How ADAC reduced downtime events by 62%
ADAC Automotive designs and manufactures vehicle access systems, including door handles and liftgate handles.
With L2L, the ADAC team has improved:
-> Rapid response system for production issues
-> Real-time performance monitoring
-> Proactive maintenance management
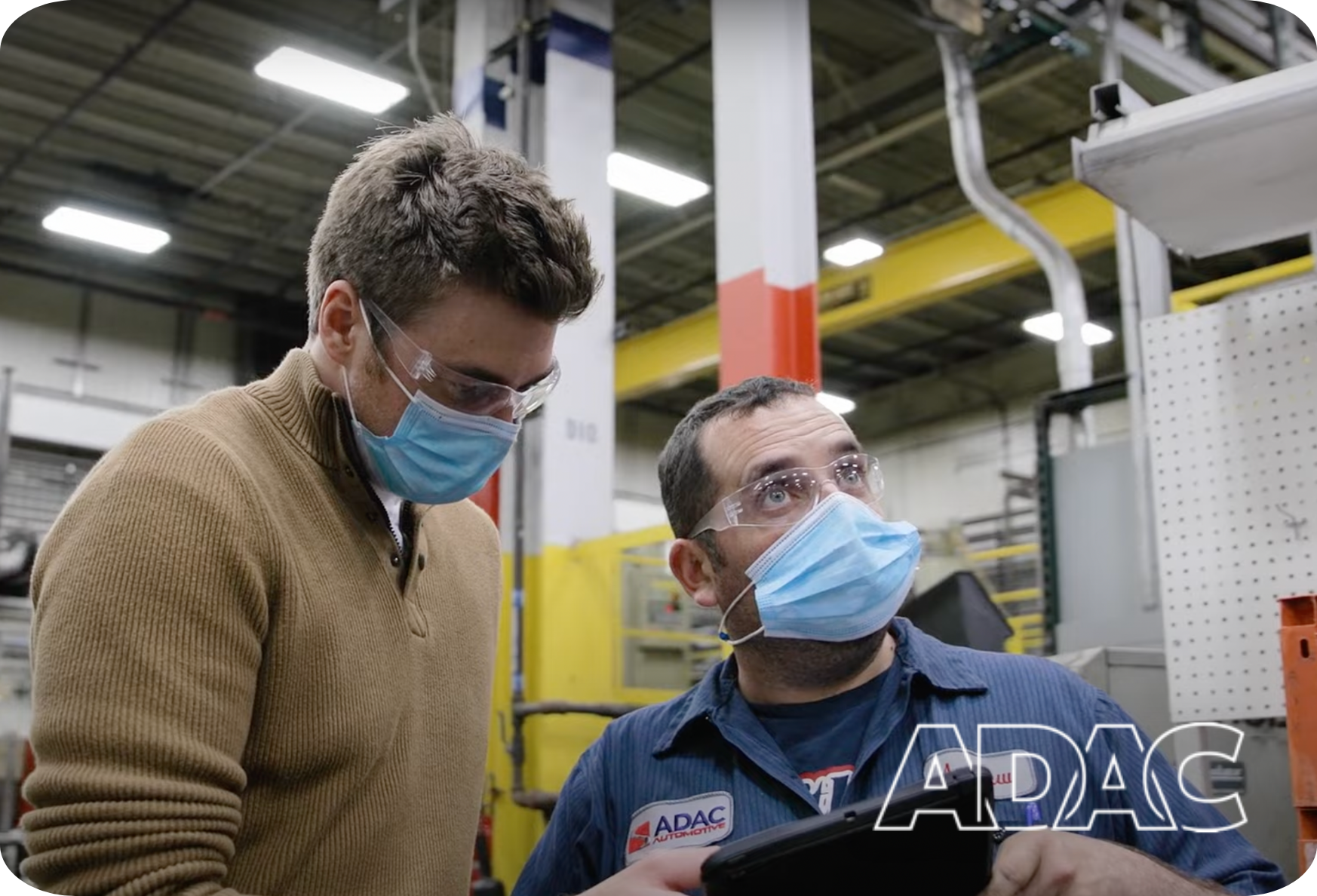
ADAC x L2L achievements
Propelling operations
"A lot of software solutions drive companies down a narrow path and solve a small set of issues. ADAC is using L2L to effectively execute 50+ business processes across our value streams."
- Rick Vande Kopple, Vice President of Quality
Digital transformation
ADAC implemented L2L with tablet and mobile access, providing real-time information visibility to all levels of the organization, when and where they need it.
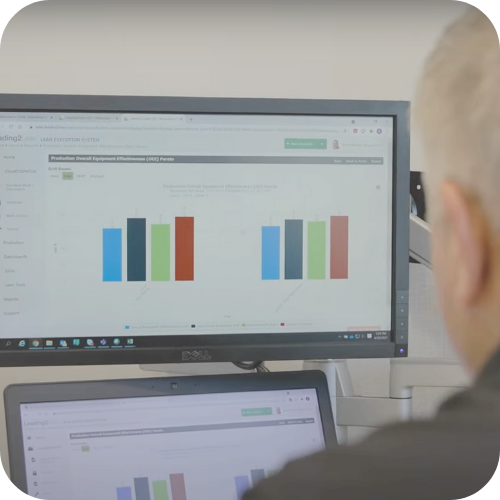
Before

ADAC was relying on manual, paper processes that wasted time and limited real-time visibility.
Now
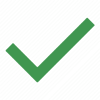
ADAC has a unified digital platform that has eliminated paper-based inefficiencies.

It puts more knowledge in [employees'] hands and in turn gives them more power to do their job.
One unified platform
ADAC established a single source of truth through L2L's integrated system. Everyone—from managers to directors to corporate—can identify and put resources toward the same opportunities for operational improvement.
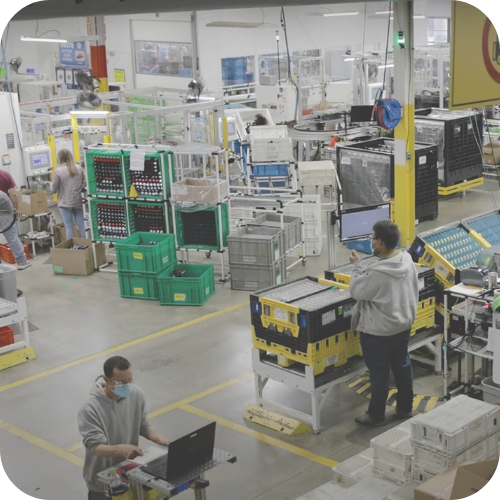
Before

ADAC was operating with siloed communication systems, making it difficult to identify bottlenecks, track progress, and make informed decisions.
Now
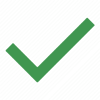
ADAC has enabled stakeholders at every level to see the same data, allowing them to better align on areas of opportunity, increase collaboration, and foster better problem-solving.

Prior to L2L, everybody had their own isolated packets of information. Now with L2L, we have a single point of truth that all of us can use to problem solve.
Rapid response system for production issues
ADAC uses L2L as a unified communication system for operators, maintenance, and plant supervisors. This lets them efficiently communicate about shop floor issues and deploy maintenance to issues in real time.
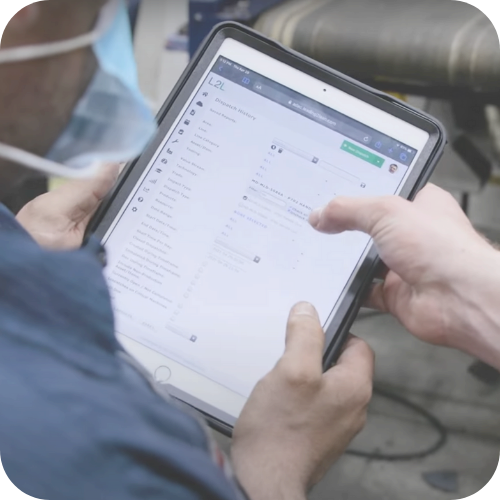
Before

Just-in-time pressure required quick response and resolution to product flow interruptions.
Now
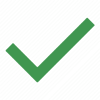
ADAC achieves faster response times to downtime events through improved tracking and communication.

The move from paper-based production recording methods to an integrated cloud-based system ensured the right people were at the right place at the right time.
Real-time performance monitoring
Real-time and historical data equipped ADAC teams with the information they need to see how process changes improve plant operations. This enabled them to make strategic improvements based on real-time insights.

Before

ADAC had difficulty distinguishing between historical and current operational status, hampering real-time decision-making.
Now
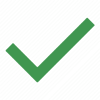
ADAC can empower leaders with actionable data to make strategic decisions and improvements based on performance.

We have achieved real-time visibility of critical metrics and enabled fast and accurate responses, increasing efficiency throughout our plants. L2L will continue to be a strategic partner, and the system will continue to play a big role as we strive for operational excellence.
The return on investment
OEE ↑
15% increase in OEE
Downtime ↓
62% reduction in major downtime events
Preventive maintenance
367% improvement in on-time preventive maintenance
Fewer tasks ↓
Process improvement
Strategically managing over
50 business processes
100s of assets ↑
The solution that shows your manufacturing problems—and fixes them too
Drive continuous improvement in availability, performance, quality, and workforce enablement.
Quickly identify problems and take action faster with L2L. Empower your teams to achieve daily wins and drive success every day.
Trusted by leading sites around the globe.