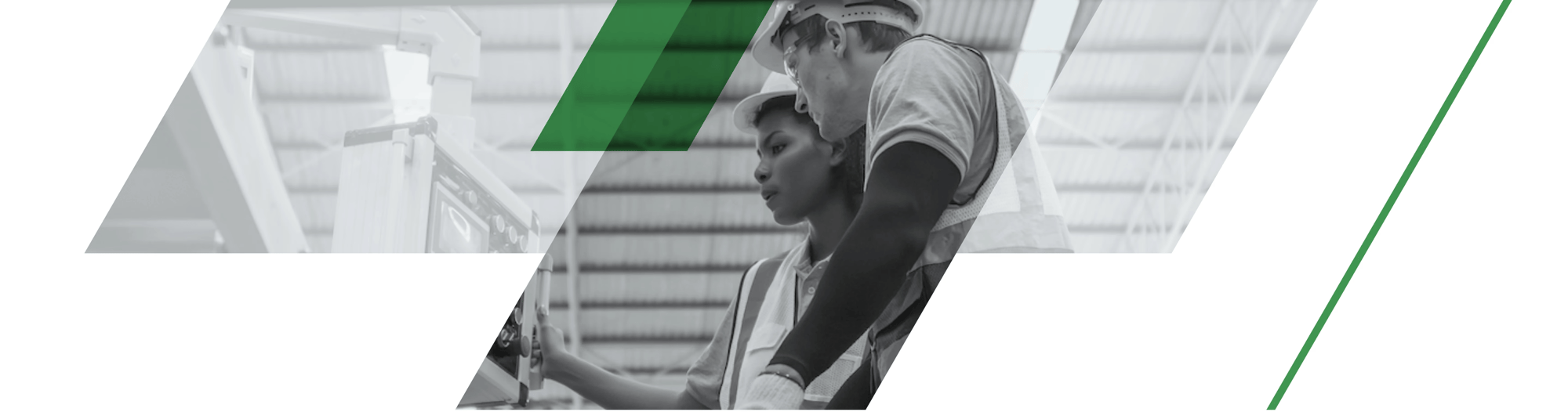
Joining Forces to Power
the Connected Workforce
Surpass your manufacturing goals across availability, performance, quality, and workforce. Say hello to the future of the connected workforce.
Used by 500k+ frontline employees worldwide
SO YOU AND YOUR TEAM CAN WIN THE DAY
Here's why L2L + SwipeGuide = Winning Combo
What needs to be done?
Track tasks, improve efficiency, and identify problems. Dispatches provide a clear record of everything that happens so you can analyze and continuously improve operations, task after task.
When & where?
Monitor and optimize operations in any area of your plant with AI-powered manufacturing tools. Optimize workflows, improve quality, and reduce costs with real-time insights and automation.
Who’s qualified?
Skills management lets you build and certify workforce capabilities. Address compliance issues by finding and closing skills gaps. Develop essential skills with on-the-job learning activities and assessments.
How should it be done?
Mobile-first job aids like visual work instructions and checklists preserve expert knowledge and reduce training time. Standardize work procedures and share best practices across teams, lines, and sites.
FOR FRONTLINE TEAMS
Get the job done right, every time. L2L provides enhanced task visibility with instant access to digital job aids for audits, inspections, and shop floor procedures.
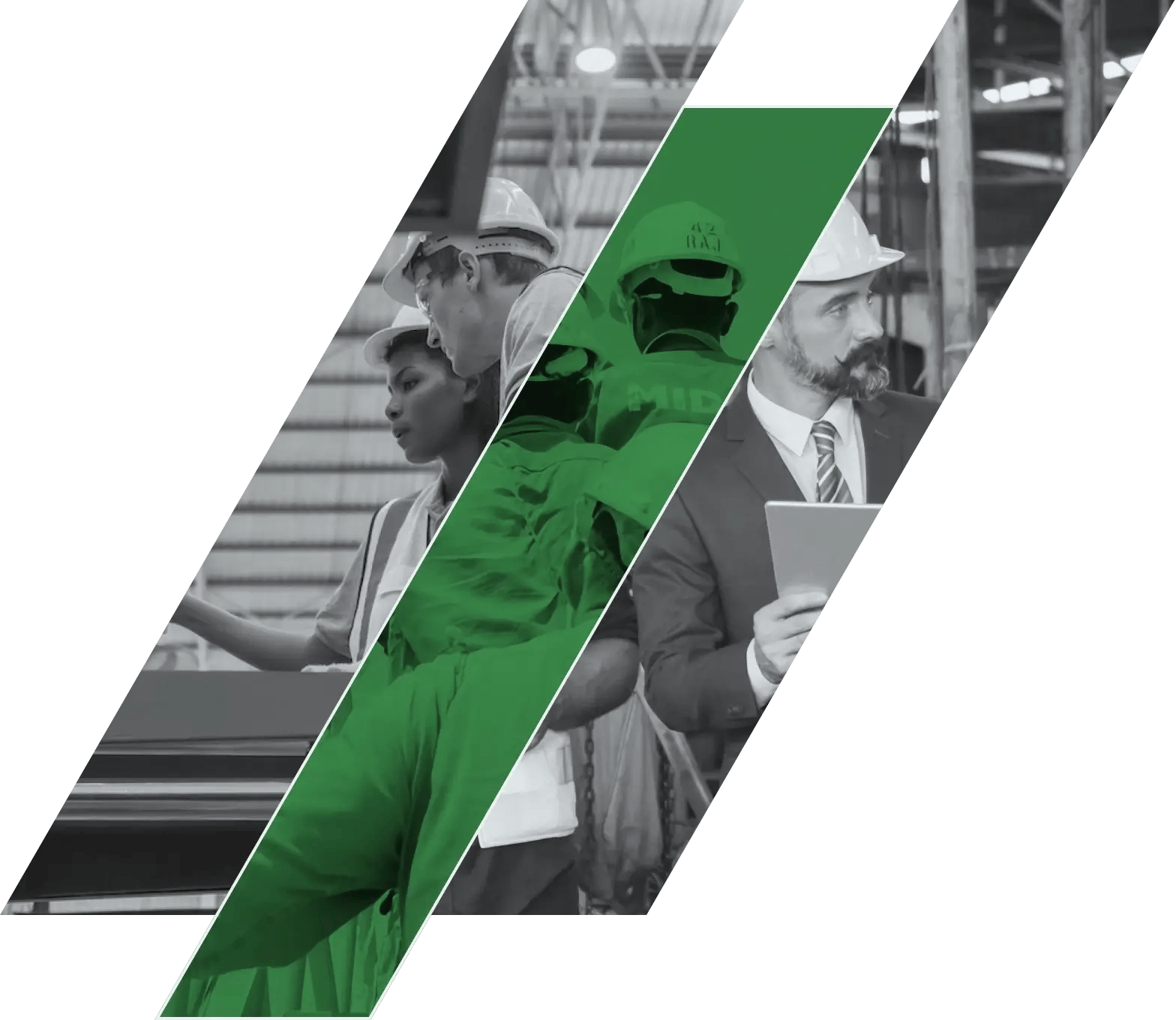
FOR THE C-SUITE
L2L enables data-driven decision-making through manufacturing intelligence, identifying disruptions, delivering insights, and automating action across all sites of the organization. From Seattle to Geneva.
…AND EVERYONE IN BETWEEN
Say goodbye to disruptions. Frontline supervisors and managers have access to machine data and workforce feedback to make sure all lines are running as they should and processes are continuously improving.
“Before L2L, finding the right data was distracting for the team. Now, the team can stay engaged. The presenter can focus on the team, and everyone can focus less on the data and more on the issues.”
Dir. Global Engineering, Oetiker
“The improvement in unplanned downtime exceeded our expectations. Once we started using L2L, other inefficiencies in our processes also became visible. Addressing these, along with the machine downtime, has resulted in close to a 30% reduction in overall downtime.”
Automotive Parts Manufacturer
”We made these incredible ROIs while implementing a tool that gives us confidence that everybody is doing exactly what they need to be doing, day in and day out.”
Production Manager, Orkla
-20%
downtime and disruptions
+20%
number of units produced
-50%
onboarding & training time
COOL, BUT I HAVE QUESTIONS
Your existing L2L modules and features will remain unchanged. However, over time, you'll benefit from the opportunity to expand functionalities around visual and mobile-first solutions for frontline training, work instructions, SOPs, and checklists.
SwipeGuide is now part of the L2L Connected Workforce ecosystem. No action is required from you. Your experience will remain unchanged, but in the future you can expect even better tools to streamline all aspects of your operations through real-time visibility and collaboration that drive availability, performance, and quality at your plant.
If you're an existing customer, please book a call with your customer success manager.
If you're new to L2L, please fill in the form below to learn more.