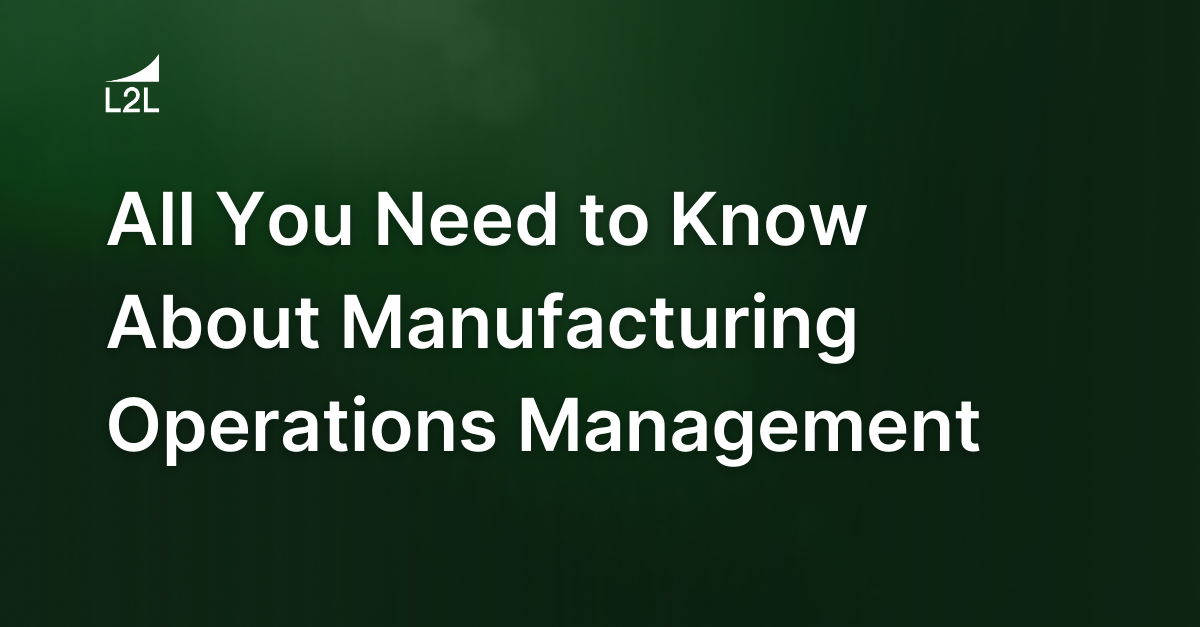
To achieve optimal efficiency and profitability, manufacturers must have an effective Manufacturing Operations Management (MOM) system — an all-encompassing approach to end-to-end process optimization. The purpose of MOM is to enable operational excellence through continuous governance and management of every step in the manufacturing process.
In this article, we’ll discuss the ins and outs of a modern Manufacturing Operations Management system: What it is, its components, the technologies involved, and best practices for implementing and running a MOM system in your organization.
What is Manufacturing Operations Management?
In short, a MOM system is a collection of tools and systems that help manufacturers create and manage efficient end-to-end processes, from supply chain planning to packaging and distribution. There are various types of MOM software on the market, but each is designed with the primary goal of maximizing efficiency.
An effective Manufacturing Operations Management system offers many benefits, including:
-
Workforce empowerment: Unifying systems and departments involved in manufacturing operations allows workers greater visibility into production processes and improves communication.
-
Better quality control: MOM software facilitates quality improvement by increasing production efficiency, enabling faster elimination of quality issues, and optimizing material storage.
-
More informed decision-making: MOM systems help teams make faster and more informed decisions by collecting real-time data across manufacturing processes.
-
Competitive advantage: Companies can boost competitiveness by leveraging their MOM system’s process streamlining capabilities, getting high-quality products to customers fast.
-
Waste reduction: An effective MOM system helps companies reduce scrap and other types of waste throughout the entire manufacturing process by optimizing the use of resources and improving quality.
-
Better compliance: MOM systems support better state and federal regulatory compliance with capabilities like real-time tracking, analytics, and automated documentation.
-
Increased profitability: Finally, a comprehensive and effective MOM system will ultimately boost an organization’s profitability due to process optimization, quality improvements, and resource efficiency.
The areas covered by Manufacturing Operations Management
Manufacturing Operations Management is designed to optimize every major process involved in turning raw materials into finished products.
Production management
Production management involves planning, coordinating, and controlling the manufacturing process to ensure efficient production of goods. MOM optimizes production management by integrating real-time monitoring, automated scheduling, and workflow optimization.
This ensures seamless coordination between different stages of production, minimizes downtime, and maximizes output, leading to more efficient and cost-effective manufacturing operations.
Quality management
Quality management focuses on ensuring finished products meet specified standards and customer expectations. MOM helps manufacturers improve quality management by embedding quality control measures into the production process.
These measures can include automated inspections, real-time defect tracking, and comprehensive data analysis. These features help identify and resolve issues promptly, helping manufacturers ensure high product quality and minimize rework and waste.
Inventory management
Inventory management oversees the control of raw materials, work-in-progress items, and finished goods and products. MOM enhances inventory management by providing real-time visibility into inventory levels, movements, and usage. This allows manufacturers to optimize stock levels, avoid overstocking or stockouts, and improve resource utilization.
With accurate and efficient inventory tracking, MOM helps reduce inventory costs and improve overall supply chain efficiency.
Maintenance management
Maintenance management is designed to keep equipment and machinery in good working condition and prevent unexpected breakdowns. MOM optimizes maintenance management by enabling predictive and preventive maintenance strategies, offering tools for monitoring equipment health, scheduling regular maintenance tasks, and analyzing performance data.
This proactive approach helps reduce downtime, extend equipment lifespan, and improve operational efficiency.
Labor management
Labor management involves planning and managing the workforce to ensure optimal productivity and efficiency. With an effective MOM system, manufacturers can optimize labor management with digital scheduling tools, labor performance tracking, and streamlined workforce allocation.
By analyzing labor data and automating routine tasks, MOM helps manufacturers maximize productivity, reduce labor costs, and improve worker satisfaction.
Supply chain management
Supply chain management encompasses the planning and coordination of the entire supply chain, from raw material procurement to product delivery. MOM aids in effective supply chain management by providing real-time data on inventory levels, production status, and supplier performance.
This improves visibility and coordination across the supply chain, enabling better demand forecasting, efficient resource allocation, and timely deliveries, ultimately leading to a more responsive and agile supply chain.
Logistics management
Logistics management involves the planning and execution of the movement and storage of goods. MOM optimizes these processes by providing real-time tracking and analysis of transportation and warehousing activities. This helps in optimizing routes, reducing transit times, managing storage efficiently, and ensuring timely and cost-effective logistics operations.
This is another way in which Manufacturing Operations Management contributes to improved customer satisfaction and reduced operational costs.
MOM software support
Manufacturing Operations Management often requires a combination of multiple industrial software solutions that work together to oversee the major functions of manufacturing.
To support a robust MOM system, you’ll typically need:
-
A Computerized Manufacturing Maintenance System (CMMS) for maintenance tasks
-
A Manufacturing Execution System (MES) for production process monitoring
-
An Enterprise Resource Planning (ERP) system for overall business management
-
A Quality Management System (QMS) for achieving quality and compliance objectives
-
A Supply Chain Management (SCM) system to manage the flow of resources across the supply chain
-
A Human Capital Management (HCM) system for workforce management and tracking
Enterprise-level organizations may use additional software solutions in their MOM systems. However, many can support an adequate MOM using elements of traditional manufacturing software. Many companies opt for solutions like L2L’s Connected Workforce Platform to handle operations management functions on a single platform without paying for functionalities they don’t need.
When choosing the right MOM solution for your business, it’s important to make the following considerations:
-
Comprehensive functionality: Ensure the software covers all key areas, including production management, maintenance, quality control, and supply chain management.
-
Ease of integration: Look for a solution that integrates seamlessly with your existing systems and equipment.
-
Scalability: Choose a platform that can grow with your business and adapt to increasing demands.
-
User-friendly interface: A simple and intuitive interface can significantly reduce the learning curve and increase adoption rates among your team.
-
Real-time data and analytics: Real-time insights and analytics are crucial for making informed decisions and quickly addressing any issues that arise.
5 best practices for effective operations management in manufacturing
While Manufacturing Operations Management may look different for every industrial company, each system should incorporate the following best practices for maximum effectiveness.
1. Implement lean manufacturing principles
Lean manufacturing principles are foundational to an effective MOM system. They can include:
-
Reducing waste: Identify and eliminate waste in all forms (overproduction, waiting time, transportation, excess inventory, motion, over-processing, and defects) to increase efficiency.
-
Focusing on continuous improvement (Kaizen): Foster a culture of continuous improvement where every employee is encouraged to suggest ways to improve processes.
-
Implementing Just-in-Time (JIT) production: Produce what is needed, when it is needed, and in the amount needed to minimize inventory costs and reduce waste.
2. Leverage technology
Modern MOM systems require the integration of advanced digital technologies, such as:
-
Automation: Deploy automation technologies where possible to increase production speed, improve accuracy, and reduce labor costs.
-
ERP Integration: Utilize software solutions like Enterprise Resource Planning (ERP) systems and L2L to integrate various business processes from inventory and order management to production, finance, and customer relationships, ensuring data consistency and streamlining operations.
-
Advanced analytics and IoT: Use sensors and Internet of Things (IoT) devices for real-time data collection. Employ advanced analytics to make informed decisions and predict maintenance needs or production bottlenecks.
3. Focus on quality
Optimal product quality must be a key focus when implementing a MOM system, with each system component supporting quality goals. Here’s how to maintain high quality standards:
-
Adopt international standards: Implement and maintain quality management systems such as ISO 9001 to enhance customer satisfaction and operational efficiency.
-
Perform regular audits and inspections: Conduct regular quality audits and inspections to ensure processes are up to standard and to identify areas for improvement.
-
Reiterate the importance of quality: Continuously train employees on quality standards and the importance of their roles in maintaining those standards.
4. Develop a skilled workforce
Your Manufacturing Operations Management system will only work if your employees understand its value and receive adequate training.
-
Ensure ongoing training and development: Invest in regular training and development programs to keep the workforce skilled and knowledgeable about the latest technologies and practices.
-
Employee engagement: Engage employees in decision-making processes, recognize their contributions, and create a positive work environment to boost morale and productivity.
-
Succession planning: Prepare for the future by developing talent from within through mentorship programs and career development plans to fill key positions.
5. Standardize processes and procedures
Make sure you standardize best practices and make them accessible to workers using the following tactics:
-
Develop Standard Operating Procedures (SOPs): Standardize work by writing SOPs for all applicable critical tasks and processes. They should provide clear instructions that are easy to follow.
-
Implement Leader Standard Work (LSW): The work performed by supervisors, team leaders, managers, and even executives can be standardized to varying levels of degree. Learn more in our guide to LSW.
-
Ensure proper documentation: Best practices should always be written down. Create work instructions in a digital format so the documentation is easier to update, access, and use.
Optimize your manufacturing operations with L2L
Effective operations management is crucial for remaining competitive and profitable. However, your MOM system doesn’t have to include every major manufacturing software category, especially if you’re looking to maximize cost-effectiveness.
L2L provides an excellent alternative to typical MOM solutions, covering everything from maintenance to quality control on a single, easy-to-use platform. Here’s how it works:
-
Maintenance: Our powerful CMMS module allows operators and technicians to handle maintenance tasks with speed and precision while providing plant leadership with a real-time view of maintenance operations.
-
Production: L2L’s production management capabilities help teams spot and solve common production issues like unplanned downtime, bottlenecks, and schedule conflicts.
-
Quality: L2L helps manufacturers optimize quality at every stage of production by providing real-time visibility into quality issues and quick, simple ways to address them. Plus, our quality management capabilities empower the entire frontline, not just QA inspectors, to drive toward zero defects.
-
Worker empowerment: With L2L’s workforce enablement capabilities, manufacturers can accelerate training and onboarding and easily track and manage their workforce’s skills and certifications.
-
Manufacturing intelligence: L2L powers operations management with an intelligence layer that turns data across the end-to-end manufacturing processes into actionable insights that drive productivity and profitability.
To discover if L2L is the right solution for your operations management needs, request a personalized demo with one of our manufacturing experts, or reach out to sales@l2l.com with specific questions!
Revisions
Original version: 1 August 2024
Written by: Evelyn DuJack
Reviewed by: Daan Assen
Please read our editorial process for more information
Related Posts
Subscribe to Our Blog
We won't spam you, we promise. Only informative stuff about manufacturing, that's all.