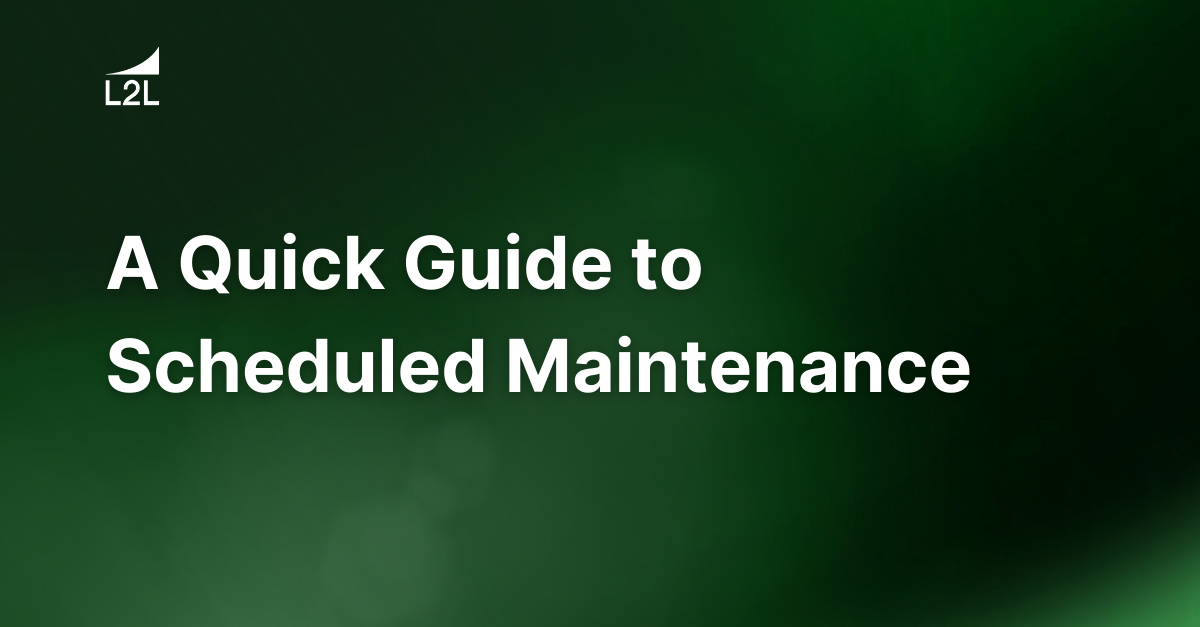
An optimal equipment maintenance schedule is your best defense against unplanned downtime. But knowing what needs to be done and who needs to do it is only part of a good proactive maintenance strategy. You need to create and execute a thorough—yet flexible—schedule for every major task involved in your maintenance processes.
Scheduled maintenance is the key to preventing work order backlogs and minimizing reactive maintenance. In this article, we’ll discuss what scheduled maintenance is, how it differs from planned maintenance, and how to use it in your manufacturing facility.
What is scheduled maintenance?
Scheduled maintenance refers to any asset repair and upkeep that happens within a specific timeframe. The goal of scheduled maintenance is to reduce maintenance issues, such as delayed repairs or unplanned downtime, while improving resource allocation.
In a factory setting, this type of maintenance involves both recurring and one-off tasks. Scheduled maintenance examples include:
-
Replacing air filters
-
Performing routine asset inspections
-
Changing a conveyor belt bearing
-
A one-time activity, like replacing a broken part
Scheduled maintenance can include cycle-based and time-based maintenance practices. It establishes who performs tasks and when.
Major benefits of scheduled maintenance include:
-
More efficient utilization of maintenance resources
-
Longer machinery lifespans
-
Lower maintenance costs
-
More collaborative workforce culture
When managed digitally—usually with a CMMS—scheduled maintenance helps manufacturers make the most of their assets and maintenance resources.
Differences between planned and scheduled maintenance
The terms scheduled maintenance and planned maintenance are often used interchangeably. However, each has a unique meaning in manufacturing. Let’s take a closer look at their differences.
Scheduled maintenance:
To reiterate, scheduled maintenance refers to a process outlining who will perform maintenance tasks and when those tasks will be performed. It’s a good way to make sure that overdue tasks are finished in a timely manner. Additionally, scheduled maintenance is part of an overall planned maintenance strategy.
Planned maintenance:
Planned maintenance is broader than scheduled maintenance. It encompasses the materials and processes needed to complete maintenance work. This includes identifying and prioritizing problems, establishing workflows, choosing the right parts, and analyzing finished tasks. Scheduled maintenance simply handles who does what—and when.
Planned maintenance strategies can include both predictive and preventive maintenance. Regardless of the strategy you choose, scheduled maintenance will always be a major component.
Using SMCP to prioritize and schedule maintenance work
Scheduled Maintenance Critical Percent (SMCP) is a key metric that helps manufacturers measure how well they adhere to planned maintenance schedules. It calculates the percentage of critical maintenance tasks completed on time within a given period. This helps you minimize equipment failure by prioritizing essential upkeep activities and executing maintenance activities as planned.
You can calculate SMCP by tracking scheduled maintenance activities, identifying which are marked as critical, and comparing their completion dates against the schedule:
A high SMCP score means your team is staying on top of essential tasks, while a low score signals potential gaps in execution or resource allocation. By improving your SMCP score, you can ensure your most important equipment remains in optimal condition.
Plan, schedule, and coordinate maintenance work with a connected workforce platform
Scheduled maintenance gets a major upgrade with connected workforce technology. Giving maintenance teams instant access to real-time data and collaborative tools lets them seamlessly coordinate tasks, access detailed work instructions, and log updates. This connectivity ensures work orders are completed on time, minimizing disruptions and maximizing uptime.
Connected workforce platforms provide clear visibility into equipment status, predictive analytics, and streamlined workflows, empowering teams to act proactively. The result? Maintenance is faster, more efficient, and much more cost-effective.
Ready to transform your scheduled maintenance processes? See how L2L simplifies work order completion and more with our FREE Interactive Product Tour.
Revisions
Original version: 9 January 2025
Written by: Evelyn DuJack
Reviewed by: Daan Assen
Please read our editorial process for more information
Related Posts
Subscribe to Our Blog
We won't spam you, we promise. Only informative stuff about manufacturing, that's all.