How HEINEKEN reduced training time by 50%
HEINEKEN primarily manufactures a variety of beers, including its flagship pale lager, other international and local beer brands, and non-alcoholic beverages and ciders.
With SwipeGuide powered by L2L, the HEINEKEN team has improved:
-> Onboarding and training experience
-> Global sharing of best practices across 138 breweries
-> First-time-right and reduced rework
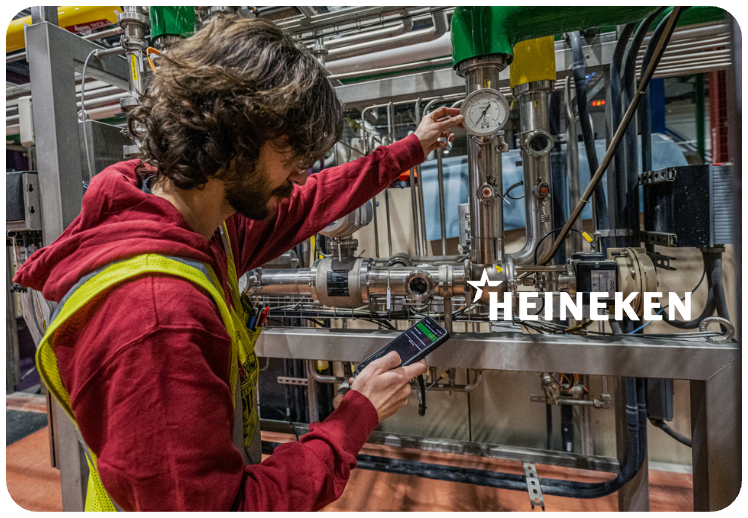
HEINEKEN x L2L achievements
Expert knowledge management
"SwipeGuide [powered by L2L] is a great tool to make knowledge available on the shop floor. The instructions are easy to use and the user-friendly interface supports knowledge creation by the operators themselves."
- TPM Manager, HEINEKEN Singapore
Better work instructions for operators
HEINEKEN's frontline has access to digital standards and job aids that make it simple to access the correct operational knowledge in the moment of need.
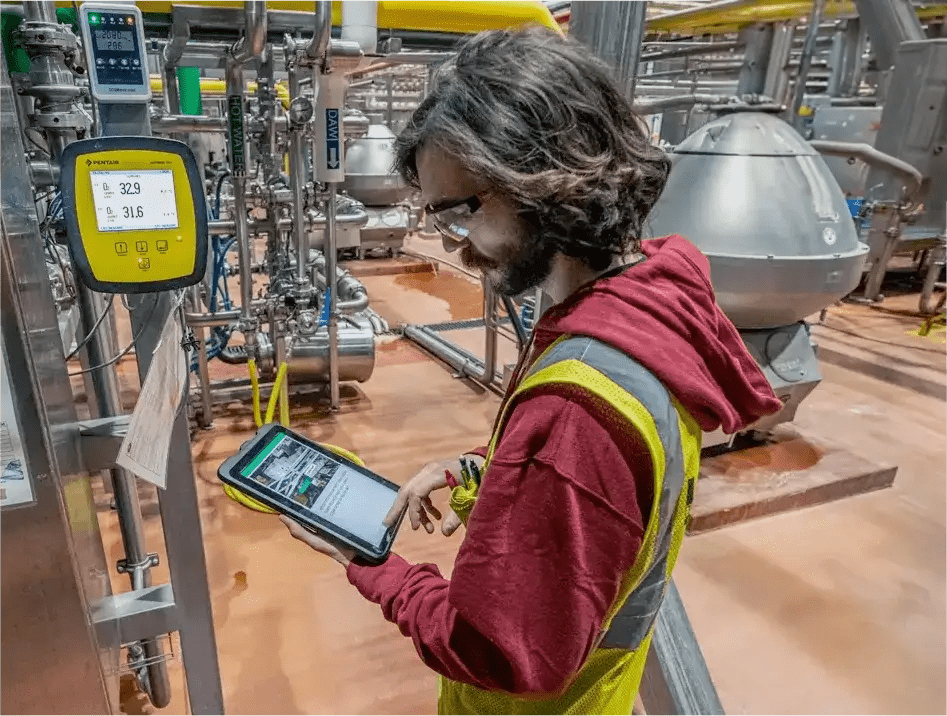
Before

Previously, employees at HEINEKEN relied on manual documentation saved in different areas. Knowledge retention was difficult for employees to manage.
Now
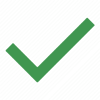

Usually, when you generate a lot of information, you tend to save it in different spots. With SwipeGuide [powered by L2L], it’s the perfect tool to be organized and find the information you need fast and accurately.
Standard work for supervisors
HEINEKEN uses SwipeGuide powered by L2L to standardize and improve processes throughout their global network of breweries.
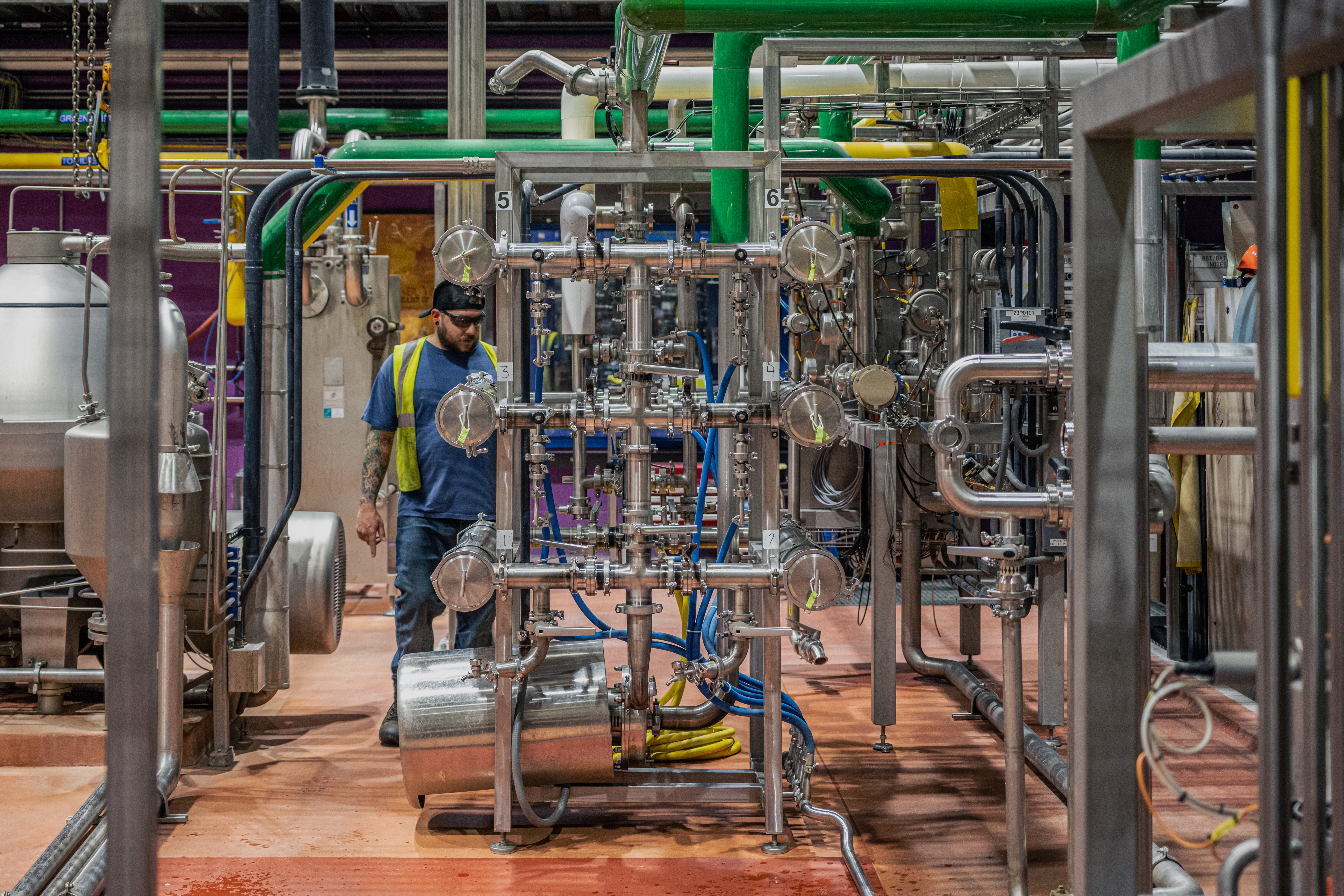
Before

Before HEINEKEN's Connected Brewery Program, procedures were followed inconsistently across different shifts and locations.
Now
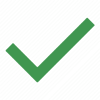
The digital standard work is implemented across 130+ breweries worldwide as part of HEINEKEN’s “Connected Brewery” program.

We can tap into the network of our mother company - there are already hundreds of breweries that use SwipeGuide [powered by L2L], so we can copy and paste their knowledge into our brewery.
Faster onboarding for new employees
With SwipeGuide powered by L2L, HEINEKEN can get new employees up to speed faster by making sure they can access the information they need quickly from the shop floor.
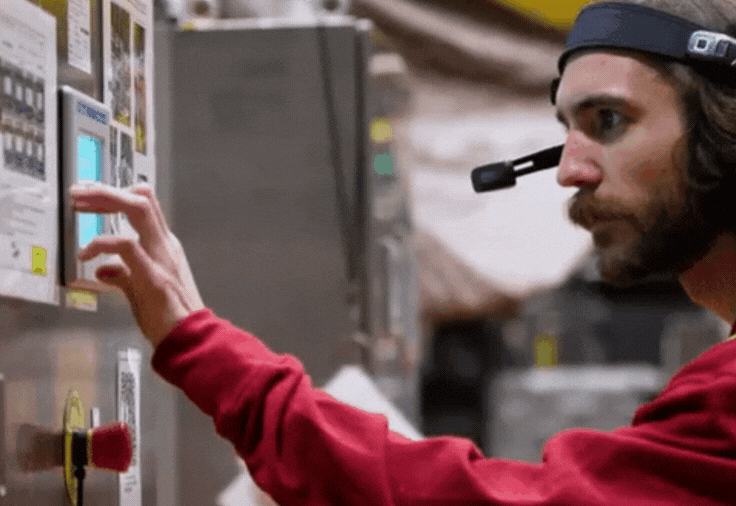
Before

Onboarding took a longer time to learn processes, and team members relied on learned knowledge to excel in their roles.
Now
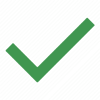
Now, skilled people make fewer errors. Immediate access to the right information in 52 languages improves first-time-right and reduces rework and quality issues.

We put new knowledge out there on the shop floor in an accessible way, and we have the technology that facilitates the step-by-step instructions to guide people in their way of working.
The return on investment
OPIs ↑
HEINEKEN has boosted Operational Performance Indicators by reducing downtime and changeover times.
Extract Losses ↓
Product losses have been reduced dramatically thanks to fewer human errors.
FTR ↑
5S ↑
CLT Standards ↑
Improved Coaching and Training
The solution that shows your manufacturing problems—and fixes them too
Drive continuous improvement in availability, performance, quality, and workforce enablement.
Quickly identify problems and take action faster with L2L. Empower your teams to achieve daily wins and drive success every day.
Trusted by leading sites around the globe.