Go digital. Modernize your manufacturing operations.
Trusted by global manufacturing leaders
Real-time visibility, real-time action
Turn frontline teams into problem solvers with AI-powered checklists and work instructions, task tracking, and skills management.
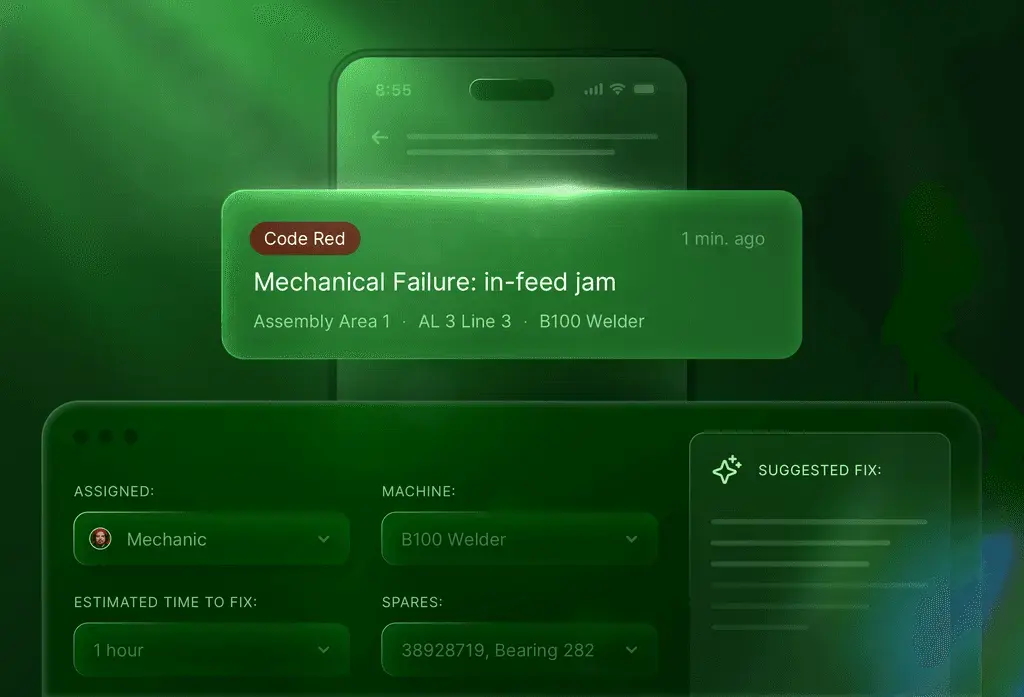
Data-driven decisions in the flow of work
Connect data with actions to keep lines running smoothly. Identify bottlenecks and root causes across teams and shifts.
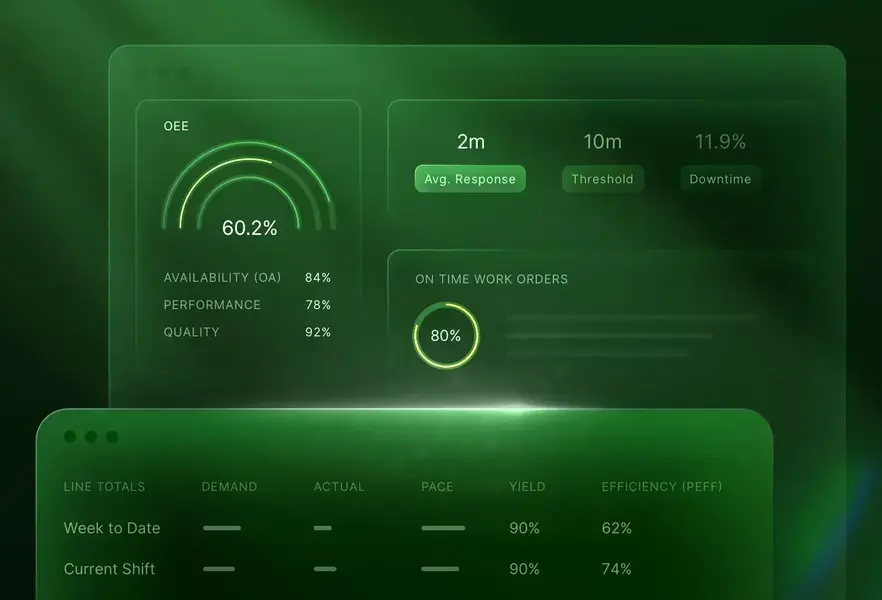
Problem-solving powered by AI
Share best practices and compare performance across global sites to build a culture of continuous improvement.
-1.webp)
Built for Continuous Improvement
Empower your frontline with digital workflows, preventive maintenance, and instant insights.
See ROI in 2 weeks
Reduced downtime, increased productivity, and better quality.
Engaged team members are an extra bonus.
Purple Mattress
HEINEKEN
JELD-WEN
Spartech
The process that sets us apart
We’ve spent decades identifying and proactively solving disruptions by shining a light on the root causes — and connecting people to actions.
Make issues visible and actionable for everyone to take the right action at the right time.
Ensure that the right people are notified and involved in problem-solving. Build a culture of problem-solving and continuous improvement with a motivated team of experts.
Track and analyze problem data to streamline processes and manufacture better-quality products across the organization.
Anticipate and address potential issues before they impact production. Prevent those problems from happening next time.
Get to the root cause of the issue and share what you learn across the entire organization so it never happens again.
Make issues visible and actionable for everyone to take the right action at the right time.
Ensure that the right people are notified and involved in problem-solving. Build a culture of problem-solving and continuous improvement with a motivated team of experts.
Track and analyze problem data to streamline processes and manufacture better-quality products across the organization.
Anticipate and address potential issues before they impact production. Prevent those problems from happening next time.
Get to the root cause of the issue and share what you learn across the entire organization so it never happens again.
Before, during, and after every shift
The only platform that unifies asset management, production performance, quality control, and team collaboration into one seamless solution.
“L2L is THE tool for transformation. It has everything... automated dispatches, standard work tools, data accuracy, historical data, dashboards...it's such a powerful tool. Everyone began using it right away. I’ve been part of software rollouts in the past, and I’ve never seen that eagerness. The moment they had the tablets in their hands and saw what L2L could do — getting updates, making work requests through Dispatches. They just took it and ran with it, never looking back.”
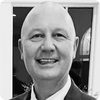
Plant General Manager
"Helps us confirm that people have the skills needed in order to operate a certain machine or process. It helps us see where skills gaps are, develop the people, and know what needs to be added in our training offer."
.png)
Senior Global Lead Supply Chain Capability Development
“What makes L2L so unique is the fact that the product was developed by real manufacturing users. People that truly understand the day-to-day issues and concerns that drive the production floor.”
.png)
Lean Maintenance Consultant
“The system has given our employees the tools to see the highest impact opportunities for improvement and a way to visually see the impact of actions taken to address them.”
VP of Engineering and Manufacturing
“L2L offers data at an extremely intuitive level. It’s actionable data. The report structures are so easy to manage that it allows for very easy determinations of cause and effect around failures”
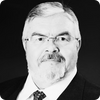
TPM Implementation Leader
“With L2L, ADAC captures and details hundreds of operational activities every day: from lab samples and first part checks to preventative and reactive equipment maintenance, calibrations, and beyond.”
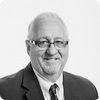
VP of Quality
“L2L is really a system focused on the people at the plant. That’s what struck a chord with us.”
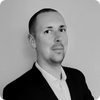
Head of Engineering
"We’ve tried literally dozens of other solutions, CMMS, and attempts at lean programs in the past 28 years, but this is the first one I’ve seen truly make a difference.”
CI Leader
Connect with your existing systems
Sync seamlessly with your ERP, inventory, and other production systems.

Our content hub
We create content about all things manufacturing, from TPM trends to shop floor management and supply chain optimization.