How BorgWarner
improved OEE by 10%
BorgWarner is one of the world’s largest automotive suppliers and focuses on sustainable mobility solutions.
With L2L, the BorgWarner team has improved:
-> Data collection and analysis process
-> Communication and issue resolution
-> Production floor visibility and optimization
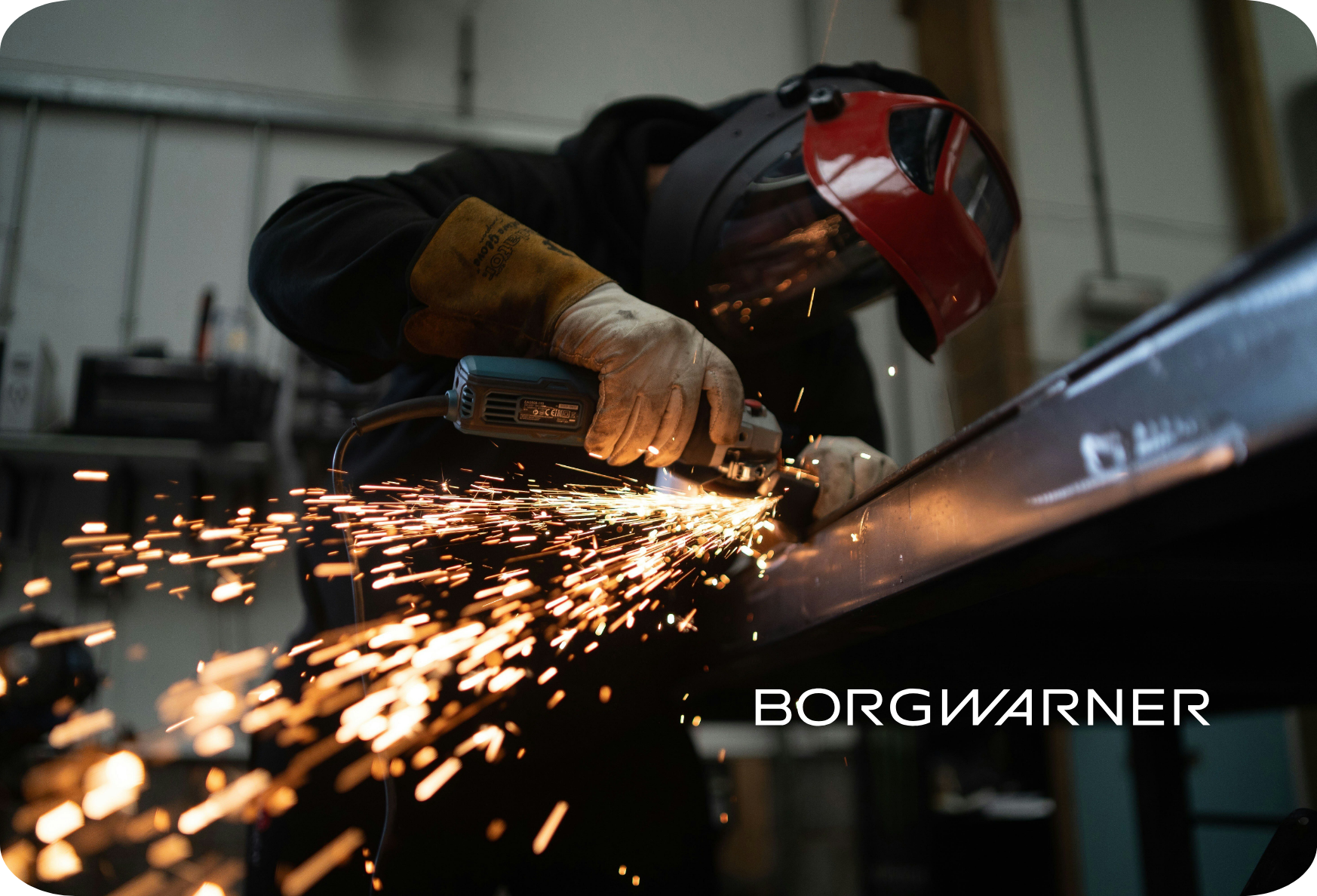
BorgWarner x L2L achievements
Streamlining data analysis
BorgWarner was able to eliminate manual data collection and analysis from multiple sources. Now, L2L captures, standardizes, and consolidates the data in one place.
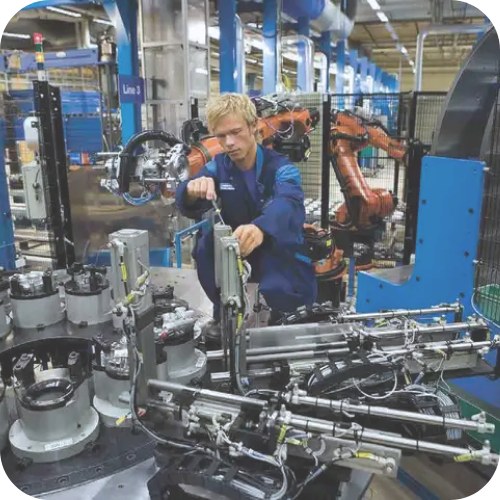
Before

Plant managers spent up to 40 hours manually collecting and analyzing production data from high-end enterprise software and spreadsheets.
Now
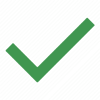
Data can now be collected and analyzed in as little as 20 minutes, saving time and allowing BorgWarner to focus on strategic initiatives.
Reducing downtime and improving quality
BorgWarner uses L2L as its main communication method on the shop floor, ensuring issues are communicated and resolved in a timely manner.
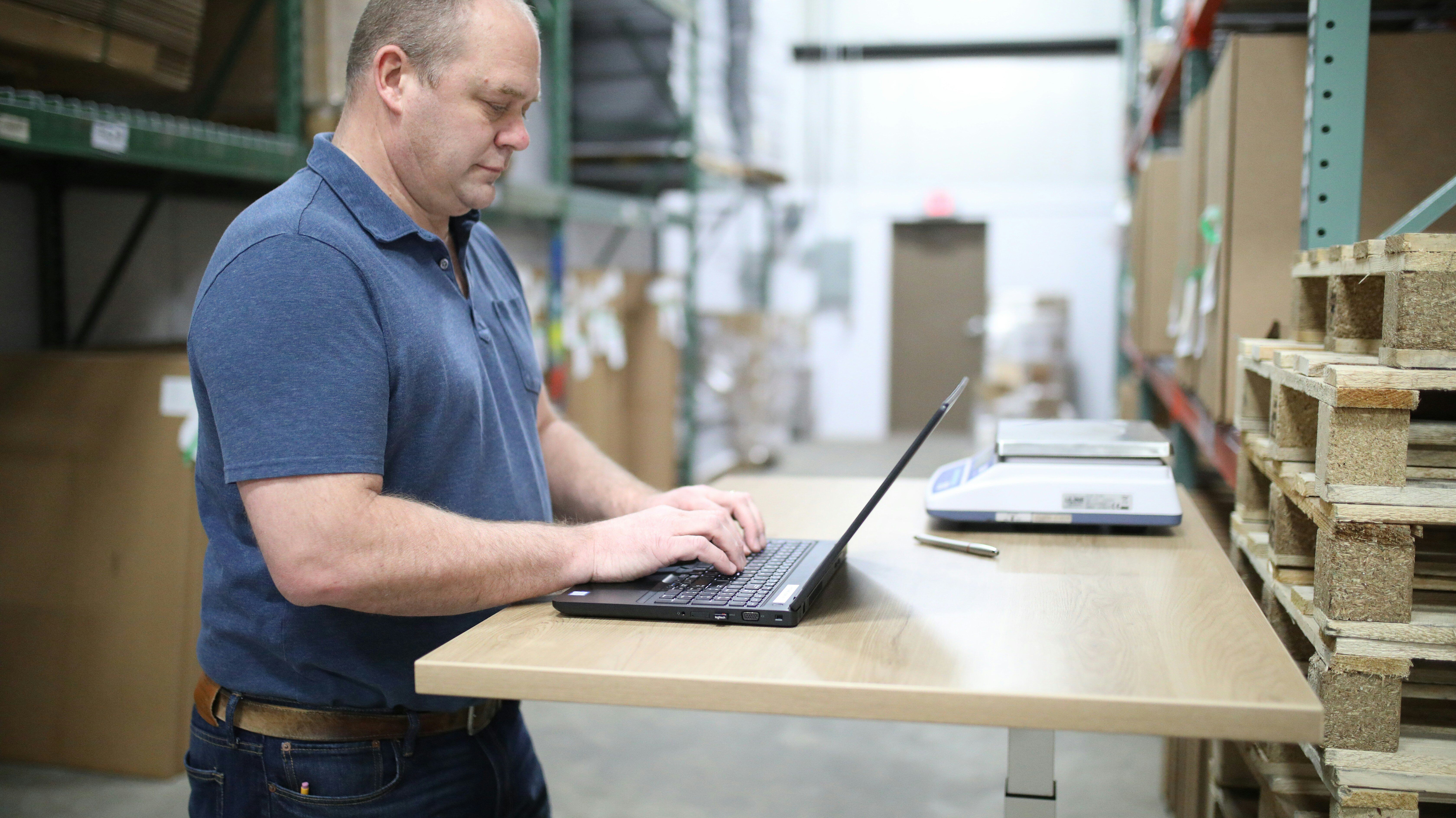
Before

Information was delayed for hours or days, meaning problems were not addressed in real time and were left unresolved.
Now
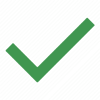
Communication occurs in real time, and issues can be solved on the line right as they occur to reduce downtime.
Empowering real-time decision making
Real-time production performance from L2L’s system ensured that BorgWarner could make adjustments, see immediate results, and optimize productivity.
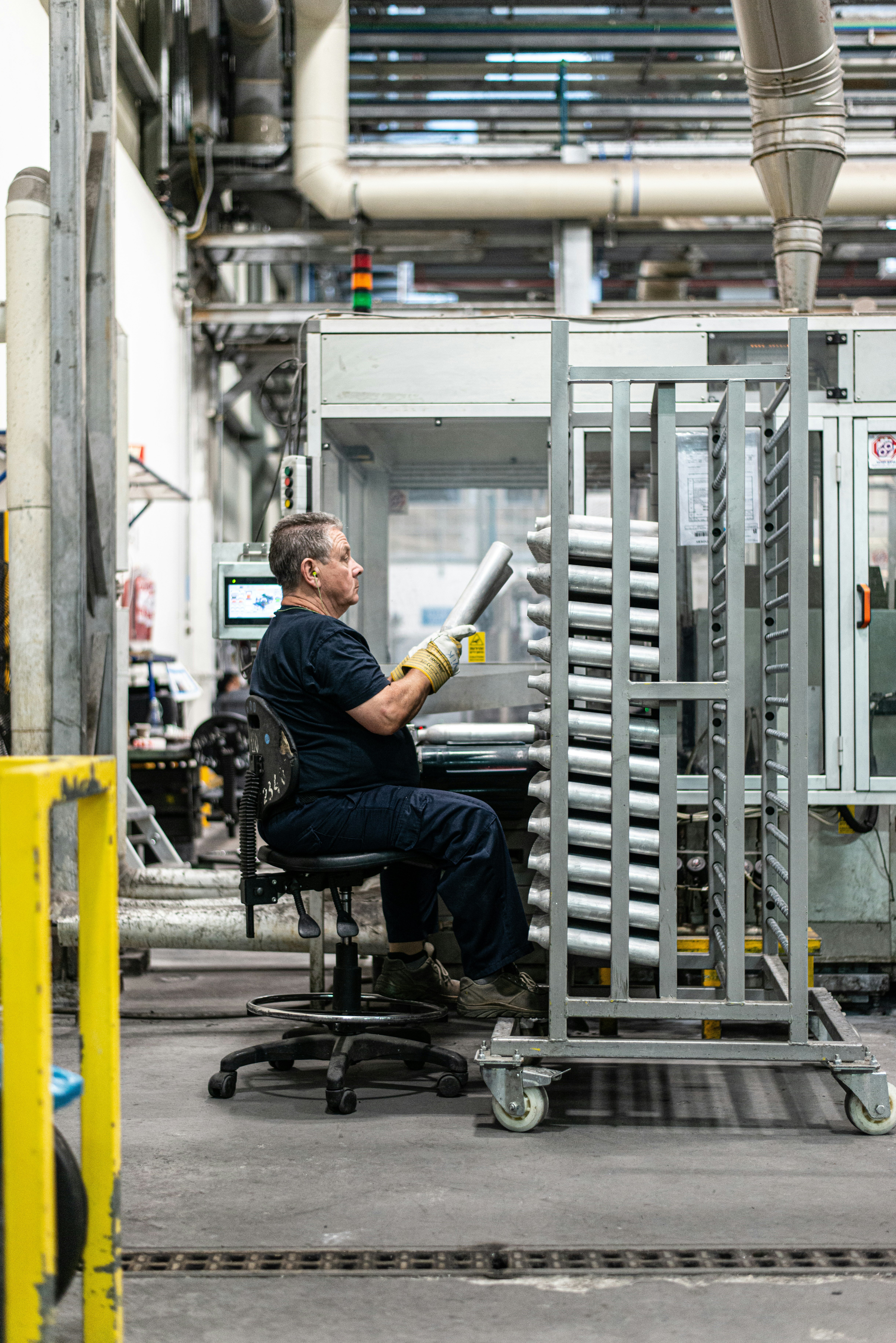
Before

Production teams were frustrated by the lack of visibility into chronic issues that impacted production. This led to an inability to problem-solve in real time.
Now
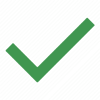
BorgWarner can see real-time production performance and work order status, helping teams problem-solve more effectively.

L2L offers data at an extremely intuitive level. It’s actionable data. The report structures are so easy to manage that it allows for very easy determinations of cause and effect around failures.
The return on investment
120x faster data analysis
Data analysis that used to take a week now takes 20 minutes
OEE ↑
10% increase in Overall Equipment Effectiveness
Operational availability ↑
Operational availability reached 90% in some areas
First Pass Yield ↑
The solution that shows your manufacturing problems—and fixes them too
Drive continuous improvement in availability, performance, quality, and workforce enablement.
Quickly identify problems and take action faster with L2L. Empower your teams to achieve daily wins and drive success every day.
Trusted by leading sites around the globe.