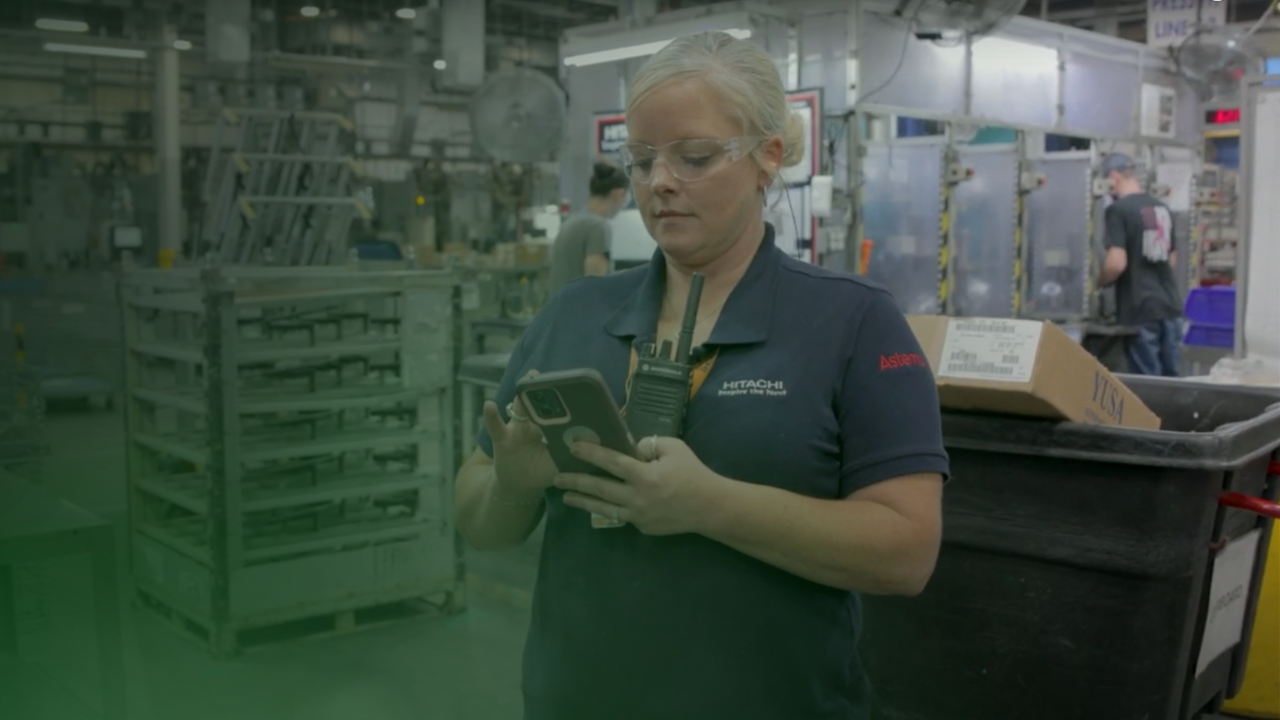
Improved data accessibility
Multiple systems and paper trails made finding the right information nearly impossible. With L2L, Hitachi's Rock Spring plant has saved time by going digital and improving data accessibility.
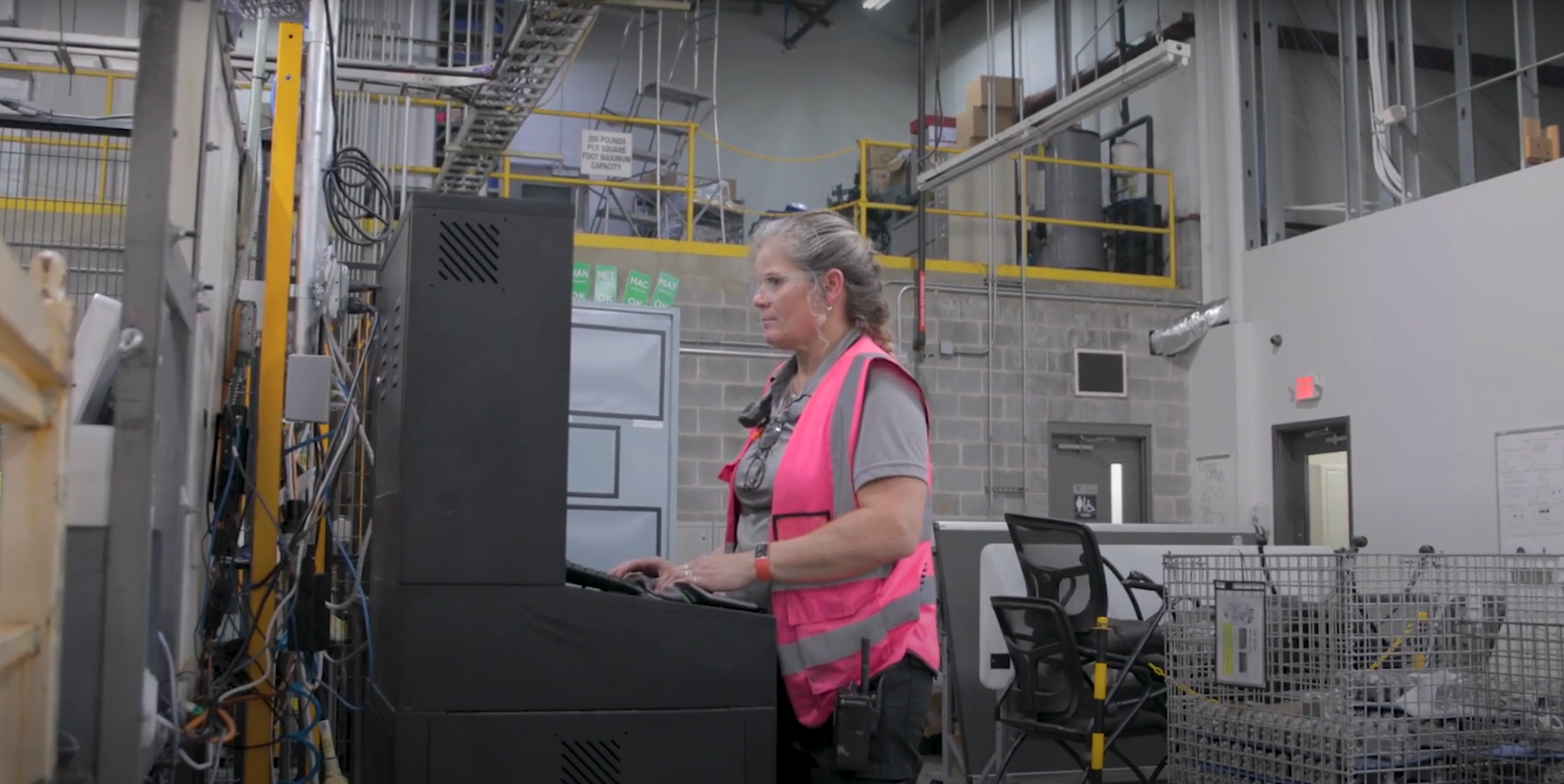
Before

Hitachi was using multiple systems and had a paper trail of work. Data analysis was done manually, and charts and graphs were difficult to analyze.
Now
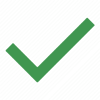

For us, no more writing, no more paper, no more piles of paper. Just go in and type it in and we’re done. We’re walking away - it saves so much time.
Team productivity
Before, processes were unclear. Now, employees can access information on-the-go from tablets or phones, see the information they need, and easily communicate across the shop floor. Employees feel involved and empowered to do their jobs.
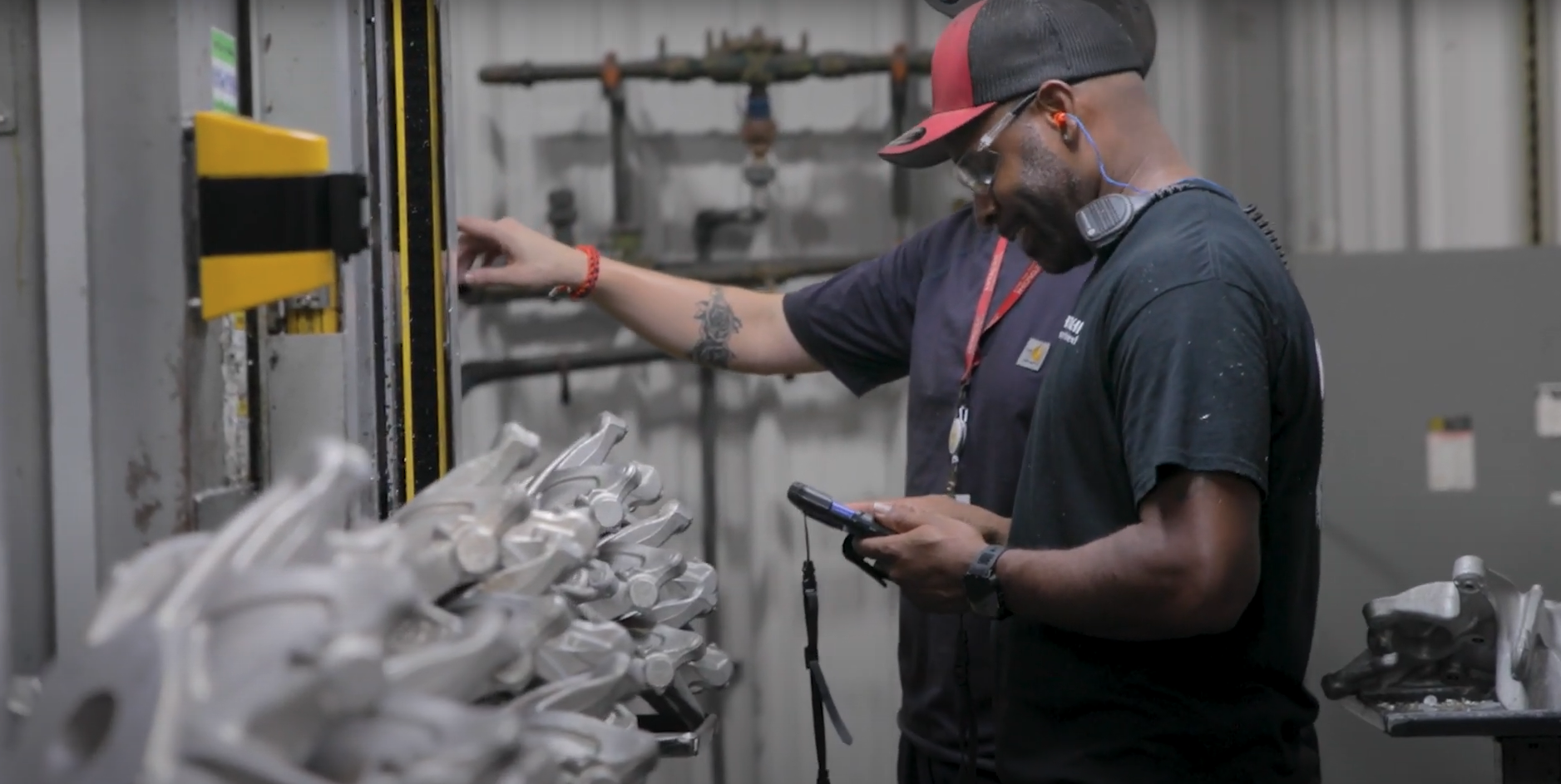
Before

Processes were unclear and lived across multiple systems, slowing frontline employees down.
Now
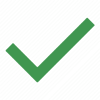
Utilizing tablets on the floor equipped with L2L has streamlined communication and made everyone’s job processes more smooth.

We can instantly pull [L2L] up from a tablet, a phone, from our desktop and we can see where they are exactly at that time. That has been a big plus, for sure.
Increased machine reliability
Technicians can see/learn/check what preventive maintenance needs to be done when and where before issues occur, improving machine reliability.
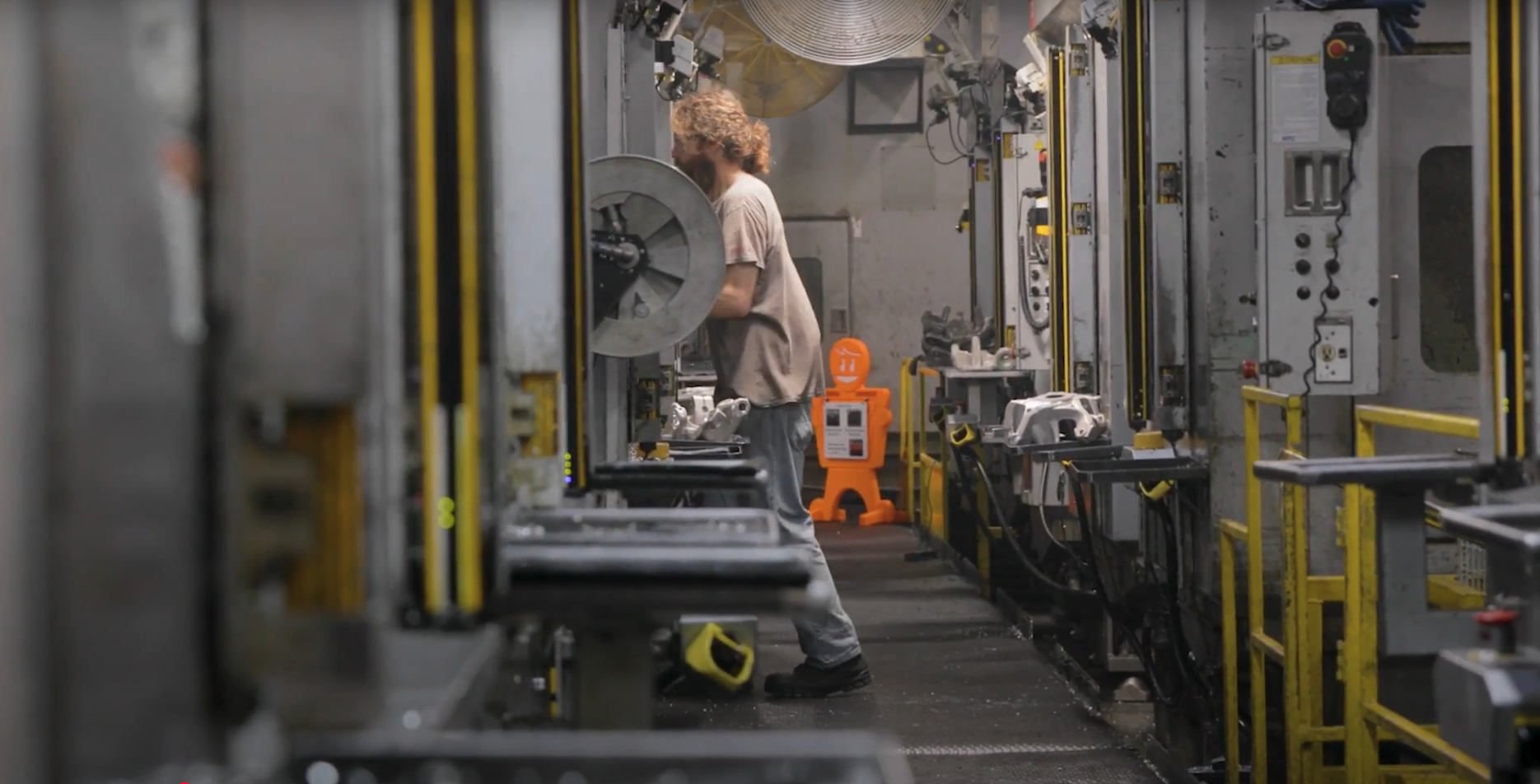
Before

Maintenance was reactive, and technicians resolved issues in real-time as they occurred.
Now
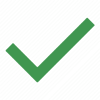
Now, with L2L, technicians have a pulse on what needs to be done and when. This shift into preventive maintenance has increased machine reliability.

L2L gives us this traceability to see the reliability of the machines. We can see what needs done before it happens. It slingshots us into smoother processes all around.
The return on investment
Improved Operations
Most Successful 12 Months in 23 Years
Data visibility ↑
Increased and enhanced data visibility across all plant operations
Empowered workforce
Communication ↑
Reliability ↑
Proactive and predictive maintenance capabilities have led to increased uptime and machine reliability.
Profitability ↑
By streamlining operations, profitability has increased and continuous improvement has progressed
The solution that shows your manufacturing problems—and fixes them too
Drive continuous improvement in availability, performance, quality, and workforce enablement.
Quickly identify problems and take action faster with L2L. Empower your teams to achieve daily wins and drive success every day.
Trusted by leading sites around the globe.