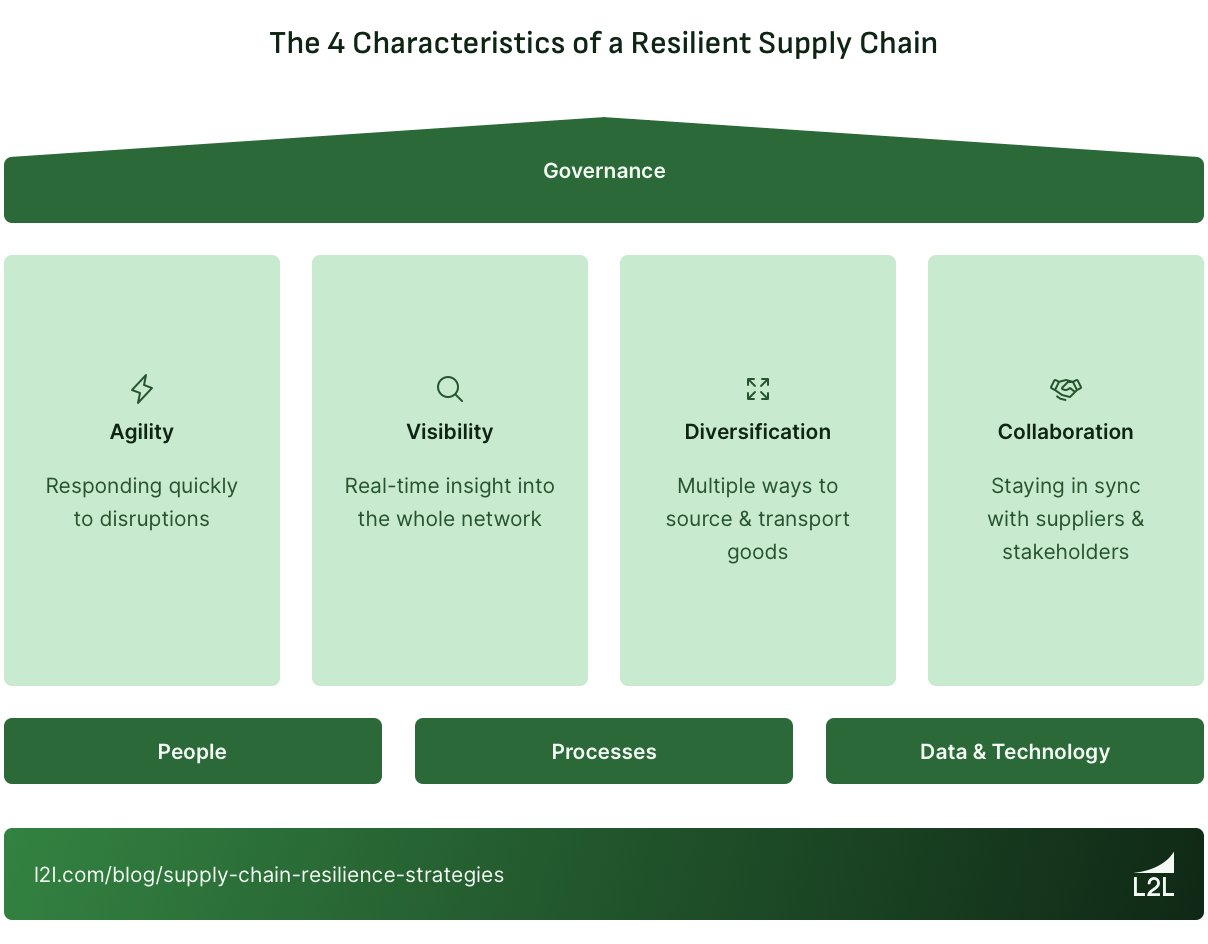
Supply chain resilience has become one of today’s top concerns among manufacturers. Global disruptions like the Covid-19 pandemic have forced companies to prioritize supply chain agility and flexibility.
Building a resilient supply chain will only become more important in the near future. Companies that invest in supply chain resilience are more likely to:
- Mitigate risks: By adopting practices such as supplier diversification and using predictive analytics in forecasting and demand planning, companies can minimize risks and reduce the impact of disruptions.
- Improve continuity: Supply chains that are resistant to disruptions decrease the risk of shutdowns, late shipments, stockouts, and other problems that impact operations and customer relationships.
- Stay compliant: Companies that invest in supply chain resilience tend to have an easier time adapting to EHS regulations and implementing sustainable practices.
- Save money: Improving flexibility and agility helps companies reduce long-term supply chain costs by minimizing waste and lessening the impact of disruptions.
In this article, we’ll cover how to improve supply chain resilience and explore strategies manufacturers can use to safeguard their supply chains in 2025.
What it means to have a resilient supply chain
Supply chain resilience refers to a supply chain’s capacity to resist and recover from disruptions. Having a resilient supply chain gives your business a major competitive advantage, especially during times of economic volatility and geopolitical uncertainty.
The primary characteristics of a resilient supply chain include:
- Agility: Resilient supply chains are agile (or flexible)—meaning they can react quickly to changes and disruptions. The greater a supply chain’s agility, the faster and more seamlessly businesses can respond to the unexpected.
- High visibility: Visibility into every area of the supply chain network is crucial for bolstering resilience. End-to-end visibility helps companies mitigate disruptions and dramatically improve forecasting.
- Diversification: Diversifying suppliers, trade routes, and even transportation methods enables companies to adjust plans at a moment’s notice and helps them maximize cost-effectiveness.
- Close collaboration: Seamless collaboration with suppliers, distributors, and customers not only improves relationships across the supply chain but also leaves companies better prepared to weather disruptions.
Supply chains that embody these four characteristics are much better prepared to navigate major disruptions, including labor shortages, geopolitical events, and geographical disasters.
In the next section, we’ll dive into practical ways manufacturing leaders can improve supply chain resilience both now and in the future.
6 supply chain resilience strategies to consider
While you can’t safeguard your supply chain from every risk, there are tried-and-tested strategies that will help your business minimize the effects of disruptions. Let’s take a look at six ways manufacturers can boost their supply chain resilience.
1. Diversify your supply chain
Supply chain diversification is one way companies can bolster resilience in times of economic volatility. Access to a range of suppliers, vendors, and shipping and logistics options often mitigates disruptions, such as material shortages.
Advanced technologies like real-time analytics, blockchain, and the Internet of Things (IoT) make supply chain diversification more manageable than ever. In turn, diversification is becoming an increasingly attractive option for today’s manufacturers—especially those with global footprints.
For instance, dual sourcing—acquiring products from two suppliers—can safeguard companies from delays caused by material shortages and other sourcing-related issues. According to a recent Gartner survey, around 57% of industrial companies operating in China are considering a “supplier +1” strategy.
Despite its benefits, diversification introduces complexities to supply chain networks. Multiple suppliers and vendors can cause logistical challenges, and retaining extra supply locations can become expensive. This is why it’s crucial to weigh the benefits of increased resilience against the costs—logistical and financial—of supply chain diversification.
One company that successfully diversified its supply chain is Apple. The company expanded production outside of China in recent years, moving a portion of its electronics production to India, Vietnam, and other Southeast Asian countries while diversifying its component suppliers. As a result, Apple was able to minimize the impact of disruptions and lead times in certain regions.
Over-reliance on a single supplier, vendor, or trade route can disrupt operational continuity. Diversifying your supply chain can dramatically improve resilience in unpredictable market conditions.
2. Map your supply chain
Understanding every participant in your supply chain—from Tier 1 to Tier 3 suppliers—is crucial for navigating today’s complex manufacturing landscape.
Supplier tiers breakdown table. Source.
By mapping out your supply chain, you can gain visibility into where materials, components, and services originate, helping you identify potential risks and vulnerabilities at every level.
This process allows manufacturers to uncover hidden bottlenecks and dependencies that could disrupt operations. For example, identifying a Tier 3 supplier located in a region prone to natural disasters can help you proactively develop contingency plans.
Advanced digital tools make supply chain mapping more achievable than ever:
- Real-time analytics provides live data to track supplier performance, inventory levels, and potential disruptions.
- Digital twins offer virtual replicas of the supply chain to simulate scenarios and optimize processes.
- IoT sensors monitor assets and shipments in real time, providing detailed insights into supply chain operations.
- ERP systems integrate supply chain data across departments for centralized management and decision-making.
- AI and machine learning tools analyze complex data sets to predict disruptions and recommend corrective actions.
These technologies help manufacturers visualize and monitor supply chain relationships in real time. The insights gained from the mapping process help you make better, faster decisions.
3. Improve end-to-end supply chain visibility
Transparency and real-time tracking are essential for maintaining control over today’s increasingly complex supply chains. Without full visibility, manufacturers risk missing critical disruptions, delays, and inefficiencies that can snowball into bigger problems across operations.
Technology plays a vital role in improving visibility. Platforms that centralize data from supply chain partners create a single source of truth, allowing manufacturers to monitor and manage every link in the chain. These tools provide live updates, ensuring decision-makers can act quickly when unexpected issues come up.
Greater visibility also leads to more accurate forecasting and strategic, data-driven decision-making. A clearer picture of supply chain dynamics lets manufacturers anticipate challenges, align inventory with demand, and optimize production schedules to maintain efficiency and agility.
Improving supply chain visibility can also help companies ensure their products are ethically sourced. For example, the Slave-Free Alliance partnered with supply chain technology vendor Exiger to combat modern slavery and forced labor. Using advanced AI and graph technology, this alliance enables a level of supply chain visibility that helps the world’s leading manufacturers avoid unethical vendors and suppliers.
4. Practice proper inventory management
Maintaining safety stock is critical for avoiding production disruptions caused by supply chain delays, demand fluctuations, or unexpected shortages. Manufacturers can safeguard operations and meet customer demands by keeping a buffer of essential materials or products.
Inventory tracking tools enhance the effectiveness of safety stock management by providing real-time visibility into stock levels, usage patterns, and replenishment needs. These tools help manufacturers optimize inventory without overstocking while balancing operational efficiency and preparedness.
Just-in-time (JIT) and just-in-case (JIC) are popular inventory models for boosting supply chain resiliency. JIT focuses on minimizing inventory by syncing deliveries with production, cutting costs—but requiring precise coordination to avoid delays. JIC, on the other hand, keeps extra stock as a cushion against disruptions. Many manufacturers blend the two for just enough flexibility to navigate disruptions without sacrificing efficiency.
Here are a few ways you can improve your inventory management:
- Always have extra stock on hand in case of unforeseen disruptions.
- Track inventory levels in real time so you can proactively order new stock.
- Maintain enough lead time between order, supply, and transportation.
- Use demand forecasting software to optimize stock levels.
Proper inventory management helps manufacturers soften the blow of supply chain disruptions and, ultimately, maintain good customer relationships.
5. Consider nearshoring
Nearshoring has become an important conversation for U.S. manufacturers—especially in light of potential new tariffs beginning this year. The practice of relocating operations closer to a company’s home market, nearshoring offers an array of benefits, such as:
- Reduced lead times
- Lower transportation costs
- Improved supply chain responsiveness
- Better supply chain oversight compared to offshoring
However, you need to determine the feasibility of nearshoring before committing to close-to-home operations. Some organizations may have a hard time nearshoring their operations if they’ve traditionally relied on low-cost overseas labor or have specialized manufacturing processes.
When deciding whether to nearshore, you should first consider:
- Cost and availability of labor
- Proximity to key markets
- Infrastructure requirements
- Supply chain flexibility
For instance, companies like Ford and General Motors have successfully nearshored production to Mexico to take advantage of lower labor costs, favorable trade agreements, and efficient supply chains. Mexico’s skilled labor force, strong infrastructure, and commitment to sustainability make it an ideal nearshoring destination for automakers looking to enhance competitiveness while aligning with global environmental goals.
When done strategically, nearshoring enables manufacturers to streamline operations, reduce costs, and support innovation in an increasingly sustainable industry.
6. Develop contingencies
Contingency planning is all about being ready for the unexpected. It involves creating backup plans to ensure that operations keep running smoothly, even if something goes wrong—whether it’s a natural disaster, a supplier failure, or a sudden spike in demand.
To identify high-risk scenarios, companies should analyze their supply chain from end to end, looking for weak spots where disruptions could have the biggest impact.
Developing a contingency plan can include choosing alternate suppliers, holding extra inventory, or having backup logistics partners. The goal is to ensure that no matter what happens, you can keep production going and avoid costly delays.
Finally, it’s important to stress test your contingency plans. Simulating potential disruptions helps companies refine their plans over time and adjust response strategies based on real-world data and changing conditions. This helps ensure that when a disruption does occur, your supply chain is as resilient as possible.
Leverage technology to ensure supply chain resilience
Choosing the right supply chain technologies and vendors is a crucial step in building supply chain resilience. Digital tools and technologies like predictive analytics, AI and machine learning, sensors, and robotic process automation help manufacturers improve production efficiency and gain optimal visibility into their entire supply chain—so they always know what’s coming.
Improving workforce effectiveness is also key to creating a resilient supply chain. Modern solutions like connected workforce platforms not only improve operational efficiency, but they help factories pivot quickly in the face of disruptions while keeping downtime to a minimum.
Discover how connected technology can empower you to future-proof your manufacturing operations when you schedule a personalized L2L demo.
Revisions
Original version: 4 February 2025
Written by: Evelyn DuJack
Reviewed by: Michael Hurd
Please read our editorial process for more information
Related Posts
Subscribe to Our Blog
We won't spam you, we promise. Only informative stuff about manufacturing, that's all.