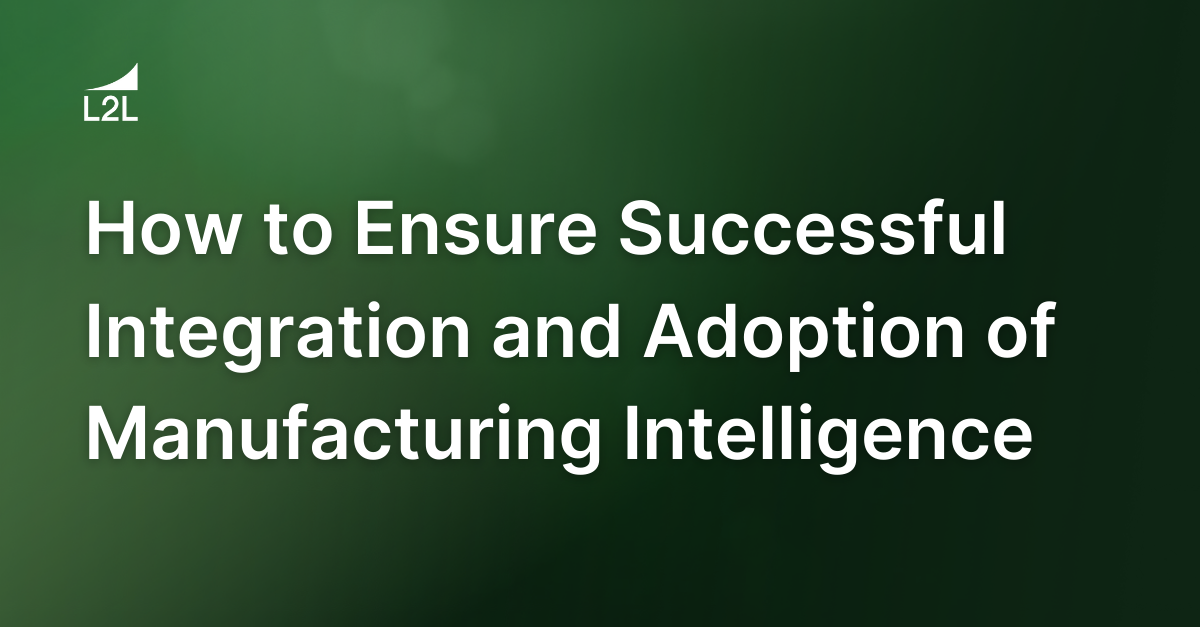
To stay competitive in today’s market, manufacturers must find new and innovative solutions for overcoming major challenges, from supply chain disruptions to changing customer demands.
We’ve seen how advanced digital technologies, such as the Industrial Internet of Things (IIoT) and robotic automation, optimize production processes and improve product quality. However, most industrial companies have yet to realize the full power of their manufacturing data.
That’s where manufacturing intelligence (MI) comes in.
In this article, you’ll learn:
-
How manufacturing intelligence unlocks real-time insights into manufacturing operations
-
Key technological components of these systems
-
Practical tips for MI integration and adoption
Let’s take a closer look at the elements of a successful MI system.
What is manufacturing intelligence and how does it work?
So, what is manufacturing intelligence, anyway?
MI is an approach to maximizing the value of a manufacturer’s data. It uses software that analyzes data from multiple sources to drive real-time or near-real-time visibility into manufacturing operations. This data can then deliver comprehensive and accurate insights into operational performance.
Simply put, MI software helps organizations use their data to make better decisions.
The key components of a manufacturing intelligence system, often known as an enterprise manufacturing intelligence (EMI) system, include:
-
Data collection: This sets the entire foundation for your MI system. MI collects data from sources like Internet of Things (IoT) sensors, programmable logic controllers (PLCs), human inputs, and integrations with manufacturing software (e.g. SCADA, MES, CMMS).
-
Data processing: Once the data is collected, the MI system will clean, organize, and analyze it. This process makes sense of raw data, converting it into useful information for you and your teams.
-
Data visualization: The final component of manufacturing intelligence is turning insights into a visual format that’s easy for manufacturing teams to understand.
The goal of MI is to turn relevant data into digestible information that empowers everyone—from frontline workers to corporate executives—to drive productivity and efficiency.
It’s important to note that a manufacturing organization’s IT department plays a critical role in the success of manufacturing intelligence initiatives. From choosing the right solutions to ensuring smooth adoption, IT leaders must help implement and maintain your manufacturing intelligence system.
Overcoming common challenges with manufacturing intelligence software integration
Introducing new technologies into your manufacturing processes requires careful planning, experimentation, and refinement.
Here’s how you and your IT teams can overcome common challenges—from planning to execution—during MI integration.
Have a clear integration roadmap
Having a clear manufacturing intelligence integration roadmap is crucial for keeping your digital transformation efforts on track and aligned with business goals. A well-defined roadmap helps you avoid pitfalls, reduce risk, and ensure all stakeholders are on the same page.
Key benefits of a phased approach to integration include:
-
Minimized disruption: By rolling out in stages, you can limit system downtime and avoid overwhelming your teams.
-
Manageable change: Each phase builds on the last, making it easier for teams to adopt and integrate new processes.
-
Scalability: A phased plan allows you to fine-tune the solution as you scale it across the organization.
Additionally, prioritizing quick wins is essential for successful MI integration. Target low-effort, high-impact areas first to showcase immediate value. This not only helps build buy-in from stakeholders but also demonstrates the ROI of your MI solution early on. By showing fast results, you can maintain momentum and set the stage for long-term success.
Avoid data silos and fragmentation
Integrating disparate systems and unifying data sources in manufacturing can be challenging but is key to unlocking the full potential of MI. To make the process smoother, it’s important to follow best practices that ensure data consistency and streamline workflows.
Here are a few critical steps:
-
Start with a clear data strategy: Define what data is most valuable, how it will be used, and how it needs to flow between systems. This prevents unnecessary complexity and ensures all data aligns with business goals.
-
Use standardized data formats: Wherever possible, adopt common standards or frameworks (like OPC UA) to make data easier to share and integrate across platforms. Standardization simplifies integration and avoids communication breakdowns between systems.
-
Implement middleware: Middleware can act as a bridge between systems, enabling real-time data sharing without overhauling existing infrastructure. It streamlines connections, making it easier to unify data sources across old and new systems.
Finally, test and validate your integrations in small phases. This ensures everything works correctly before rolling out to larger parts of your operation, reducing risk and improving overall data reliability.
Ensure scalability
Your MI system should grow with your business, so it’s crucial to build it with scalability in mind. This means selecting flexible, modular solutions that can easily adapt to new technologies, increased production demands, and evolving business goals without requiring constant rework.
Key strategies for ensuring scalability include:
-
Invest in cloud-based solutions: Cloud infrastructure lets you scale up (or down) as needed, without the heavy upfront costs of on-premise systems. It provides the flexibility to add new features, integrate additional data sources, or expand to multiple sites easily.
-
Prioritize interoperability: Make sure your MI system is designed to integrate with both current and future tools. Open APIs and standard communication protocols (like MQTT or OPC-UA) ensure that your system can connect with new machines, sensors, or platforms as your business grows.
-
Plan for continuous updates: Regular software updates, both for security and functionality, ensure your system stays up-to-date with the latest technology trends. This future-proofs your MI system and enables you to stay competitive as the market evolves.
Finally, keep a long-term roadmap in place, revisiting it regularly to align with growth and strategic shifts. This keeps your MI system aligned with business objectives, ensuring it evolves alongside your operations.
Choose the right technology partners
When evaluating MI platforms, focus on core factors that directly impact your ability to integrate, scale, and future-proof the solution.
First, integration capabilities are key. Look for platforms that easily connect with your existing systems and equipment using open APIs or standardized protocols. This ensures seamless data flow and minimal disruption during implementation and integration.
Platform features should align with your operational needs. Evaluate whether the platform offers real-time analytics, customizable dashboards, and predictive maintenance tools. These features can enhance decision-making and improve overall efficiency.
Scalability is essential as your business grows. Ensure the platform can handle increasing data volumes, multiple plant locations, and new technology integrations without compromising performance. A cloud-based platform typically offers the most flexibility here.
Minimize cybersecurity risks
Protecting sensitive production data is critical to maintaining operational integrity and avoiding costly breaches. Here are some best practices for securing your data with robust measures:
-
Implement role-based access control (RBAC): Limit access to sensitive data based on job roles. This ensures that only authorized personnel can view or modify critical information, reducing the risk of insider threats.
-
Encrypt data: Both at rest and in transit, encryption protects your data from being intercepted or accessed by unauthorized users. Use strong encryption standards to ensure comprehensive protection.
-
Regularly update and patch systems: Outdated software can leave vulnerabilities that hackers exploit. Keep all systems, software, and firmware up to date to address potential security risks.
-
Conduct regular security audits: Periodically review your security protocols to identify and address any gaps. Audits ensure your systems stay compliant with industry standards and best practices.
By following these best practices, you can safeguard sensitive production data and maintain the trust of your customers and stakeholders.
Ensuring successful adoption by the manufacturing team
Adopting manufacturing intelligence technology can transform your operations, but successful implementation requires more than just installing the tools. It takes a solid strategy to ensure your team embraces and effectively uses the new system. Here’s how you can set your teams up for success.
Create a change management strategy
Building a holistic change management strategy is crucial for ensuring a smooth adoption process. First, you need strong buy-in from leadership and key stakeholders. When leaders champion the change, it trickles down to the rest of the organization. Make sure leadership understands how MI aligns with business goals and the long-term benefits it brings.
It’s also important to address resistance to change. Some employees might worry about how MI will impact their roles or feel overwhelmed by the shift in workflows. Communicate openly about the reasons for the change, and offer reassurances that the new technology is there to support them, not replace them.
By clearly communicating these benefits and ensuring support at every level, you’ll secure the buy-in for a smooth adoption process, setting the stage for long-term success.
Provide training and support
Even the best technology won’t deliver results if people don’t know how to use it. Offer comprehensive training that empowers employees with the skills they need to use MI tools effectively. Hands-on sessions can ease anxiety and build confidence in using the new systems.
Keep the support going with ongoing upskilling initiatives. As the MI system evolves and new features roll out, ensure that workers continue receiving the training they need to stay up to date.
Leverage user-friendly dashboards
To encourage adoption, make sure your manufacturing intelligence platform is user-friendly. Customizable, intuitive dashboards allow employees to engage with the data in a way that’s meaningful to them. A simple interface makes it easier for teams to find the insights they need without sifting through complex data sets.
Simplified data visualization is also key. Presenting data in clear, digestible formats reduces complexity, helping operators quickly identify issues and take action in real time.
Data is key to success in the modern manufacturing environment
Manufacturing intelligence integration and adoption must happen in stages, each building upon the other. Before beginning your MI journey, you must prepare your manufacturing data for MI integration. This involves:
-
Making sure you collect the right data from assets, systems, and processes
-
Cleaning your data, which includes removing inaccuracies from your datasets
-
Choosing the right manufacturing intelligence use cases for your plant
Naturally, IT leadership plays a critical role in this process—along with ensuring smooth adoption. Involving IT teams in every stage of MI implementation, integration, and adoption will help every manufacturing team maximize the benefits of intelligent technologies.
Choosing the right technology partner is another non-negotiable when it comes to successful MI integration and adoption. Low-code connected workforce platforms like L2L make it easy for manufacturers to get started on their MI journeys.
L2L Business Intelligence (BI) lets users merge manufacturing data with existing systems.
Our intelligence layer helps workers act with confidence and precision, empowering them with real-time data from manufacturing and business intelligence (BI) systems. With AI-powered guidance, seamless BI integration, and simple workflow automation, L2L offers the manufacturing intelligence features essential to accelerating your MI strategy.
Want to learn more? Schedule a demo with our MI experts or reach out to sales@l2l.com with any questions.
Revisions
Original version: 17 October 2024
Written by: Evelyn DuJack
Reviewed by: Daan Assen
Please read our editorial process for more information
Related Posts
Subscribe to Our Blog
We won't spam you, we promise. Only informative stuff about manufacturing, that's all.